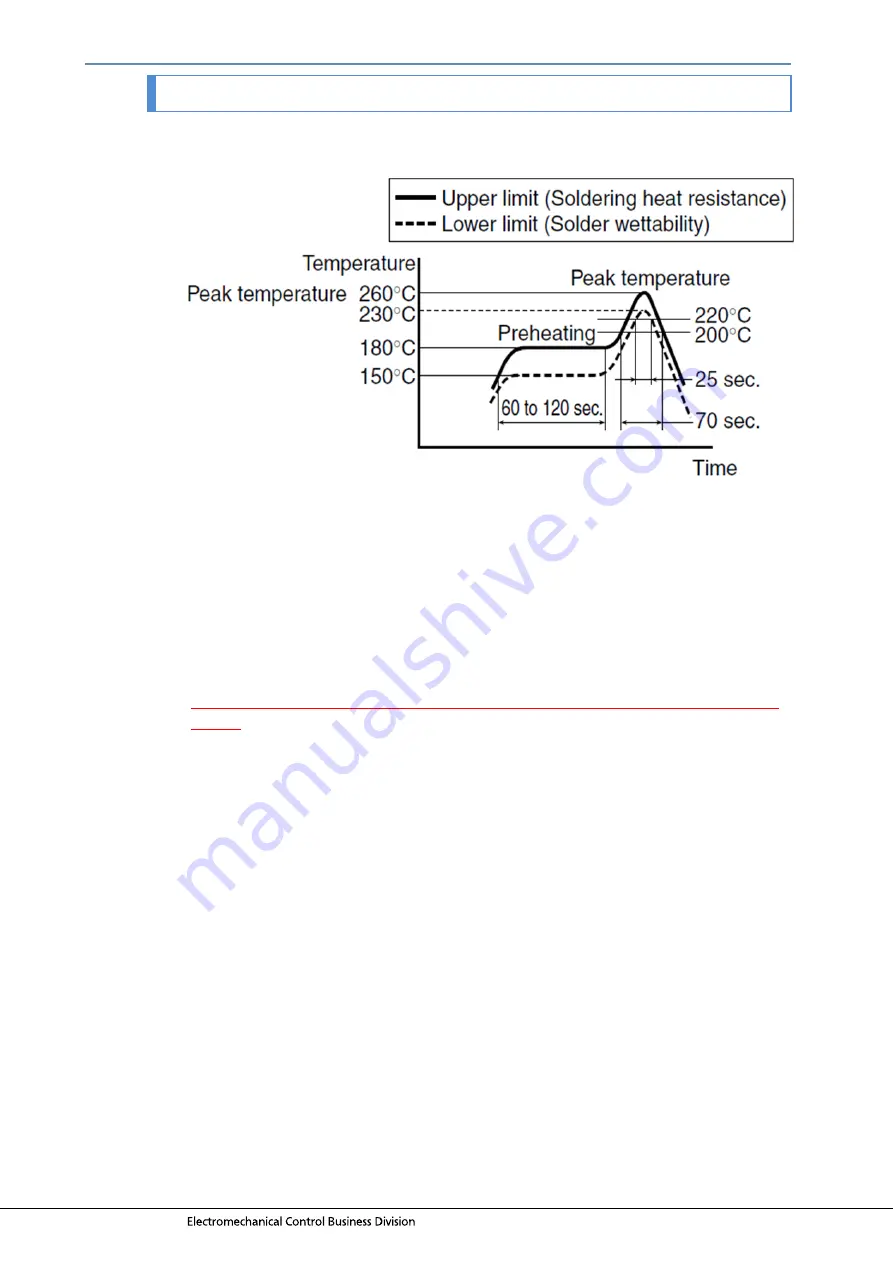
Operation manual for Narrow-pitch connectors A4S
Panasonic Corporation
industrial.panasonic.com/ac/e/
©
Panasonic Corporation 2015
ACCTF6E-2 201506
- 16 -
03-2. Precautions for reflow soldering
(1)Measure the temperature profile at the mounted connector position, and make sure
that it conforms to the recommended profile.
(2)When the molded part of connector melts or becomes deformed during the reflow
process, the heating temperature may be too high, or the connector may be
affected by a nearby electronic component with high heat capacity.
(3)When the soldering finish is abnormal, check the next points.
If solder creeps to or near the contact section, then excessive solder may have
been applied or the wicking phenomenon may have occurred. Check the amount
of solder applied, the position, and the temperature profile at the mounted
connector position.
In particular, be careful not to apply excessive solder when the N2 reflow furnace
is used
.
(4)Extending the screen pattern outward and providing a solder application position
on the outer side can help secure a large front fillet.
(5)In the reflow process of FPC boards, pay attention to the following points to
reduce temperature variations among connector terminals.
- Ensure that the FPC board and the base attach firmly to each other when the base
on which the FPC board is placed is made of metal (e.g., Al).
- When a metal reinforcing plate is used, further firmly attach the base and
reinforcing plate (e.g., by using heat-resistant double-sided tape).
Summary of Contents for A4S
Page 28: ...ACCTF6E 2 201506 ...