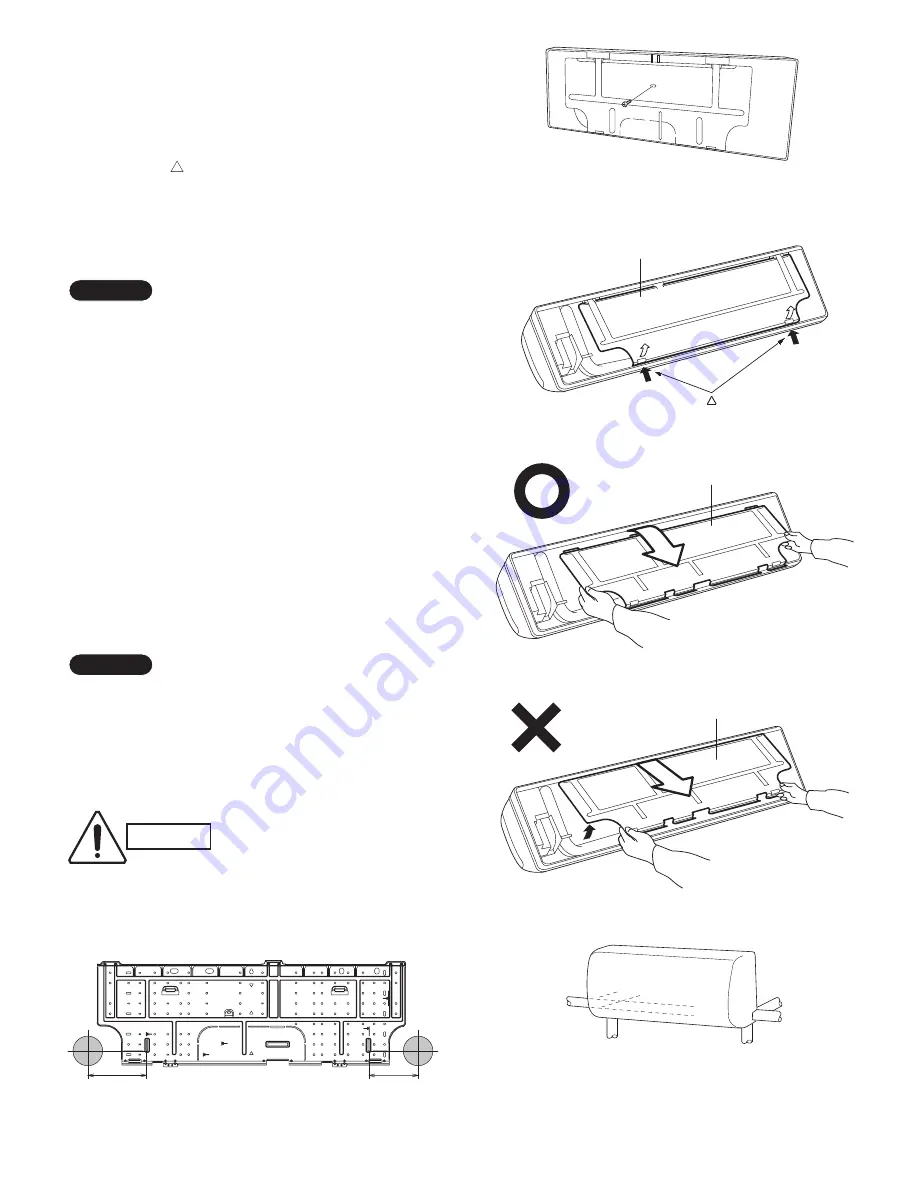
13
Rear panel
Fig. 7c
Rear panel
Fig. 7b
Set screw only for transportation
Fig. 6
Rear panel
marks
Fig. 7a
,-:
:;)04.
"0./:
:;)04.
"0./:8,(8
:;)04.
8,*533,4+,+
"0./:+5=4=(8+
:;)04.
,-:8,(8
:;)04.
,-:+5=4=(8+
:;)04.
Fig. 8
3. How to Install the Indoor Unit
3-1. Remove the Rear Panel from the Unit
(1) Remove and discard the set screw on the rear panel.
(Fig. 6)
(2) Press the 2
marks on the frame cover and disengage
the stationary tabs from the frame. (Fig. 7a)
(3) Remove the rear panel by grasping the sections shown
in Fig. 7b and pulling it in the direction shown by the
arrow.
Tubing can be extended in 6 directions as shown in Fig. 8.
Select the direction you need providing the shortest run to
the outside unit.
When left tubing is to be done, switch the drain hose and
drain cap. (For details, refer to “Switching drain hose and
drain cap” on page 21.)
3-2. Make a Hole
(1) Place the rear panel from the indoor unit on the wall at
the location selected. Make sure the panel is horizontal,
using a carpenter’s level or tape measure to measure
down from the ceiling. Wait until after cutting the hole
before attaching the rear panel to the wall.
(2) Determine which side of the unit you should make the
hole for tubing and wiring. (Fig. 9)
In the case of left-rear tubing, use the measurement points
6-7/32" (158 mm) from the marked position on the rear
panel for precise placement of the hose outlet. (Fig. 9)
(3) Before making the hole, check carefully that no studs or
pipes are directly run behind the spot to be cut.
The above precautions are also applicable if tubing
goes through the wall in any other location.
NOTE
NOTE
33
33
Fig. 9
CAUTION
Also avoid areas where elec-
trical wiring or conduits are
located.
Summary of Contents for CS-KE30NKU
Page 79: ......
Page 112: ...DC1111 0 ...