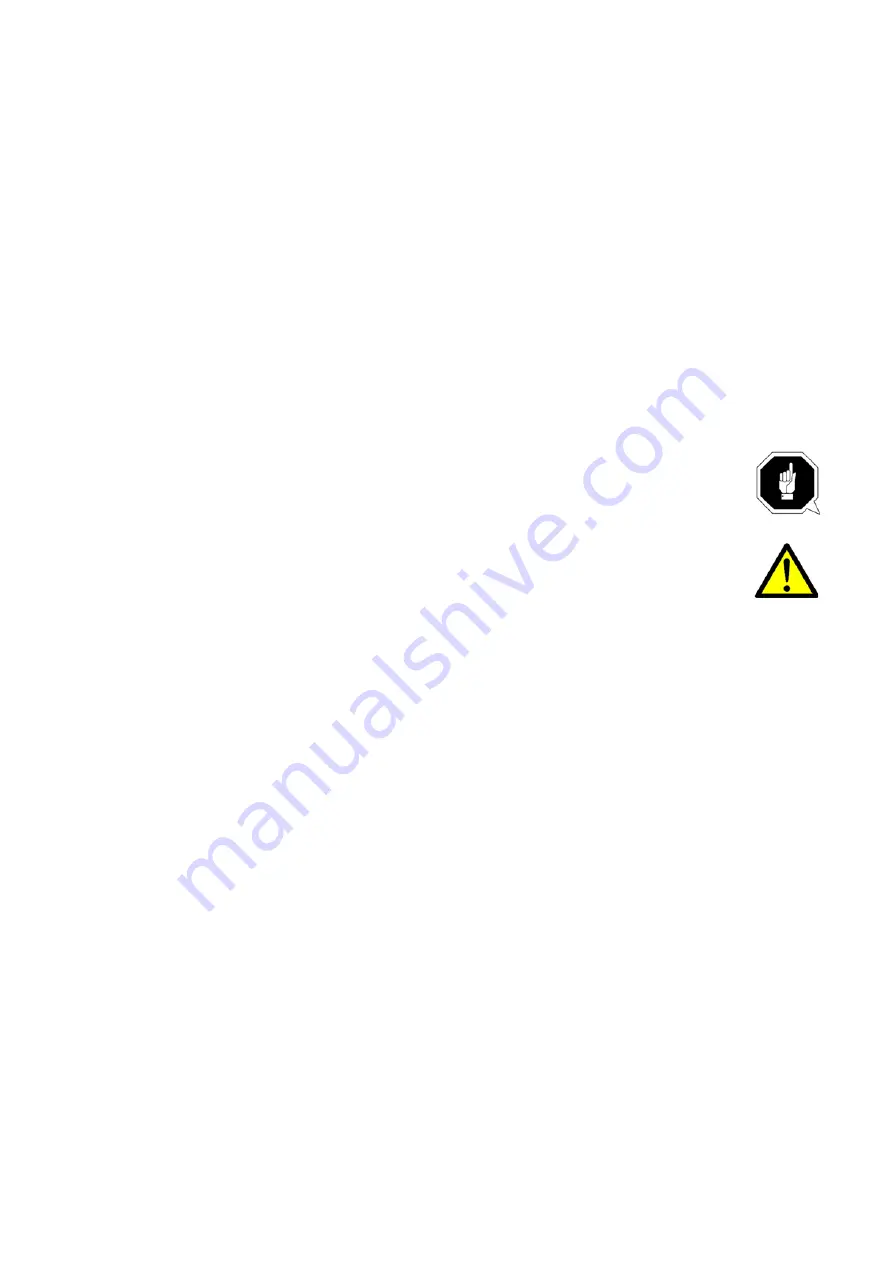
1.4
Reasonably foreseeable misuse
Any use other than that specified under "Intended use" or any use beyond that described will be
deemed non-intended use and is not permissible.
Any other use has to be discussed with the manufacturer.
It is only allowed to process metal, cold and non-inflammable materials with the drilling
machine.
In order to avoid misuse, it is necessary to read and understand the operating instructions
before first commissioning.
Operators must be qualified.
1.4.1
Avoiding misuse
Use of suitable cutting tools.
Adapting the speed setting and feed to the material and workpiece.
Clamp workpieces firmly and free of vibration.
ATTENTION!
The workpiece is always to be fixed by a machine vice, jaw chuck or by another
appropriate clamping tool such as for the clamping claws.
WARNING!
Risk of injury caused by flying workpieces.
Clamp the workpiece in the machine vice. Make sure that the workpiece is firmly clamped in the
machine vice and that the machine vice is firmly clamped onto the machine table.
Use cooling and lubricating agents to increase the durability of the tool and to improve the
surface quality.
Clamp the cutting tools and workpieces on clean clamping surfaces.
Sufficiently lubricate the machine.
Set the bearing clearance and guides correctly.
Recommendations:
Insert the drill in a way that it is exactly positioned between the three clamping jaws of the
quick action chuck.
When drilling, make sure that
the suitable speed is set depending on the diameter of the drill,
the pressure must only be such that the drill can cut without load,
if there is too much pressure, the drill will wear quickly and may even break or jam in the
borehole. If the drill jams, immediately stop the main motor by pressing the emergency stop
switch,
use commercial cooling/lubricating agents for hard materials, e.g. steel and
generally always back the spindle out of the workpiece while it is still turning.
1.5
Possible dangers caused by the drilling machine
The drilling machine was built using state-of-the-art technology.
Nevertheless, there is a residual risk as the drilling machine operates with
at high speeds,
with rotating parts,
electrical voltage and currents.
We have used design and safety engineering to minimize the health risk to personnel resulting
from these hazards.
7