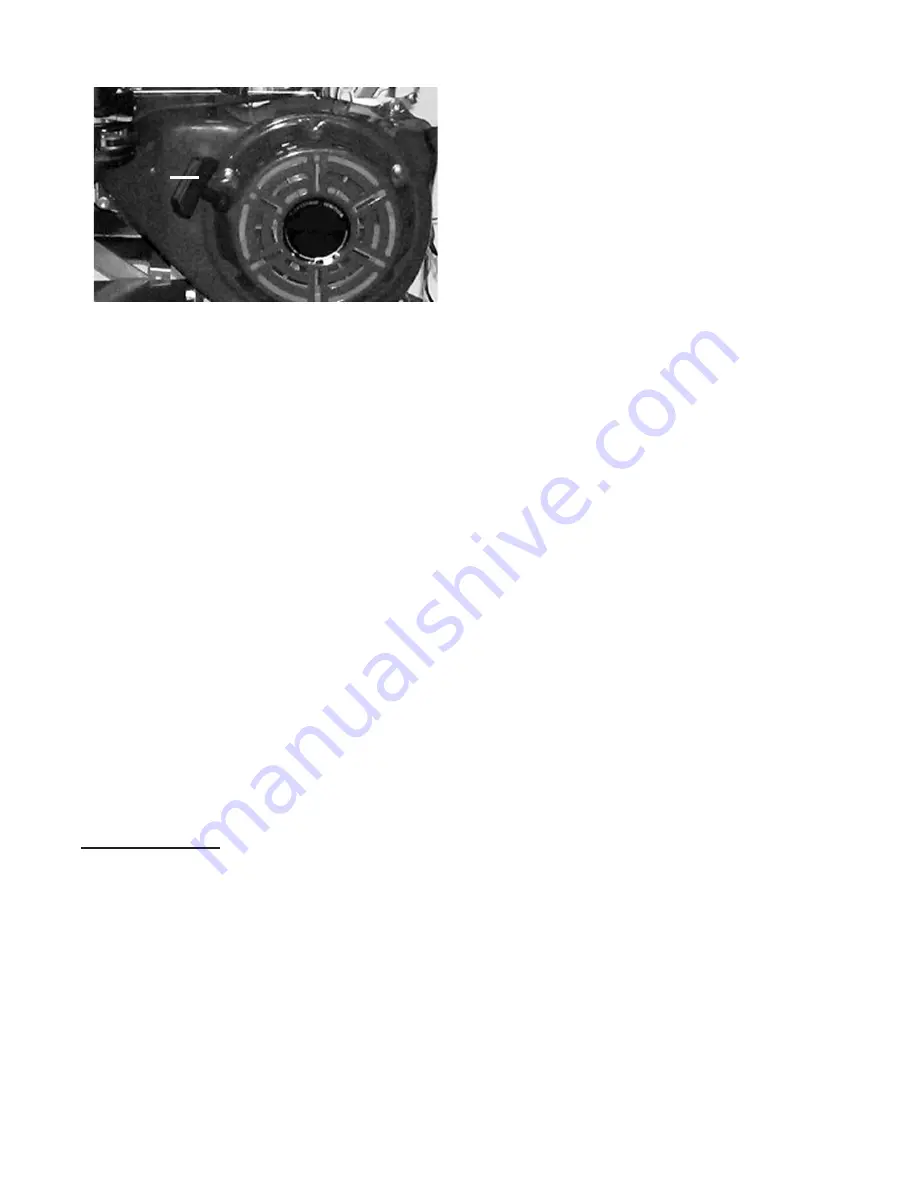
Page 11
For technical questions, please call 1-800-444-3353.
SKU 65351
FIGURE H
STARTER
HAndLE
(16K)
3. Grasp the Starter Handle (16K), and
pull slowly until resistance is felt. While
holding the Handle, allow the Starter
Rope to rewind slowly. Then, pull the
Starter Handle with a rapid, full arm
stroke. Once again while holding the
Handle, allow the Rope to rewind slowly.
Repeat as necessary, until the Engine
starts.
(See Figure H.)
After the Engine starts and warms up,
4.
slowly move the Choke Lever (22G) to
its “RUN” position.
(See Figure F.)
To adjust the Engine’s speed, move
5.
the Engine Throttle (23G) to the left for
increased speed. Move the Throttle to
the right for decreased speed.
(See Figure F.)
IMPORTANT: Allow the Engine to run
6.
at no load until warm (1-5 minutes) and
with no load after each start-up to allow
the Engine to stabilize.
Break-in Period:
Breaking-in the Engine will help to
a.
ensure proper equipment and operation,
and will extend the Engine’s lifespan.
The warranty is void if the Engine is not
broken in properly. The first 20 hours of
operation is the break-in period.
During the first 3 hours of use:
b.
Do not apply a heavy load to
•
equipment.
Do not operate the Engine at its
•
maximum speed.
After the first 20 hours of use:
c.
Change the engine oil.
•
Under normal operating conditions
subsequent maintenance follows the
schedule explained in MAINTENANCE
AND SERVICING section.
Once Engine starts, the Water Pump will
7.
run continuously until Engine is turned
off. To turn off the Engine, turn the
Power Switch (6K) off.
(See Figure G.)
IMPORTANT:
8.
If the machine’s Impeller
strikes a foreign object, or if the machine
begins making an unusual noise or
vibrates excessively, immediately shut
off the Engine. Allow the Impeller to
come to a complete stop. Remove the
Spark Plug (10D) from the Engine. Then
perform the following steps:
Clear the obstruction.
a.
Inspect for damage.
b.
Repair or replace damaged parts.
c.
Check for any loose parts and tighten to
d.
ensure continued safe operation.
Do not leave the Water Pump
9.
unattended when it is running. Turn off
the Engine before leaving the work area.
When finished, turn the Engine’s Power
10.
Switch (6K) off. Wait until the Water
Pump completely stops. Allow the
Engine to completely cool before moving
or storing the Water Pump.