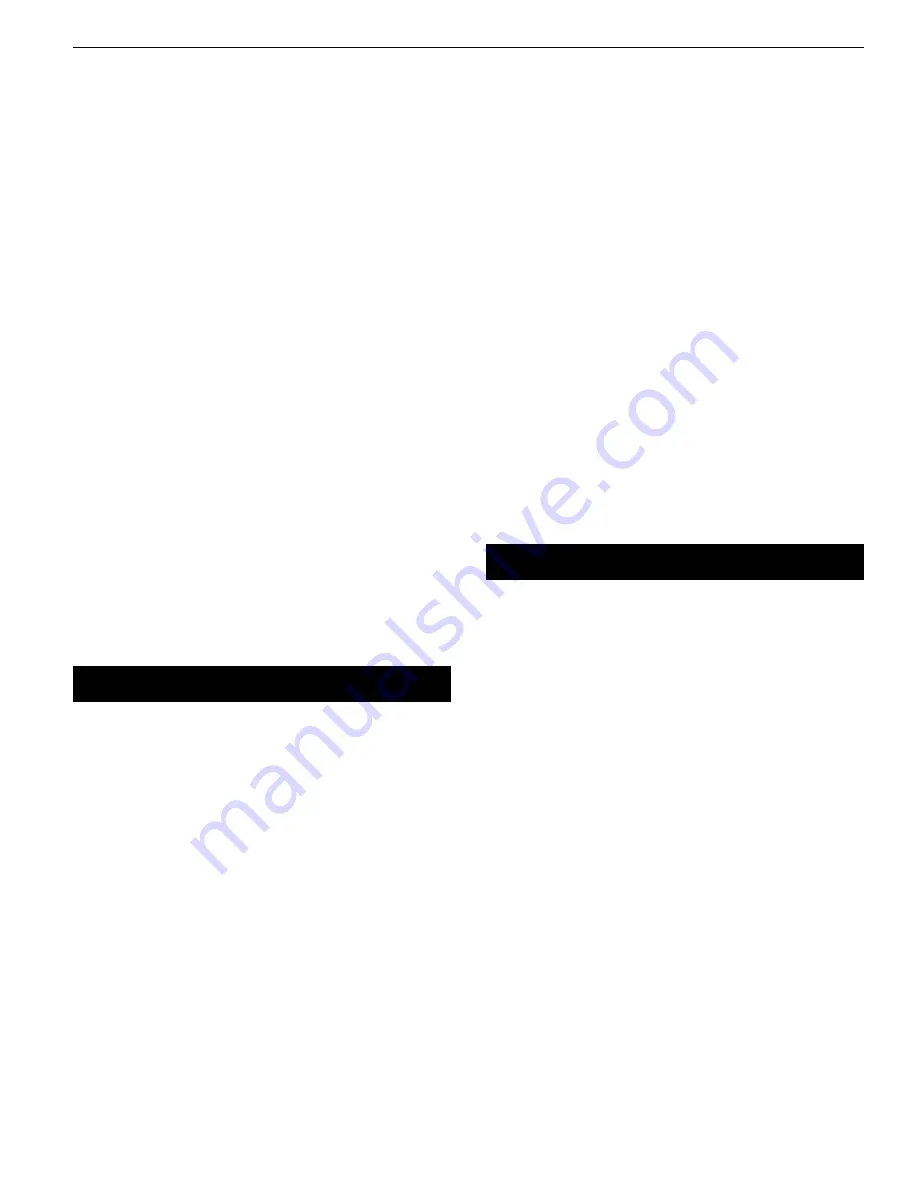
3
SAFETY RULES (CONTINUED)
KNOW HOW TO USE TOOL
•
Use the right tool for the job. Do not force tool or attachment
to do a job for which it was not designed.
•
Disconnect tool when changing accessories such as bits, cut-
ters and the like.
•
Avoid accidental start-up. Make sure switch is in OFF position
before plugging in.
•
Do not force tool. It will work most efficiently at the rate for
which it was designed.
•
Handle workpiece correctly. Secure work with clamps or vise.
Leave hands free to operate machine, Protect hands from
possible injury.
•
Never leave a tool running unattended. Turn the power off and
do not leave tool until it comes to a complete stop.
•
Do not overreach. Keep proper footing and balance.
•
Never stand on tool. Serious injury could occur if tool is tipped
or if cutter is unintentionally contacted.
•
Keep hands away from moving parts and cutting surfaces.
•
Know your tool. Learn its operation, application and specific
limitations.
•
Feed work into a bit or cutter against the direction of rotation
of bit or cutter.
•
Turn the machine off if it jams. A cutter jams when it digs too
deeply into the workpiece. (The motor force keeps it stuck in
workpiece.)
•
Use recommended accessories. Refer to page 9. Use of improp-
er accessories may cause risk of injury to persons.
•
Clamp workpiece or brace against column to prevent rotation.
•
Use recommended speed for drill accessory and workpiece
material.
WARNING:
Think Safety! Safety is a combination of operator com-
mon sense and alertness at all times when drill press is being used.
A
AS
SS
SE
EM
MB
BL
LY
Y
MOUNT COLUMN ASSEMBLY TO BASE
Refer to Figure 5.
•
Place base (Ref. No. 1) on flat level surface.
•
Mount column assembly (Ref. No. 2) to base using four socket
head bolts (Ref. No. 3).
MOUNT TABLE
Refer to Figure 5.
•
Attach crank handle (Ref. No. 7) to shaft of worm gear (Ref. No.
11), rotate worm gear to remove slack, and shoulder crank han-
dle with set screw (Ref. No. 6).
•
Attach table (Ref. No. 16) to table bracket (Ref. No. 12) using hex
head bolt and lock washer (Ref. Nos. 23 and 24).
•
Thread hose fitting (Ref. No. 17) into table. Slide hose (Ref. No.
18) over hose fitting.
MOUNT HEAD ASSEMBLY
Refer to Figure 6.
WARNING:
Although compact, the drill press head assembly is
heavy. Two people are required to mount the drill press head
assembly onto the column.
•
Slide drill press head assembly onto top of column.
•
Position head so that it is centered over base.
•
Secure head by inserting threaded bushing (Ref. No. 64) into
left side of head, bushing (Ref. No. 66) into right side of head,
then insert and tighten socket head bolt (Ref. No. 67).
MOUNT MOTOR ADJUSTING HANDLE
Refer to Figure 6.
•
Thread handle (Ref. No. 76) into motor mount plate (Ref. No. 77).
MOUNT QUILL FEED HANDLE ASSEMBLY
Refer to Figure 6.
•
Place key (Ref. No. 5) into keyway of pinion (Ref. No. 6).
•
Place quill feed handle assembly over pinion.
•
Secure handle assembly with socket head bolt (Ref. No. 3) and
spacer (Ref. No. 4).
MOUNT DRILL CHUCK AND ARBOR
Refer to Figure 6.
•
Be sure spindle taper, arbor taper and chuck taper are clean
and dry.
•
Insert arbor into spindle, push arbor into spindle and twist
arbor slightly to release air trapped in taper. Make sure tang of
arbor seats properly into spindle.
•
Mount chuck onto arbor, push chuck over arbor and twist
chuck slightly to release air trapped in taper.
•
Place a block of wood on table, below chuck, and firmly pull
quill feed handle to securely seat chuck and arbor into spindle.
IIN
NS
ST
TA
AL
LL
LA
AT
TIIO
ON
N
Refer to Figures 1, 2 and 3.
MOUNT DRILL PRESS
•
Drill press must be mounted to flat level surface. Use shims or
machine mounts if necessary. Do not mount drill press in direct
sunlight.
•
Be sure to bolt drill press to floor or bench securely to prevent
tipping and minimize vibration.
•
Tighten all nuts and bolts that may have loosened during
shipment.
POWER SOURCE
The motor is designed for operation on the voltage an frequency
specified. Normal loads will be handled safely on voltages not
more than 10% above or below the specified voltage.
Running the unit on voltages which are not within the range may
cause overheating and motor burn out. Heavy loads require that
the voltage at motor terminals be no less than the voltage speci-
fied.
GROUNDING INSTRUCTIONS
WARNING:
Improper connection of equipment grounding con-
ductor can result in the risk of electrical shock. Equipment should
be grounded while in use to protect operator from electrical shock.
Check with a qualified electrician if grounding instructions are not
understood or if in doubt as to whether the tool is properly
grounded.
This tool is equipped with an approved 3-conductor cord rated up
to 300V and a 3-prong grounding type plug rated at 115V (See
Figure 1) for your protection against shock hazards.
Palmgren Operating Manual & Parts List
80206