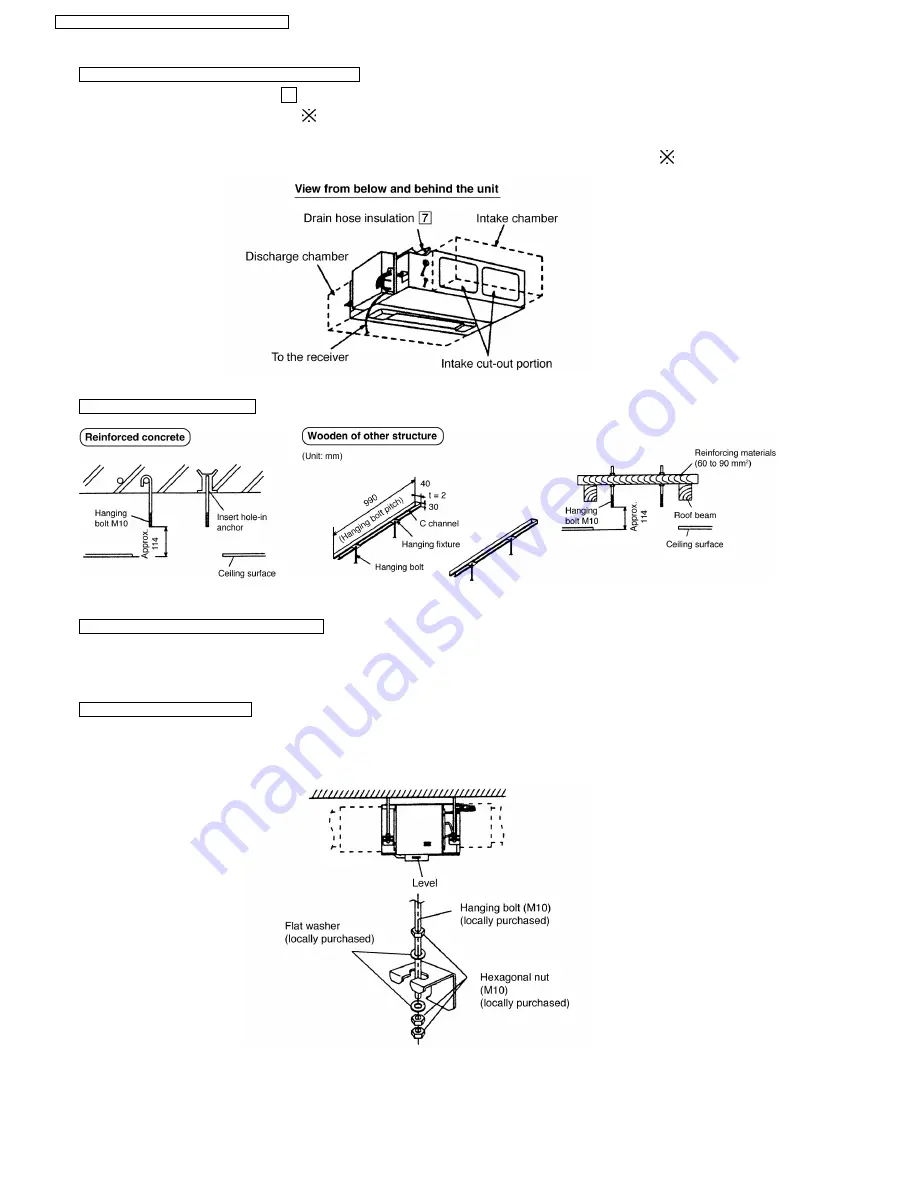
PREPARING TO INSTALL THE INDOOR UNIT
•
Fit the drain hose insulation 7
around the drain hose as shown in the diagram beside.
•
Attach the discharge chamber. (
) (10 screws)
•
Cut out the intake cut-out portions at the unit rear panel using a cutter or other tools to make openings.
•
Remove the two screws at the rear edge of the unit top panel and attach the intake chamber. (
) (8 screws)
Securing the Hanging Bolts
Switching the High State Switch (SW2)
•
To increase the air volume, open the control box and on the control board, switch the high state switch (SW2) to “HI”.
•
See the diagram for “Connecting the Indoor/Outdoor Connecting Cable”.
Installation into the Ceiling
•
Attach the nuts and washers to the hanging bolts, then lift up and hook the main unit onto the hanging fixtures.
•
Check if the unit is leveled using a level or a vinyl hose filled partially with water.
56
CS-E15DD3EW CU-E15DBE / CS-E18DD3EW CU-E18DBE
Summary of Contents for CS-E15DD3EW
Page 11: ...4 1 2 CS E18DD3EW 11 CS E15DD3EW CU E15DBE CS E18DD3EW CU E18DBE ...
Page 12: ...4 2 Outdoor Unit 4 2 1 CU E15DBE CU E18DBE 12 CS E15DD3EW CU E15DBE CS E18DD3EW CU E18DBE ...
Page 13: ...5 Refrigeration Cycle Diagram 13 CS E15DD3EW CU E15DBE CS E18DD3EW CU E18DBE ...
Page 14: ...6 Block Diagram 14 CS E15DD3EW CU E15DBE CS E18DD3EW CU E18DBE ...
Page 15: ...7 Wiring Diagram 15 CS E15DD3EW CU E15DBE CS E18DD3EW CU E18DBE ...
Page 20: ...2 Heating ii Auto Fan Speed 1 Cooling 20 CS E15DD3EW CU E15DBE CS E18DD3EW CU E18DBE ...
Page 32: ...9 Operating Instructions 32 CS E15DD3EW CU E15DBE CS E18DD3EW CU E18DBE ...
Page 33: ...33 CS E15DD3EW CU E15DBE CS E18DD3EW CU E18DBE ...
Page 34: ...34 CS E15DD3EW CU E15DBE CS E18DD3EW CU E18DBE ...
Page 35: ...35 CS E15DD3EW CU E15DBE CS E18DD3EW CU E18DBE ...
Page 36: ...36 CS E15DD3EW CU E15DBE CS E18DD3EW CU E18DBE ...
Page 37: ...37 CS E15DD3EW CU E15DBE CS E18DD3EW CU E18DBE ...
Page 38: ...38 CS E15DD3EW CU E15DBE CS E18DD3EW CU E18DBE ...
Page 39: ...39 CS E15DD3EW CU E15DBE CS E18DD3EW CU E18DBE ...
Page 73: ...13 1 2 CS E18DD3EW CU E18DBE 73 CS E15DD3EW CU E15DBE CS E18DD3EW CU E18DBE ...
Page 85: ...18 3 Remote Control 85 CS E15DD3EW CU E15DBE CS E18DD3EW CU E18DBE ...
Page 88: ......