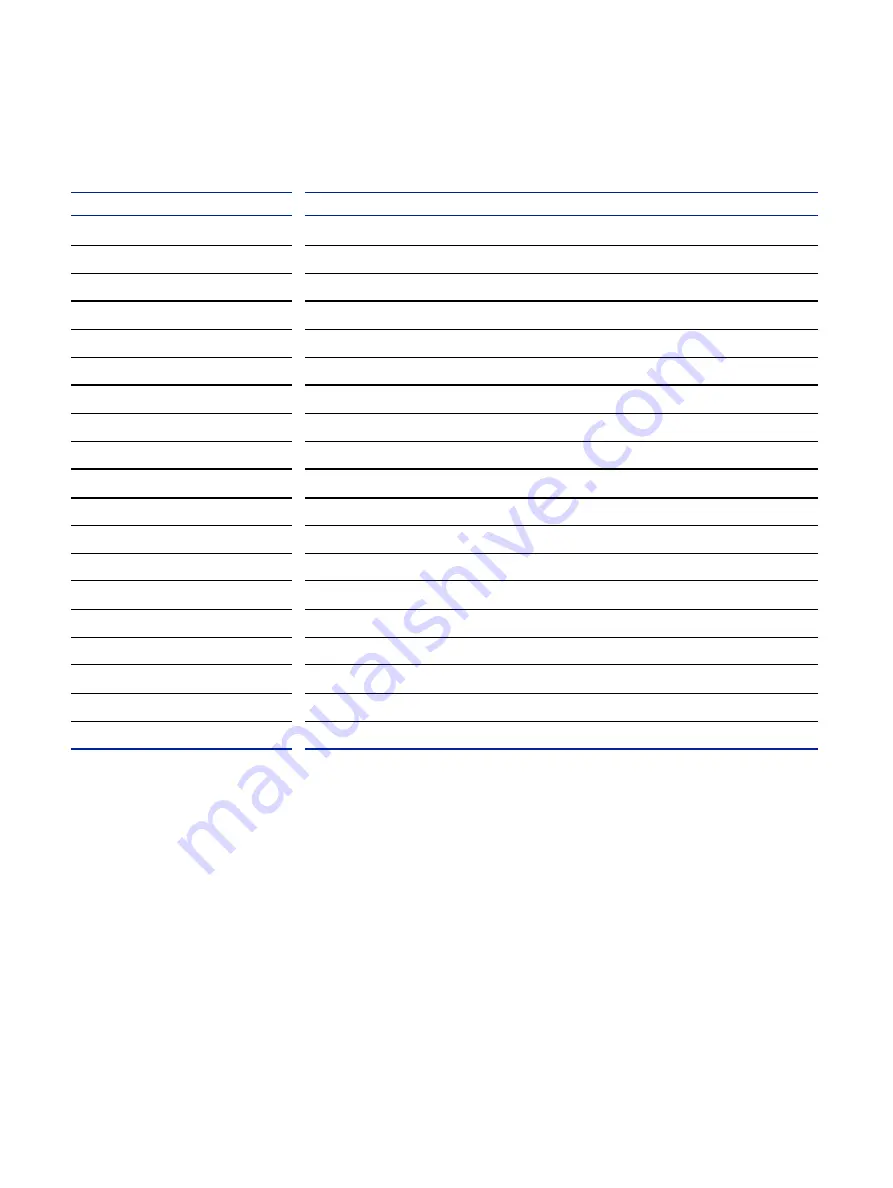
34
15
Spare Parts and Accessories
Table 12
Standard accessories.
Part Number
Description
4100048
Bushing, wand HDPE (Included in tool box)
201487
Quickclamp tube fitting wingnut clamp (included in tool box)
4100049
Coupler, wand, stainless steel (included in tool box)
4100153NS
Plate, clip for 1 in. drain valve (included in tool box)
201489
Knurled head thumb screw (included in tool box)
LT-SVSP366
Assembly, EU power cord (included in tool box)
LT-SVSP365
Assembly, US power cord (included in tool box)
1100025
Shaft adaptor assembly
500-11381-00
Medium acting fuse, 3 A, 5 mm X 20 mm
LT-SVSP367
Assembly, Australian power cord
LT-SVSP368
Assembly, Swiss power cord
LT-SVSP369
Assembly, UK power cord
LT-SVSP480
Assembly, Chinese power cord
LT-SVSP414
White illuminated push button switch, assembled
LT-SVSP415
White LED bulb
CBG401B
Basic Control box CE
–
optional for DCS/SCADA data transfer
CBG401A
Advanced Control box CE
–
optional for DCS/SCADA data transfer
CBG402B
Basic Control box UL
–
optional for DCS/SCADA data transfer
CBG402A
Advanced Control box UL
–
optional for DCS/SCADA data transfer