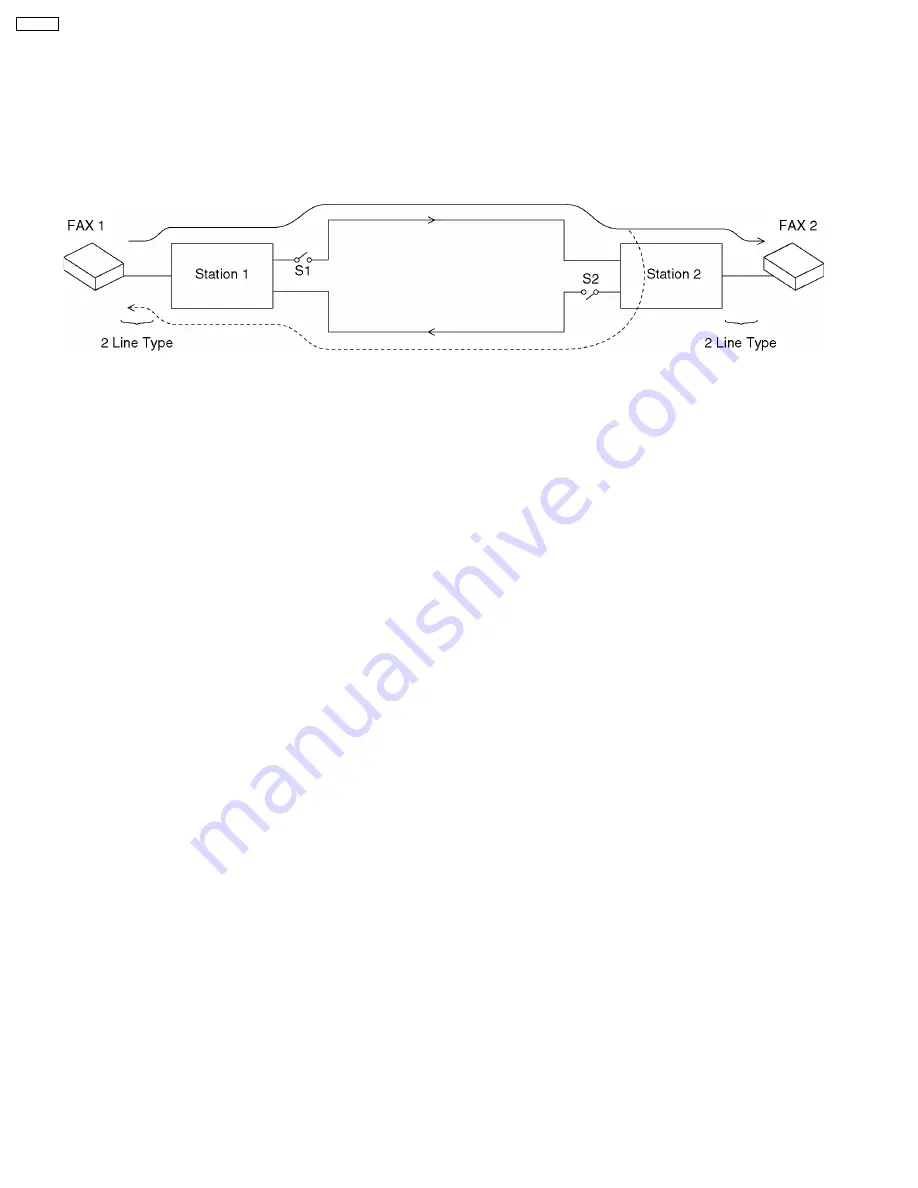
(Cause and Countermeasure)
As shown in the chart above, the total handshaking time must be reduced, but because of the long distance connection and linking
of several stations, the line connection time cannot be reduced. Accordingly, the following countermeasures should be tried.
(A)... As the 35 sec. count is started directly after dialing or directly after the START button has been pressed for models with a
START button, the other party should be called manually, if possible. Another possibility is entering two pauses at the end of the
auto dial number on the transmission side. Then the count start time can be delayed for 2 pauses (about 10 sec.).
Cause 2:
Erroneous detection because of an echo or an echo canceler.
(Echo/Echo Canceler)
The signal from FAX1 reaches FAX2 via stations 1 and 2, but the reflection signal at station 2 also returns via station 1 (echo). As
the distance between station 1 and station 2 is far, the echo returns to FAX 1 at a max of 600 msec after transmission. There is
a possibility that this signal is detected erroneously as the signal from FAX2. For a normal call, there is also a possibility that the
echo of their own voice will make the call difficult to understand. For this reason, each station (station 1 and station 2) attaches echo
cancelers (S1 and S2) for international lines or long distance lines. For the echo canceler, the level of the transmission signal from
FAX 1 is compared with the level of the reception signal from FAX2. When the transmission signal is larger, S1 is closed while S2
is opened when it is smaller. In other words, for transmission from FAX1, S1 is closed and S2 is open, so that the echo does not
return to FAX1.
(Causes and Countermeasures)
(Cause A)
When a training signal is transmitted from FAX1 during the communication procedure at the time of transmission from FAX1 to
FAX2, there is a delay until the echo canceler operates. S1 is closed so that a part of the head of the training signal may drop out.
Normal reception by FAX2 may not be possible, and transmission may not be started.
(Countermeasure A)
When the international line mode is ON in the service mode (code No. 521), a dummy signal is attached to the head of the training
signal to prevent this problem. As this is normally ON, it is necessary to reconfirm that this has not become OFF. When the
international mode is switched OFF, the transmission side will try the training signal three times at each speed (9600BPS, 4800BPS
and 2400BPS). If NG, it will drop the speed by one rank (fall-back). When the international mode is switched ON, each speed will
be tried only twice. In other words, the slower speed with fewer errors can be accessed more easily. This is done because the line
conditions may deteriorate and the picture may be disturbed more easily during communication for international lines or long
distance communication, even when the training is OK. The default value is ON as preference is given to clearer pictures rather
than speed.
(Cause B)
The echo canceler operation stops with a 2100Hz signal. (i.e. S1 and S2 become ON). Accordingly, when FAX1 has executed
automatic reception, a CED signal is output. If this signal is 2100Hz, S1 and S2 will become ON. Then the echo of the DIS signal
output afterwards may be received and FAX1 may execute an erroneous operation, preventing communication from starting.
(Countermeasure B)
In the service mode, the CED signal frequency is set to 1100 Hz (code No.520), or the time setting between the CED signal and
the DIS signal is set from 75 msec to 500 msec in the service mode (code No.593). This is because the echo canceler operation
stop mode is canceled by an interval of 250 msec or more.
Reduce receiving sensitivity to reduce the effect of RCV echo signal. (Service mode: code No. 598)
52
KX-FP85
Summary of Contents for KX-FP85
Page 8: ...1 11 TEST CHART 1 11 1 ITU T No 1 TEST CHART 8 KX FP85 ...
Page 9: ...1 11 2 ITU T No 2 TEST CHART 9 KX FP85 ...
Page 11: ...1 12 2 CONTROL PANEL 11 KX FP85 ...
Page 22: ...1 15 2 MAINTENANCE CHECK ITEMS COMPONENT LOCATIONS 22 KX FP85 ...
Page 33: ...2 3 3 1 SIMPLE CHECK LIST CROSS REFERENCE 2 5 TEST FUNCTIONS P 103 33 KX FP85 ...
Page 43: ...Fig C 43 KX FP85 ...
Page 55: ...55 KX FP85 ...
Page 56: ...CROSS REFERENCE 2 5 TEST FUNCTIONS P 103 56 KX FP85 ...
Page 57: ...CROSS REFERENCE 2 5 TEST FUNCTIONS P 103 57 KX FP85 ...
Page 58: ...CROSS REFERENCE 2 5 TEST FUNCTIONS P 103 58 KX FP85 ...
Page 59: ...CROSS REFERENCE 2 5 TEST FUNCTIONS P 103 59 KX FP85 ...
Page 60: ...60 KX FP85 ...
Page 61: ...61 KX FP85 ...
Page 62: ...CROSS REFERENCE 2 5 TEST FUNCTIONS P 103 62 KX FP85 ...
Page 68: ...NG Wave pattern Refer to NG EXAMPLE 68 KX FP85 ...
Page 70: ...I O and Pin No Diagram 70 KX FP85 ...
Page 74: ...2 3 6 3 NG EXAMPLE 74 KX FP85 ...
Page 75: ...2 3 6 4 CHECK THE STATUS OF THE DIGITAL BOARD 75 KX FP85 ...
Page 78: ...4 No tone dialing CROSS REFERENCE 2 3 7 1 CHECK SHEET P 76 78 KX FP85 ...
Page 80: ...CROSS REFERENCE 2 3 7 ANALOG BOARD SECTION P 76 80 KX FP85 ...
Page 82: ...2 3 9 2 TOROUBLESHOOTING FLOW CHART 82 KX FP85 ...
Page 87: ...87 KX FP85 ...
Page 88: ...2 3 13 THERMAL HEAD SECTION Refer to 6 4 3 THERMAL HEAD P 142 88 KX FP85 ...
Page 97: ... 47 NUMBER OF IQ FAX PAGES TRANSMITTED 97 KX FP85 ...
Page 101: ...2 4 7 3 PRINTOUT EXAMPLE 101 KX FP85 ...
Page 102: ...102 KX FP85 ...
Page 106: ...2 5 3 PRINT TEST PATTERN 1 Platen roller Reference pattern 106 KX FP85 ...
Page 107: ...2 Left margin Top margin Reference pattern 107 KX FP85 ...
Page 108: ...3 Thermal head 1 dot Reference pattern 108 KX FP85 ...
Page 111: ...4 DISASSEMBLY INSTRUCTIONS 4 1 HOW TO REMOVE THE BOTTOM FRAME 111 KX FP85 ...
Page 112: ...4 2 HOW TO REMOVE THE OPERATION PANEL BLOCK 112 KX FP85 ...
Page 113: ...4 3 HOW TO REMOVE THE OPERATION BOARD AND LCD 113 KX FP85 ...
Page 114: ...4 4 HOW TO REMOVE THE ANALOG DIGITAL AND POWER BOARDS AND AC INLET 114 KX FP85 ...
Page 115: ...4 5 HOW TO REMOVE THE MOTOR BLOCK 115 KX FP85 ...
Page 116: ...116 KX FP85 ...
Page 117: ...4 6 HOW TO REMOVE THE SEPARATION ROLLER 117 KX FP85 ...
Page 118: ...4 7 HOW TO REMOVE THE IMAGE SENSOR CIS 118 KX FP85 ...
Page 119: ...4 8 HOW TO REMOVE THE TERMAL HEAD 119 KX FP85 ...
Page 120: ...4 9 HOW TO REMOVE THE PLATEN ROLLER BACK COVER 120 KX FP85 ...
Page 121: ...4 10 HOW TO REMOVE THE PICKUP ROLLER 121 KX FP85 ...
Page 122: ...4 11 HOW TO REMOVE THE CASSETTE PLATE 122 KX FP85 ...
Page 123: ...4 12 HOW TO REMOVE THE DOCUMENT TRAY 123 KX FP85 ...
Page 124: ...4 13 INSTALLATION POSITION OF THE LEAD WIRES 124 KX FP85 ...
Page 127: ...6 CIRCUIT OPERATIONS 6 1 CONNECTION DIAGRAM 127 KX FP85 ...
Page 129: ...6 2 1 GENERAL BLOCK DIAGRAM CROSS REFERENCE 6 7 1 ANALOG UNIT BLOCK DIAGRAM P 167 129 KX FP85 ...
Page 130: ...6 3 CONTROL SECTION 6 3 1 BLOCK DIAGRAM 130 KX FP85 ...
Page 131: ...6 3 2 MEMORY MAP 131 KX FP85 ...
Page 141: ...6 4 2 BLOCK DIAGRAM 141 KX FP85 ...
Page 143: ...143 KX FP85 ...
Page 167: ...6 7 1 ANALOG UNIT BLOCK DIAGRAM 167 KX FP85 ...
Page 171: ...171 KX FP85 ...
Page 178: ...7 TERMINAL GUIDE OF THE IC S TRANSISTORS AND DIODES 178 KX FP85 ...
Page 179: ...8 FIXTURES AND TOOLS 179 KX FP85 ...
Page 180: ...9 CABINET MECHANICAL AND ELECTRICAL PARTS LOCATION 9 1 OPERATION PANEL SECTION 180 KX FP85 ...
Page 181: ...9 2 UPPER CABINET SECTION 181 KX FP85 ...
Page 182: ...9 2 1 BACK COVER SECTION 9 2 1 1 BACK COVER 1 182 KX FP85 ...
Page 183: ...9 2 1 2 BACK COVER 2 183 KX FP85 ...
Page 184: ...9 3 LOWER P C B SECTION CROSS REFERENCE 4 1 HOW TO REMOVE THE BOTTOM FRAME P 111 184 KX FP85 ...
Page 185: ...9 4 MOTOR SECTION 9 5 ACTUAL SIZE OF SCREWS AND WASHER 185 KX FP85 ...
Page 186: ...10 ACCESSORIES AND PACKING MATERIALS 186 KX FP85 ...
Page 196: ...12 1 MEMO 196 KX FP85 ...