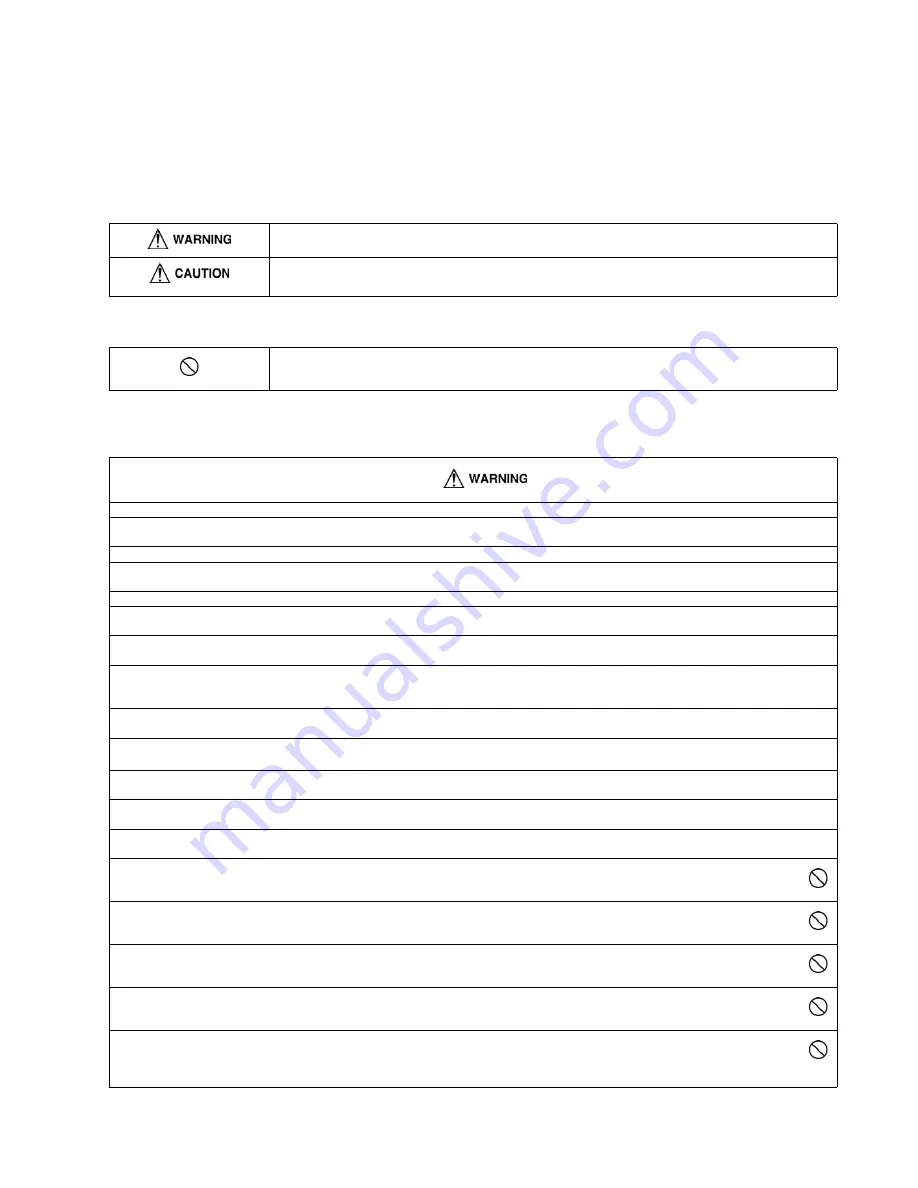
3
1 Safety Precautions
• Read the following “SAFETY PRECAUTIONS” carefully before perform any servicing.
• Electrical work must be installed or serviced by a licensed electrician. Be sure to use the correct rating of the power plug and
main circuit for the model installed.
• The caution items stated here must be followed because these important contents are related to safety. The meaning of each
indication used is as below. Incorrect installation or servicing due to ignoring of the instruction will cause harm or damage, and
the seriousness is classified by the following indications.
• The items to be followed are classified by the symbols:
• Carry out test run to confirm that no abnormality occurs after the servicing. Then, explain to user the operation, care and
maintenance as stated in instructions. Please remind the customer to keep the operating instructions for future reference.
This indication shows the possibility of causing death or serious injury.
This indication shows the possibility of causing injury or damage to properties.
This symbol denotes item that is PROHIBITED from doing.
1. Do not modify the machine, part, material during repairing service.
2. If wiring unit is supplied as repairing part, do not repair or connect the wire even only partial wire break. Exchange the whole wiring
unit.
3. Do not wrench the fasten terminal. Pull it out or insert it straightly.
4. Engage dealer or specialist for installation and servicing. If installation of servicing done by the user is defective, it will cause water
leakage, electrical shock or fire.
5. Install according to this installation instructions strictly. If installation is defective, it will cause water leakage, electrical shock or fire.
6. Use the attached accessories parts and specified parts for installation and servicing. Otherwise, it will cause the set to fall, water
leakage, fire or electrical shock.
7. Install at a strong and firm location which is able to withstand the set’s weight. If the strength is not enough or installation is not
properly done, the set will drop and cause injury.
8. For electrical work, follow the local national wiring standard, regulation and the installation instruction. An independent circuit and
single outlet must be used. If electrical circuit capacity is not enough or defect found in electrical work, it will cause electrical shock or
fire.
9. This equipment is strongly recommended to install with Earth Leakage Circuit Breaker (ELCB) or Residual Current Device (RCD).
Otherwise, it may cause electrical shock and fire in case equipment breakdown or insulation breakdown.
10. Use the specified cable 4
u
1.5 mm
2
, and connect tightly for indoor/outdoor connection. Connect tightly and clamp the cable so that
no external force will be acted on the terminal. If connection or fixing is not perfect, it will cause heat-up or fire at the connection.
11. Wire routing must be properly arranged so that control board cover is fixed properly. If control board cover is not fixed perfectly, it will
cause heat-up or fire at the connection point of terminal, fire or electrical shock.
12. When carrying out piping connection, take care not to let air substances other than the specified refrigerant go into refrigeration cycle.
Otherwise, it will cause lower capacity, abnormal high pressure in the refrigeration cycle, explosive and injury.
13. Do not install outdoor unit near handrail of veranda. When installing air-conditioner unit at veranda of high rise building, child may
climb up to outdoor unit and cross over the handrail and causing accident.
14. This equipment must be properly earthed. Earth line must not be connected to gas pipe, water pipe, earth of lightning rod and
telephone. Otherwise, it may cause electric shock in case equipment breakdown or insulation breakdown.
15. Keep away from small children, the thin film may cling to nose and mouth and prevent breathing.
16. Do not damage or use unspecified power supply cord. Otherwise it will cause fire or electric shock.
17. Do not modify the length of the power supply cord or use of the extension cord, and do not share the single outlet with other electrical
appliances. Otherwise, it will cause fire or electrical shock.
18. In case of using existing (R22) pipes during installation of R410 models, must carry out pump down properly to collect back the
refrigerant and oil before installation new unit.
Thickness of copper pipes used with R410A must be more than 0.8 mm. Never use copper pipes thinner than 0.8 mm.
It is desirable that the amount of residual oil is less than 40 mg/10m.
Summary of Contents for CS-RE18JKE
Page 9: ...9 4 Location of Controls and Components 4 1 Indoor Unit 4 2 Outdoor Unit 4 3 Remote Control...
Page 10: ...10 5 Dimensions 5 1 Indoor Unit Remote Control...
Page 11: ...11 5 2 Outdoor Unit 5 2 1 CU RE18JKE...
Page 12: ...12 5 2 2 CU RE24JKE...
Page 13: ...13 6 Refrigeration Cycle Diagram...
Page 14: ...14 7 Block Diagram 7 1 CS RE18JKE CU RE18JKE...
Page 15: ...15 7 2 CS RE24JKE CU RE24JKE...
Page 16: ...16 8 Wiring Connection Diagram 8 1 Indoor Unit...
Page 17: ...17 8 2 Outdoor Unit 8 2 1 CU RE18JKE...
Page 18: ...18 8 2 2 CU RE24JKE...
Page 19: ...19 9 Electronic Circuit Diagram 9 1 Indoor Unit...
Page 20: ...20 9 2 Outdoor Unit 9 2 1 CU RE18JKE...
Page 21: ...21 9 2 2 CU RE24JKE...
Page 22: ...22 10 Printed Circuit Board 10 1 Indoor Unit 10 1 1 Main Printed Circuit Board...
Page 23: ...23 10 1 2 Power Printed Circuit Board 10 1 3 Indicator Printed Circuit Board...
Page 24: ...24 10 2 Outdoor Unit 10 2 1 Main Printed Circuit Board 10 2 1 1 CU RE18JKE...
Page 25: ...25 10 2 2 Main Printed Circuit Board 10 2 2 1 CU RE24JKE...
Page 26: ...26 10 2 3 Power Printed Circuit Board 10 2 3 1 CU RE24JKE...
Page 76: ...76 16 1 3 To remove power electronic controller...
Page 77: ...77 16 1 4 To remove discharge grille 16 1 5 To remove control board...
Page 78: ...78 16 1 6 To remove cross flow fan and indoor fan motor...
Page 79: ...79...
Page 90: ...90 18 Exploded View and Replacement Parts List 18 1 Indoor Unit...