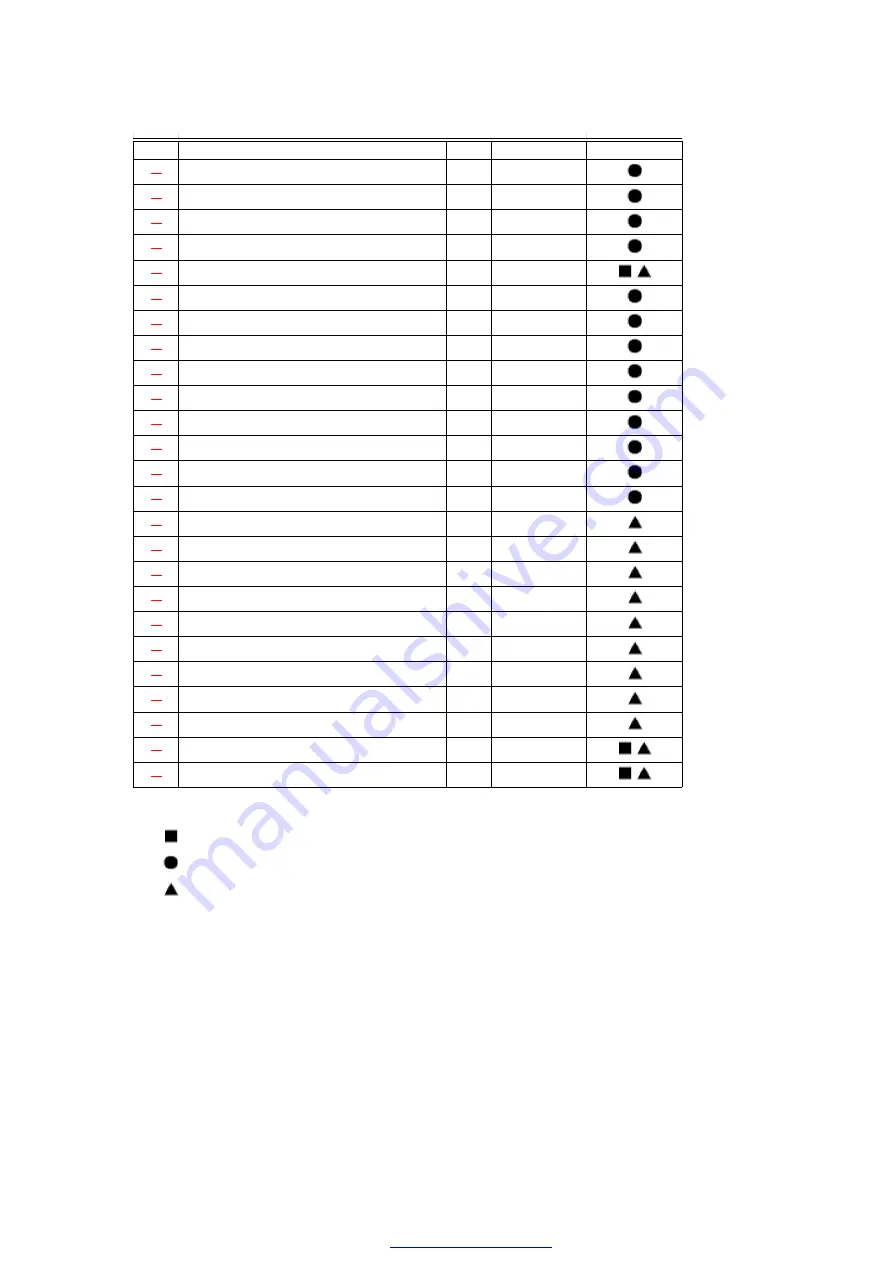
NO
DESCRIPTION & NAME
QTY
CS-280KR
REMARKS
40
CAP (FRONT GRILLE COMPLETE)
4
CWH5060060
41
PARTICULAR PLATE
1
CWH4945610
42
RAIN COVER (HOLDER - EVAPORATOR TUBE ASS’Y
1
CWH4631410
43
BAG COMPLETE (AIR PURIFYING FILTER)
1
CWE4649570C
44
REMOTE CONTROL COMPLETE ASS’Y
1
CWA75C556
45
INSTALLATION PLATE
1
CWH8010540
46
OPERATING INSTRUCTIONS
1
CWF8036900
47
INSTALLATION INSTRUCTIONS
1
CWF8039140
48
BAG COMPLETE - INSTALLATION SCREW
1
CWH4649210
49
SCREW
1
XTT4+12C
50
SCREW
1
XTT4+16C
51
SCREW
1
XTN4+8C
52
SCREW
1
XTT4+10C
53
SCREW
1
XTT4+8C
54
REMOTE CONTROL UPPER CASE
1
CWE15C241
55
CONTROL PANEL
1
CWE311064
56
KNOB
1
CWE17196A
57
KNOB
1
CWE17197A
58
CONTACTOR
1
CWA65036C
59
ELECTRONIC CONTROLLER
1
CWA74224
60
INDICATOR
1
CWE39199
61
REMOTE CONTROL LOWER CASE
1
CWE15128A
62
COVER
1
CWB80040A
63
CAP (BUTTON)
1
CWE5060120
64
FUSE COMPLETE
1
CWA4023070C
(Note)
- “ ” marked parts are recommended to be kept in stock.
- “ ” marked parts are supplied from TAMACO, Taiwan.
- “ ” marked parts are supplied from MACC, Malaysia.
17. Exploded View
70
PDF created with pdfFactory Pro trial version
Summary of Contents for CS-A281KR
Page 6: ...6 PDF created with pdfFactory Pro trial version www pdffactory com ...
Page 8: ...7 Wiring Diagram 8 PDF created with pdfFactory Pro trial version www pdffactory com ...
Page 34: ...34 PDF created with pdfFactory Pro trial version www pdffactory com ...
Page 66: ...66 PDF created with pdfFactory Pro trial version www pdffactory com ...
Page 67: ...15 Exploded View 67 PDF created with pdfFactory Pro trial version www pdffactory com ...