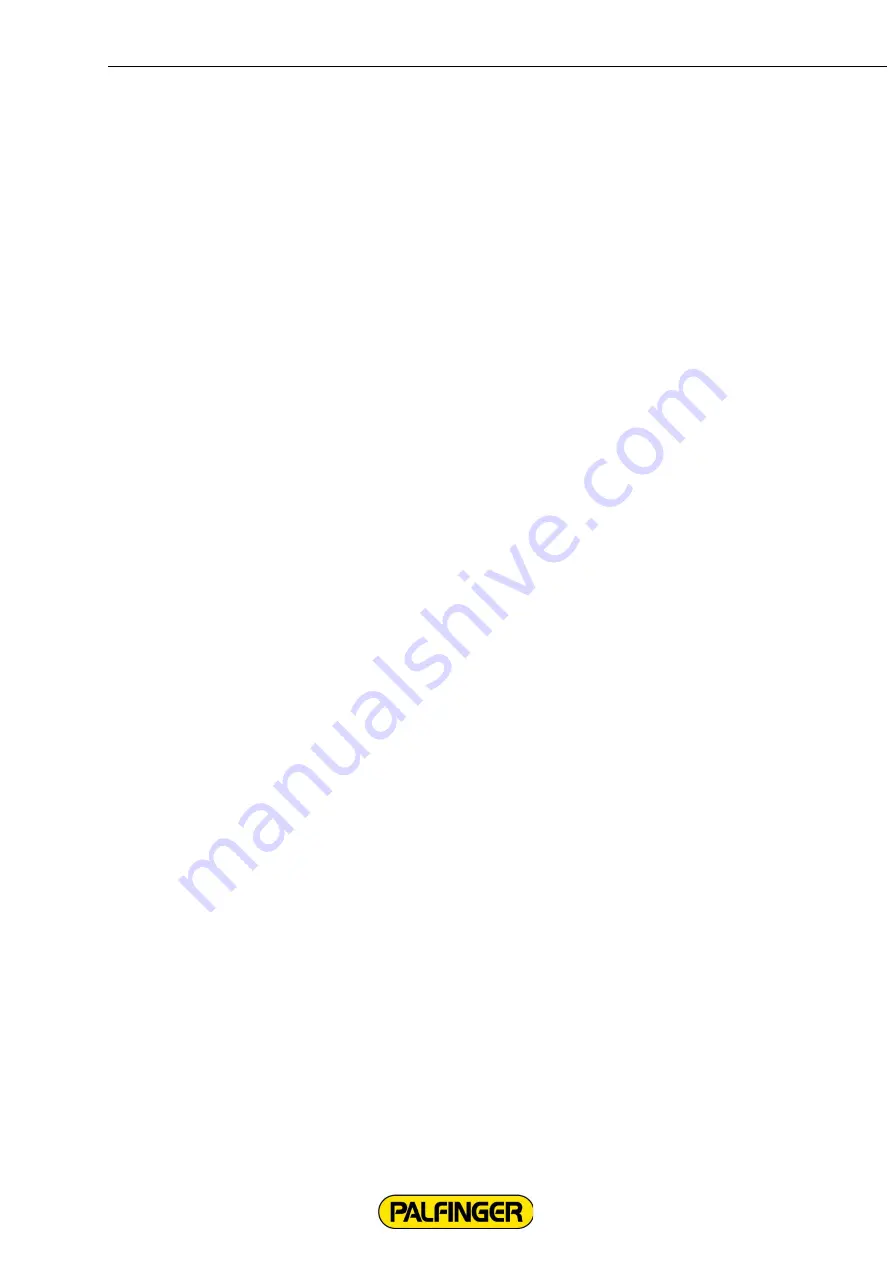
CHAPTER 5
17
CHAPTER 5
Set-Up
In this chapter
....................................
Crane Mounting
.......................................
20
Preparation for base assembly
.................
22
Process of tightening
................................
23
Preserving the screw joints
......................
24
Summary of Contents for PSM400-16
Page 15: ...CHAPTER 4 12 CHAPTER 4 Crane handling In this chapter Crane handling 13 Storage 16...
Page 37: ...CHAPTER 8 34 CHAPTER 8 Power Pack In this chapter Filling the power pack tank 34...
Page 44: ...CHAPTER 10 41 CHAPTER 10 Post assembly check In this chapter Post assembly check 42...
Page 47: ...CHAPTER 11 Commissioning In this chapter Commissioning 44 Term Definitions 44...
Page 49: ...CRANES LIFESAVING EQUIPMENT WINCHES AND HANDLING EQUIPMENT SERVICE 2021 11 15 Revision 3 0 NOV...