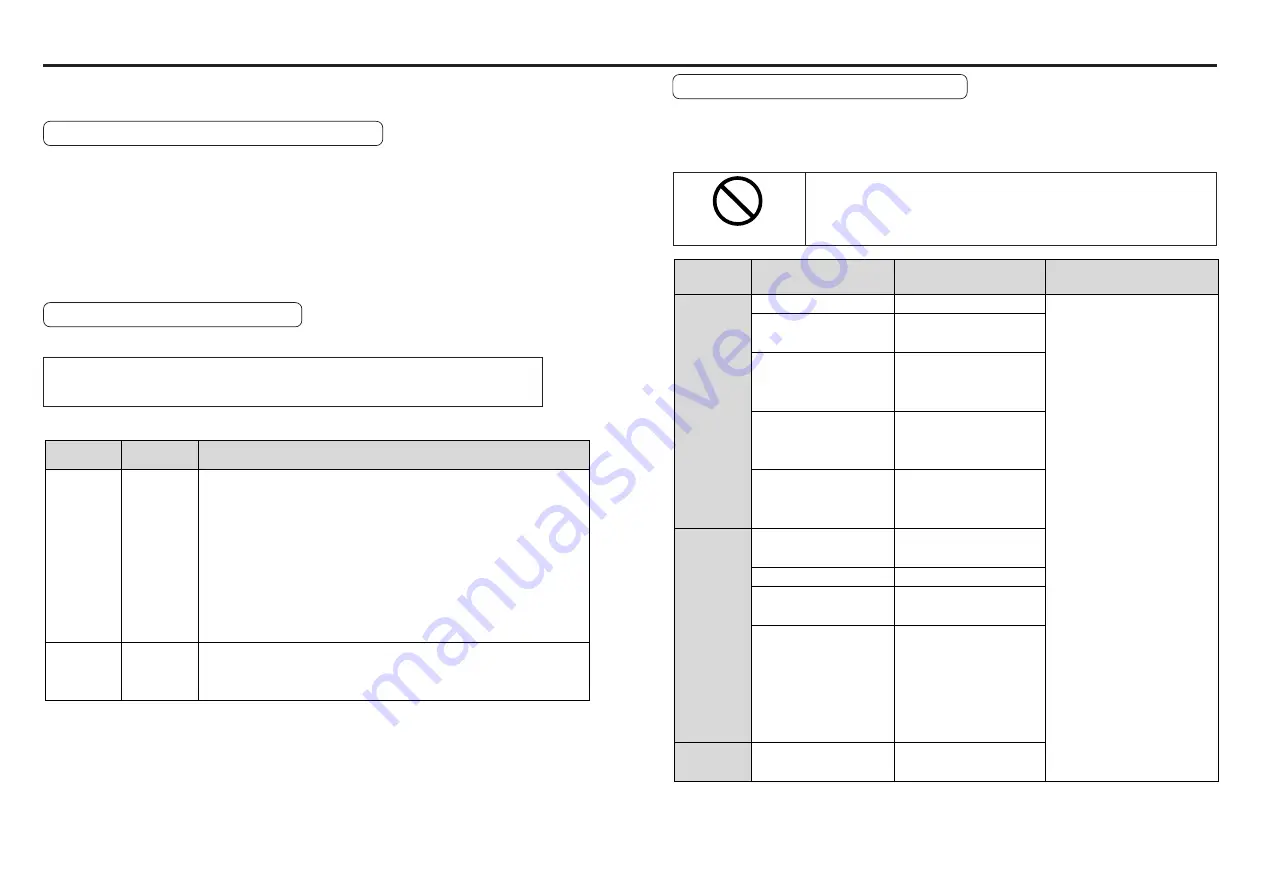
– B39 –
– B38 –
Prohibited
Disassembling for inspection and repair should
be carried out only by authorized dealers or ser-
vice company.
Daily
Annual
• Ambient temperature, humidity, speck, dust or foreign object
• Abnormal vibration and noise
• Main circuit voltage
• Odor
• Lint or other particles at air holes
• Cleanness at front portion of the driver and connecter
• Damage of the cables
• Loose connection or misalignment between the motor and
machine or equipment
• Pinching of foreign object at the load
• Loose tightening
• Trace of overheat
• Damage of the terminals
Type
Cycles
Items to be inspected
Daily
inspection
Periodical
inspection
Driver
Motor
Motor with
gear reducer
Smoothing condenser
Cooling fan
Aluminum electrolytic
capacitor (on PCB)
Rush current
preventive relay
Rush current
preventive resistor
Bearing
Oil seal
Encoder
Battery
for absolute encoder
Gear reducer
Approx. 5 years
2 to 3 years
(10,000 to 30,000 hours)
Approx. 5 years
Approx. 100,000 times
(depending on working
condition)
Approx. 20,000 times
(depending on working
condition)
3 to 5 years
(20,000 to 30,000 hours)
5000 hours
3 to 5 years
(20,000 to 30,000 hours)
Life time varies depending
on working conditions.
Refer to the instruction
manual attached to the
battery for absolute
encoder.
10,000 hours
Product
Component
Standard replacement
cycles (hour)
Note
These hours or cycles are
reference.
When you experience any
error, replacement is re-
quired even before this
standard replacement cy-
cle.
6. Maintenance and Inspections
• Routine maintenance and inspection of the driver and motor are essential for the
proper and safe operation.
Notes on Maintenance and Inspection
1) Turn on and turn off should be done by operators or inspectors themselves.
2) Internal circuit of the driver is kept charged with high voltage for a while even after
power-off. Turn off the power and allow 15 minutes or longer after LED display of the
front panel has gone off, before performing maintenance and inspection.
3) Disconnect all of the connection to the driver when performing megger test (Insulation
resistance measurement) to the driver, otherwise it could result in breakdown of the
driver.
Inspection Items and Cycles
General and normal running condition
Ambient conditions : 30˚C (annual average), load factor of 80%
or lower, operating hours of 20 hours or less per day.
Perform the daily and periodical inspection as per the items below.
<Notes>
Inspection cycle may change when the running conditions of the above change.
Guideline for Parts Replacement
Use the table below for a reference. Parts replacement cycle varies depending on the
actual operating conditions. Defective parts should be replaced or repaired when any
error have occurred.