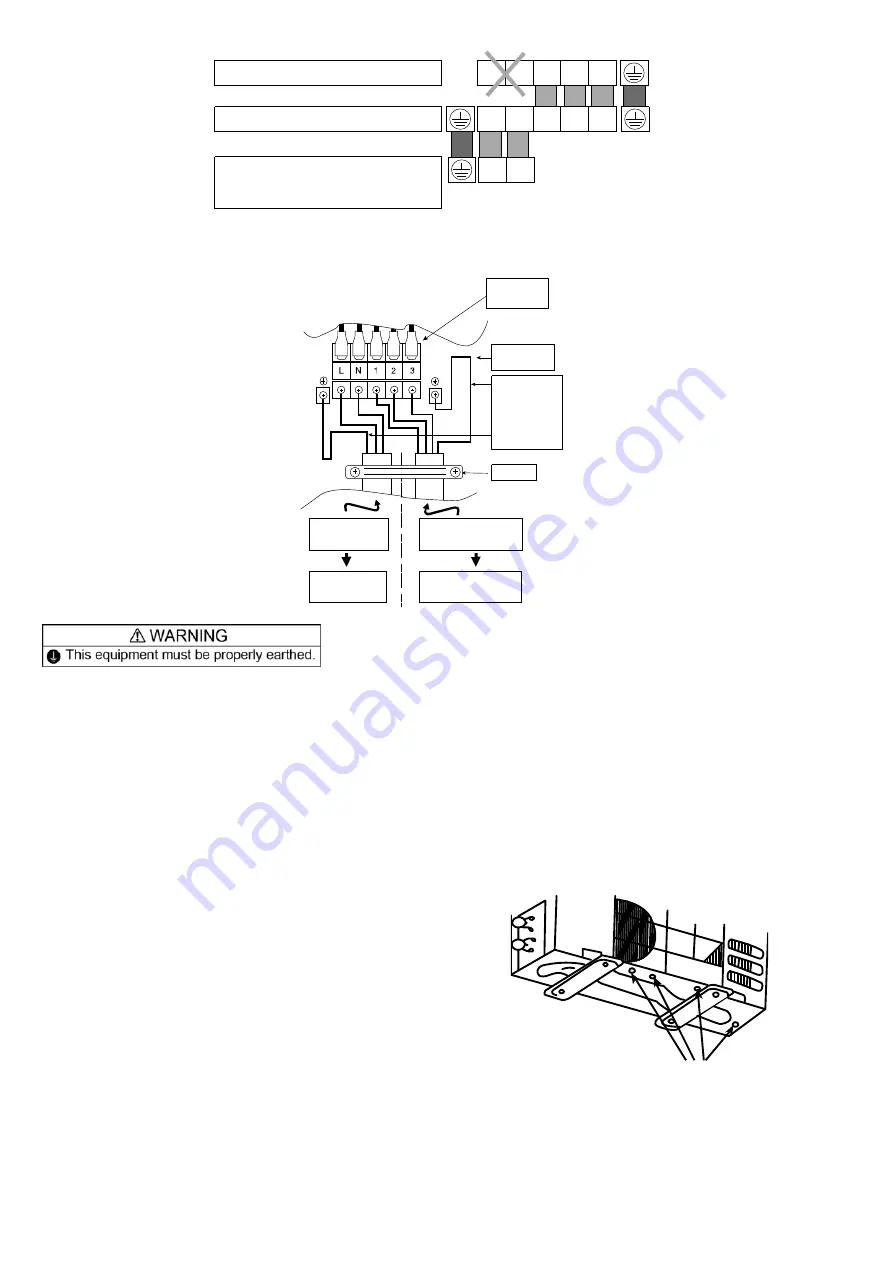
40
Terminals on the indoor unit
Colour of wires (connection cable)
Terminals on the outdoor unit
Terminals on the isolating devices
(Disconnecting means)
(Power supply cord)
L
N 1
2
3
(L) (N)
1
2
3
L
N
4. Secure the power supply cord and connection cable onto the control board with the holder.
5. Attach the control board cover back to the original position with screw.
Terminal
Board
Control
Board
Earth wire
longer than
others
AC wires
for safety
reason
Holder
Indoor & outdoor
connection cable
Isolating
Devices
Indoor unit
Power supply
cord
For wire stripping and connection requirement, refer to instruction
of indoor unit.
Isolating Devices (Disconnecting means) should have minimum 3.0 mm contact gap.
Earth wire shall be Yellow/Green (Y/G) in colour and longer than other AC wires for safety reason.
12.3.5 Piping Insulation
1 Please carry out insulation at pipe connection portion as mentioned in Indoor/Outdoor Unit Installation
Diagram. Please wrap the insulated piping end to prevent water from going inside the piping.
2 If drain hose or connecting piping is in the room (where dew may form), please increase the insulation by
using POLY-E FOAM with thickness 6 mm or above.
12.3.5.1
Outdoor Unit Drain Water
Water will drip from the base pan hole area
during defrost function.
To avoid water dripping, do not stand or place
objects at this area.
Hole
Summary of Contents for CS-HZ9RKE-1
Page 118: ...118 Figure 8 Figure 9 ...
Page 119: ...119 Figure 10 ...