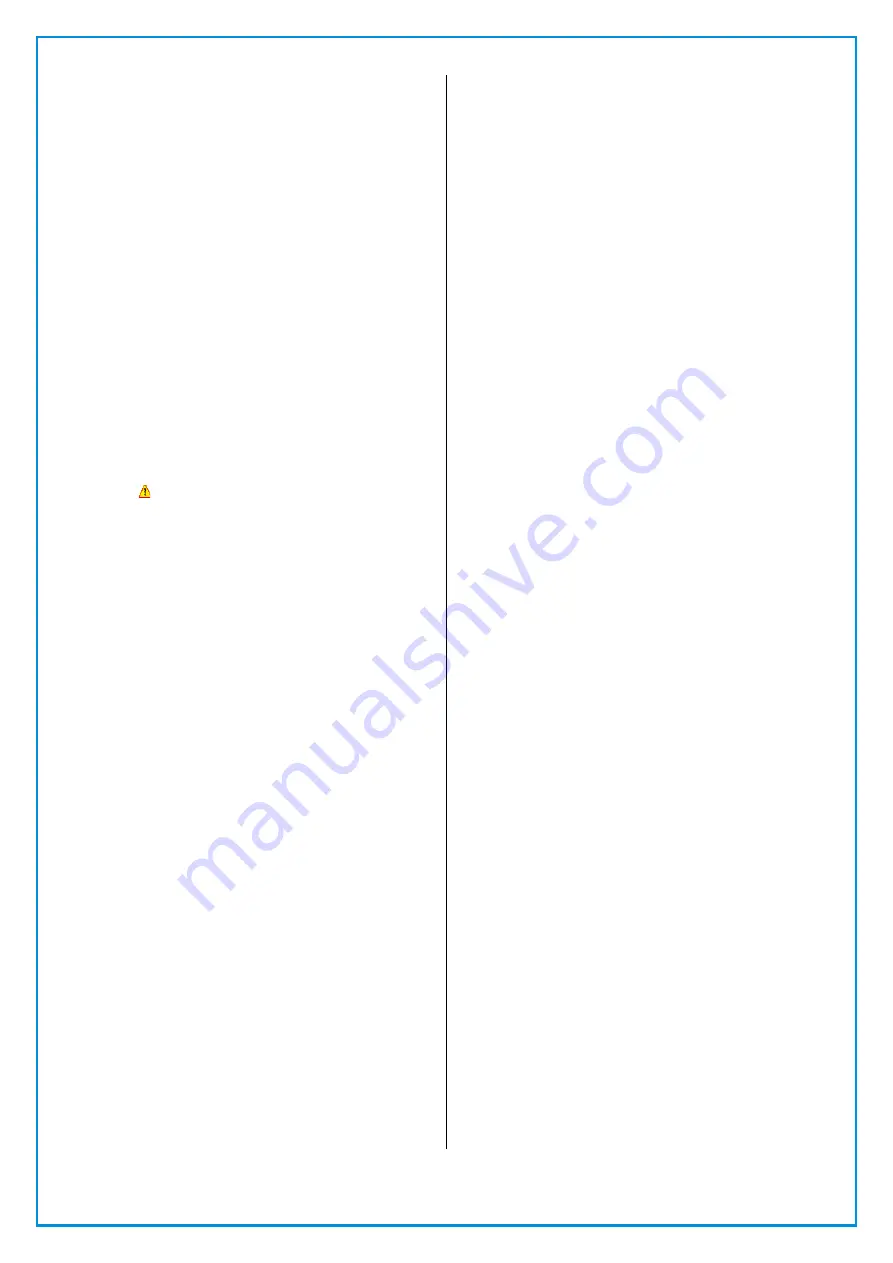
- 1 –
ZVP-PC-0068-00-R2
1.0
GENERAL INFORMATION
1.1
Panblast notice to purchasers and users
1.1.1
All products and equipment designed and
manufactured by Panblast are intended for use
by experienced users of abrasive blasting
equipment and its associated operations and
abrasive blasting media.
1.1.2
It is the responsibility of the user to:
- Determine if the equipment and abrasive
media are suitable for the users' intended
use and application.
- Familiarize themselves with any appropriate
laws, regulations and safe work practices,
which may apply within the users working
environment.
- Provide appropriate operator training and a
safe working environment including
operator protective equipment such as, but
not limited to, safety footwear, protective
eyewear and hearing protection.
1.1.3
Panblast Standard Terms and Conditions of Sale
apply. Contact your local Panblast office should
you require any further information or
assistance.
1.2
! WARNING! – READ THIS SECTION
CAREFULLY BEFORE USING THIS
EQUIPMENT/APPARATUS.
1.2.1
Heavy metal paint, asbestos and other toxic
material dusts will cause serious lung disease or
death without the use of properly designed and
approved supplied air respiratory equipment
(SAR) by blast operators and all personnel within
the work site area.
1.2.2
The compressor must have adequate output and
the plumbing between the compressor and the
point of attaching the air supply hose must have
sufficient capacity to supply the volume of air at
the pressure required.
1.3
Standard safety precautions
1.3.1
Approved safety eyewear, hearing and footwear
protection should be worn at all times by the
operator and anyone else in the immediate area
that may be exposed to any hazards generated
by the abrasive blasting process.
1.3.2
Suitably approved respiratory protection should
also be worn when handling abrasive media,
abrasive refuse dust and when carrying out any
service/maintenance work where any dust may
be present.
1.3.3
Any work performed on electrical wiring or
components must only be carried out by
suitably qualified and registered electrical trades
personnel.
1.3.4
Under no circumstances should any safety
interlocks / lockouts or features be altered or
disabled in any way.
1.3.5
All equipment must be isolated from the
compressed air supply and electrical power prior
to any service or maintenance work being
carried out.
1.3.6
All care must be taken by the operator(s) when
lifting or moving equipment or components in
order to prevent injury. Blast pots must always
be emptied of abrasive media before any
attempt is made to move them.
1.3.7
Any modification of the equipment and/or
components or use of non-genuine PanBlast™
replacement parts will void warranty.
1.3.8
Always check the Material Safety Data Sheet
(MSDS) on the abrasive media being used to
ensure that it is free of harmful substances, in
particular, free silica, cyanide, arsenic or lead.
1.3.9
Test the surface that is to be blasted for harmful
substances, taking the appropriate measures to
ensure the safety of the operator and others.
1.3.10
The operator should carry out a daily inspection
of all related components prior to startup of all
wearing and safety items to ensure they are in
correct operating order. In particular check all
hose couplings and nozzle holders, ensuring
that all hose couplings are fitted correctly, the
safety locking pins are engaged and in good
order. Always install safety whip check cables at
every hose connection. Ensure that the blast
nozzle has been securely screwed into the
nozzle holder and the nozzle holder has been
secured to the blast hose correctly and all
screws are engaged.
NOTE: UNDER OSHA 1915:34(c)(1)(iv) DEAD
MAN CONTROL. A DEADMAN CONTROL
DEVICE SHALL BE PROVIDED AT THE NOZZLE
END OF THE BLAST HOSE EITHER TO PROVIDE
DIRECT CUTOFF OR TO SIGNAL THE POT
TENDER BY MEANS OF A VISUAL AND
AUDIBLE SIGNAL TO CUT OFF THE FLOW, IN
THE EVENT THE BLASTER LOSES CONTROL OF
THE HOSE. THE POT TENDER SHALL BE
AVAILABLE AT ALL TIMES TO RESPOND
IMMEDIATELY TO THE SIGNAL.
2.0
INTRODUCTION
2.1
The Tornado Internal Pipe Blasting Tool Set is
designed to clean the internal surfaces of pipes
from 200mm (8”) to 900mm (36”) I.D.
The tool
is connected to a pipe lance that is coupled to a
standard blast hose in place of the blast nozzle.
A carriage fitted to the tool supports the tool
and centers it within the pipe, the tool is
positioned at the far end of the pipe and slowly
withdrawn, as the tool travels down the pipe
abrasive media is thrown from a twin nozzle
rotating blast head. The speed of the rotating
head is controlled by a centrifugal speed limiter.
There are three types of centering carriages
available to suit small, medium and large
diameter pipes.
Refer to the charts below for the centering
carriage assemblies, blast nozzles and air
requirements to suit various applications.