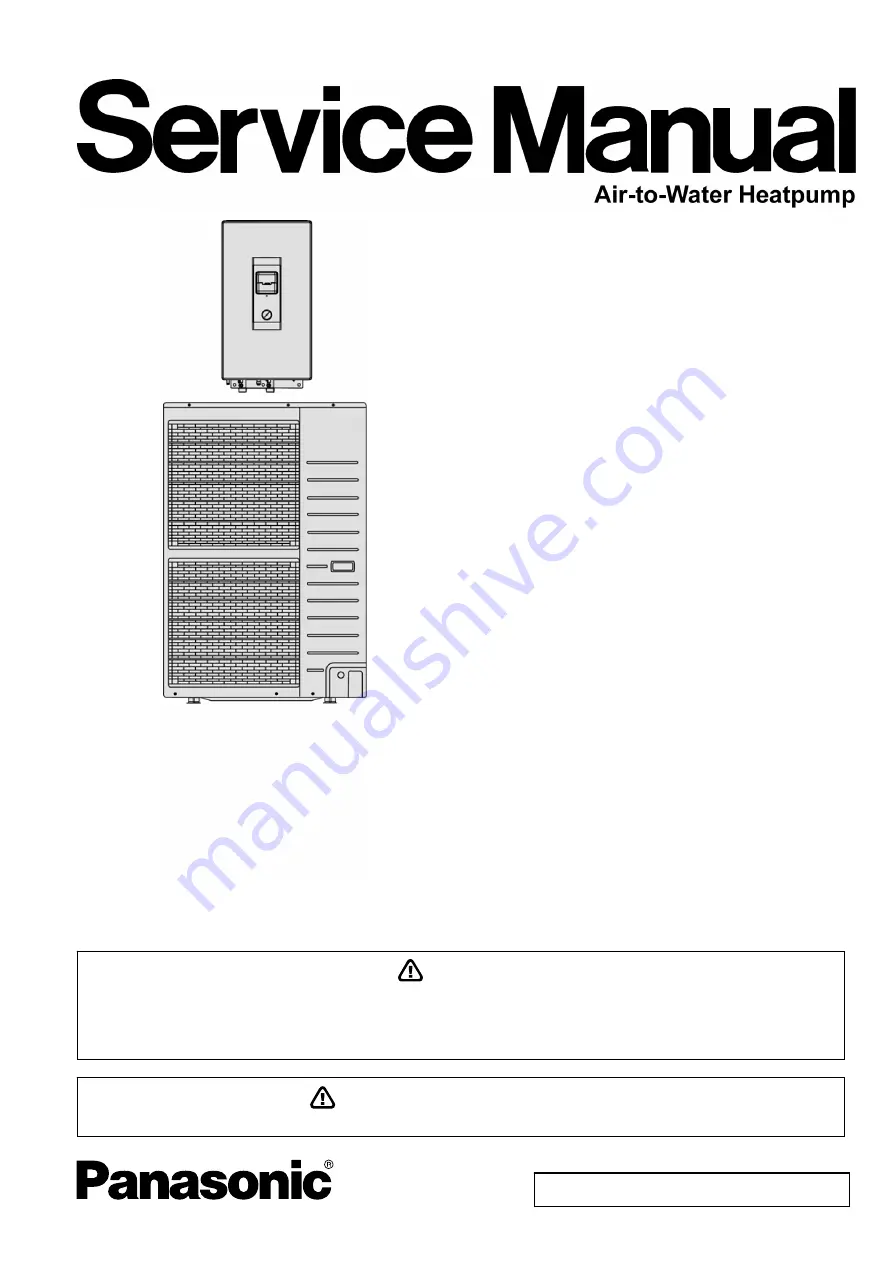
© Panasonic HA Air-Conditioning (M) Sdn. Bhd. 2011.
Unauthorized copying and distribution is a violation of law.
Order No. PHAAM1108115C2
Indoor Unit
Outdoor Unit
WH-SXH09D0E8 WH-UX09DN8
PRECAUTION OF LOW TEMPERATURE
In order to avoid frostbite, be assured of no refrigerant leakage during the installation or repairing of refrigerant circuit.
WARNING
This service information is designed for experienced repair technicians only and is not designed for use by the general public.
It does not contain warnings or cautions to advise non-technical individuals of potential dangers in attempting to service a product.
Products powered by electricity should be serviced or repaired only by experienced professional technicians. Any attempt to
service or repair the product or products dealt with in this service information by anyone else could result in serious injury or death.
Summary of Contents for WH-SXH09D0E8
Page 8: ...8 4 Location of Controls and Components 4 1 Indoor Unit 4 1 1 Location of Control ...
Page 9: ...9 ...
Page 10: ...10 ...
Page 11: ...11 4 1 2 Weekly Timer Setting ...
Page 12: ...12 4 1 3 Main Components 4 2 Outdoor Unit ...
Page 13: ...13 5 Dimensions 5 1 Indoor Unit ...
Page 14: ...14 5 2 Outdoor Unit ...
Page 16: ...16 7 Block Diagram ...
Page 17: ...17 8 Wiring Connection Diagram 8 1 Indoor Unit ...
Page 18: ...18 8 2 Outdoor Unit ...
Page 19: ...19 9 Electronic Circuit Diagram 9 1 Indoor Unit ...
Page 20: ...20 9 2 Outdoor Unit ...
Page 21: ...21 10 Printed Circuit Board 10 1 Indoor Unit 10 1 1 Main Printed Circuit Board ...
Page 22: ...22 10 2 Outdoor Unit 10 2 1 Main Printed Circuit Board ...
Page 23: ...23 10 2 2 Noise Filter Printed Circuit Board ...
Page 77: ...77 17 3 To Remove Pressure Gauge 17 4 To Remove Control Panel ...
Page 78: ...78 17 5 To Remove RCCB 17 6 To Remove Transformer and Electronic Controller Board ...
Page 80: ...80 When reinstall the water pipe use grease or water at the joining ...
Page 86: ...86 19 2 Outdoor Unit ...
Page 87: ...87 ...