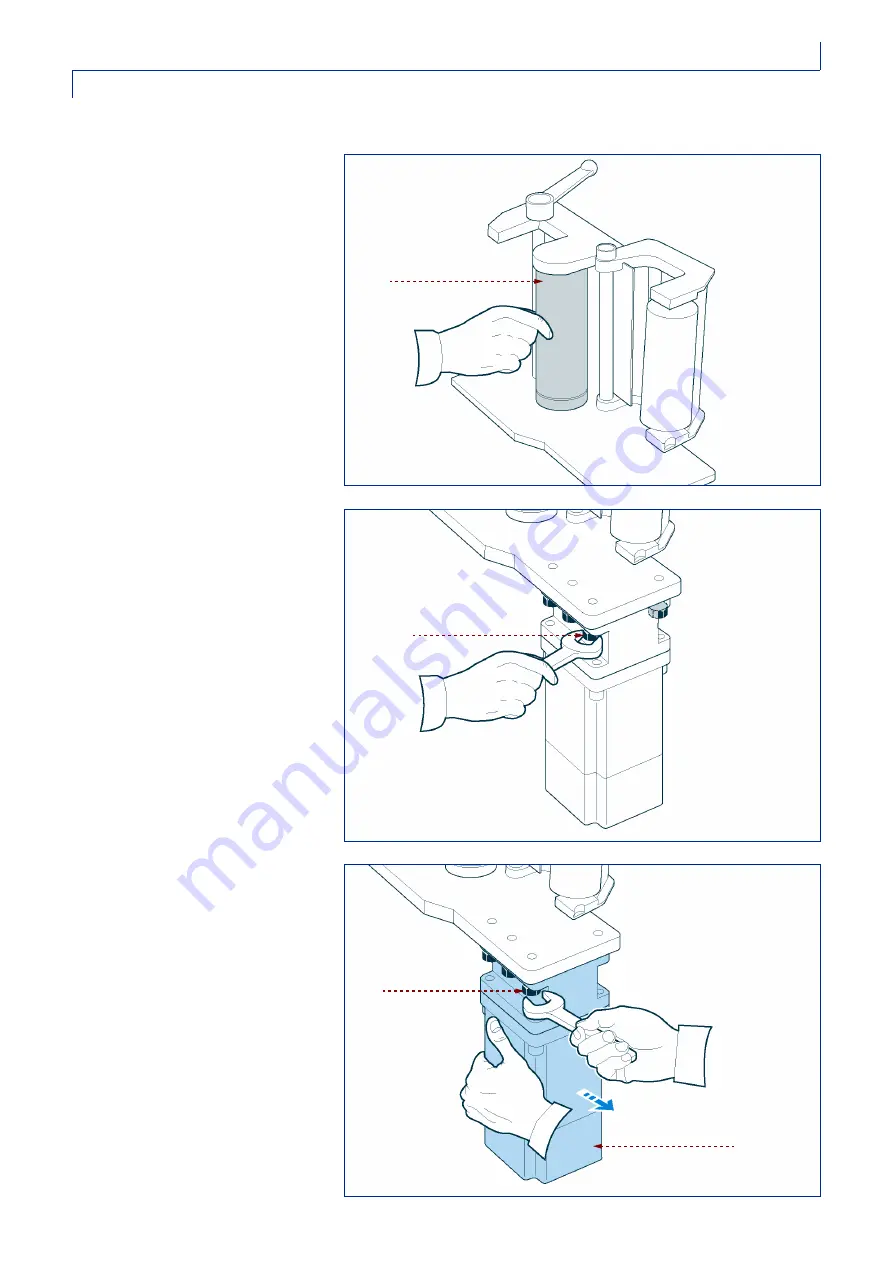
Section 5
LABELING UNIT
-
14
-
English
F
412
0501
00.fm
ID
M
version:
Module 40/60/90/120
DRIVING MOTOR BELT ADJUSTMENT
In some versions (e.g. MODULE 120),
there is a belt and pulley drive between
the motor and the driving roller. Refer
to the “Assembly drawings” document
for further details.
To pull the belt taut, proceed as follows.
1 -Open the guard over the driving
unit and make sure there is no
slack on the
roller
. A flexible
displacement of approximately 0.5
mm is normal. If the roller moves
more, proceed with the steps listed
below.
2 -Loosen the driving motor coupling
cage
bolts
.
3 -Move the
motor
with one hand,
shifting it outwards without exerting
an excessive force, then tighten the
bolts
.
An automatic sprung tensioning
system ensures the right tension on the
drive belt. Refer to the “Assembly
drawings” document.
IDM-41200601100.tif
roller
IDM-41200601200.tif
screw
IDM-41200601300.tif
motor
screw