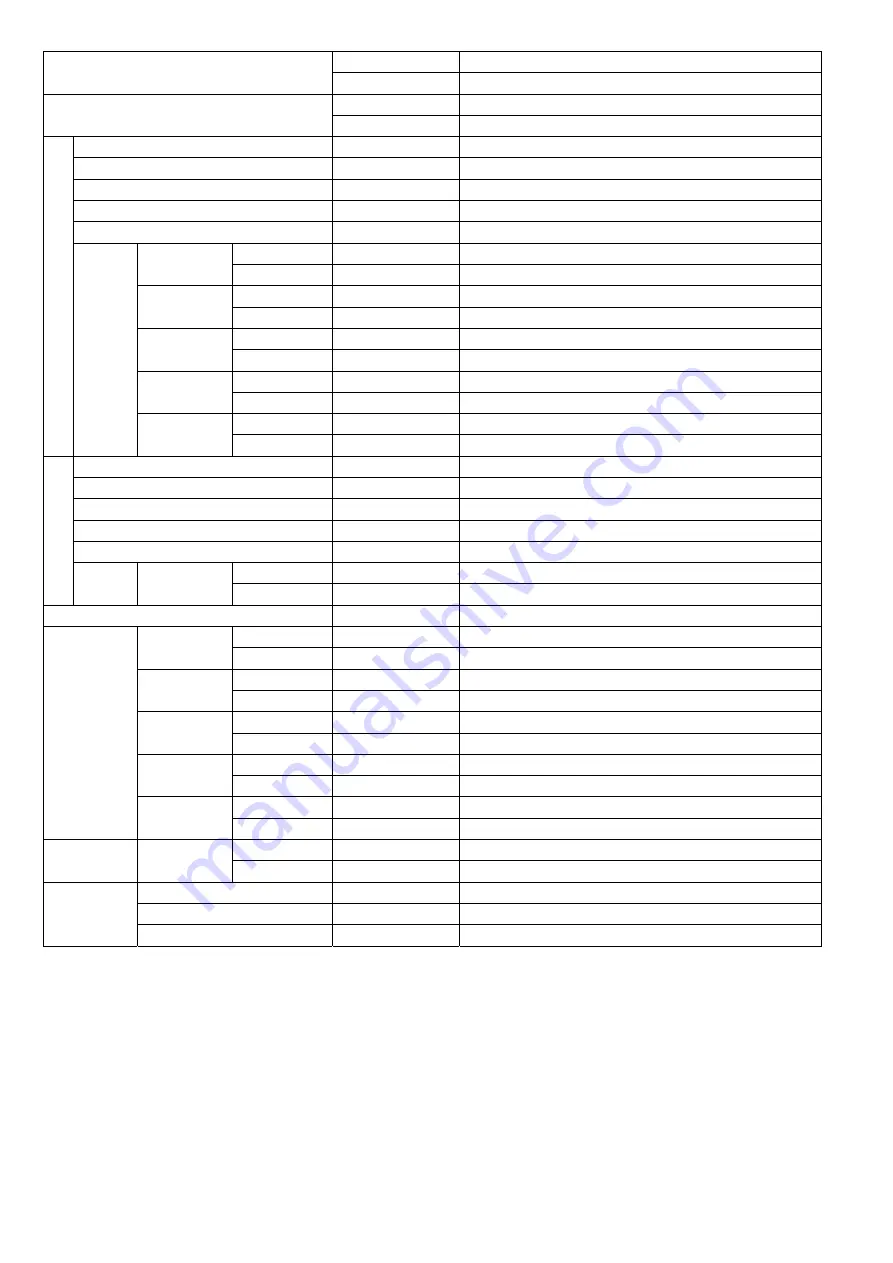
26
Indoor
Model
CS-RZ80TKR
POS (EAN)
5025232871391
Outdoor
Model
CU-RZ80TKR
POS (EAN)
5025232871582
Indoor Fan
Type
Cross-flow Fan
Material
ASG33
Motor Type
DC (8-poles)
Input Power
W
105.0
Output Power
W
40
Speed
QLo
Cool
rpm
870
Heat
rpm
950
Lo
Cool
rpm
970
Heat
rpm
1050
Me
Cool
rpm
1160
Heat
rpm
1220
Hi
Cool
rpm
1350
Heat
rpm
1400
SHi
Cool
rpm
1450
Heat
rpm
1450
Outdoo
r Fa
n
Type
Propeller Fan
Material
PP
Motor Type
DC (8-poles)
Input Power
W
-
Output Power
W
60
Speed
Hi
Cool
rpm
720
Heat
rpm
720
Moisture Removal
L/h (Pt/h)
4.7 (9.9)
Indoor Airflow
QLo
Cool
m³/min (ft³/min) (L/s)
13.91 (491) (232)
Heat
m³/min (ft³/min) (L/s)
15.41 (544) (257)
Lo
Cool
m³/min (ft³/min) (L/s)
15.83 (559) (264)
Heat
m³/min (ft³/min) (L/s)
17.32 (612) (287)
Me
Cool
m³/min (ft³/min) (L/s)
19.46 (687) (324)
Heat
m³/min (ft³/min) (L/s)
20.56 (726) (343)
Hi
Cool
m³/min (ft³/min) (L/s)
23.10 (815) (385)
Heat
m³/min (ft³/min) (L/s)
24.0 (845) (400)
SHi
Cool
m³/min (ft³/min) (L/s)
25.01 (883) (416)
Heat
m³/min (ft³/min) (L/s)
24.95 (881) (415)
Outdoor Airflow
Hi
Cool
m³/min (ft³/min)
55.8 (1970)
Heat
m³/min (ft³/min)
55.8 (1970)
Refrigerant
Cycle
Control Device
Expansion Valve
Refrigerant Oil
cm³
FW50S (800)
Refrigerant Type
g (oz)
R32, 1.49k (52.6)