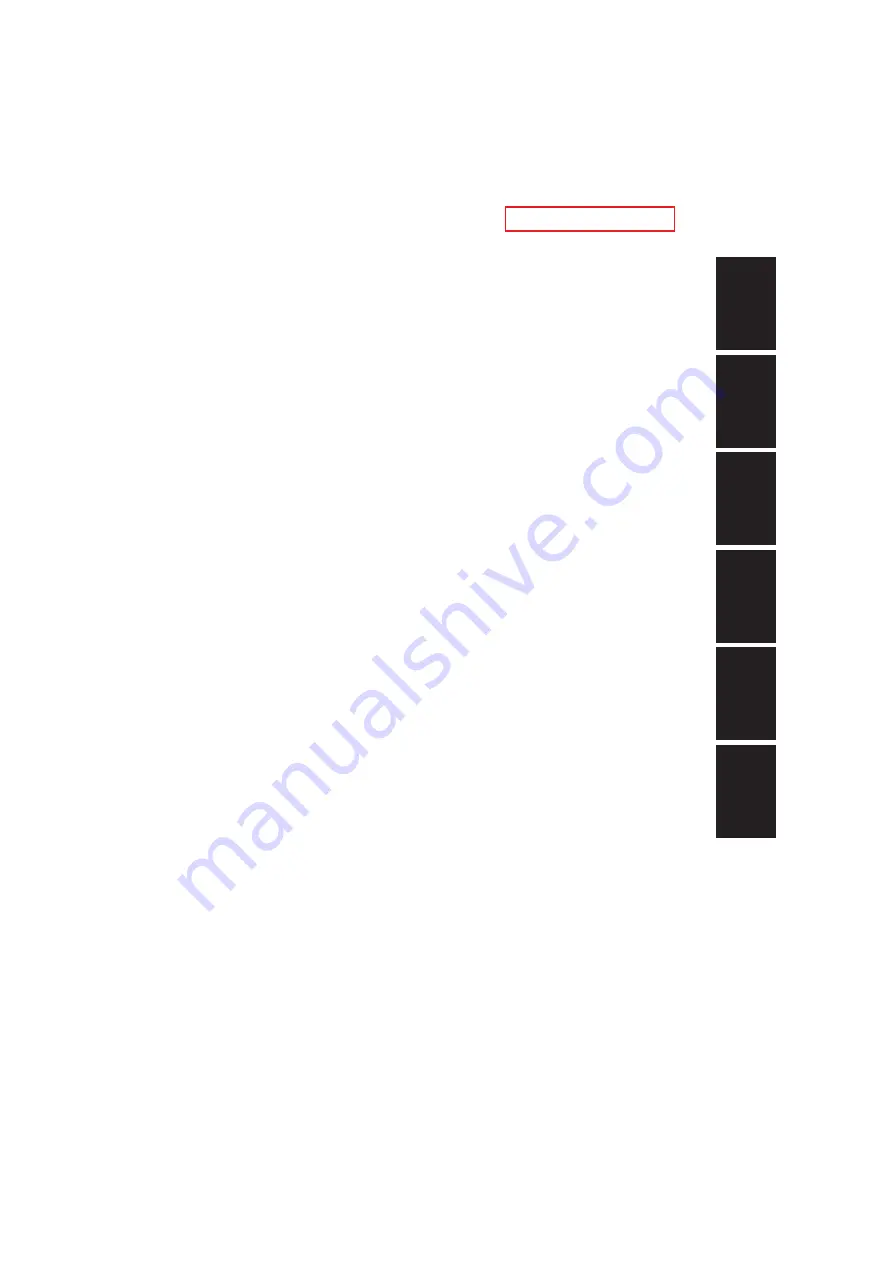
FA-F320
Contents / Index
2.2 Paper Transport Mechanism ..................................................................
2.3 Punching Mechanism .............................................................................
2.4 Jogging Offset Mechanism .....................................................................
3.3 Cleaning recommendations ....................................................................
3.5 Diassembly and Assembly ......................................................................
4.1 Electrical Parts (Functions of Switches and Sensors) ............................
5.1 Error detection by self-diagnostics ..........................................................
Electrical
Preventive
Maintenance
Operation
Introduction
Unpacking/
Installation
Troubleshooting
FA-F320