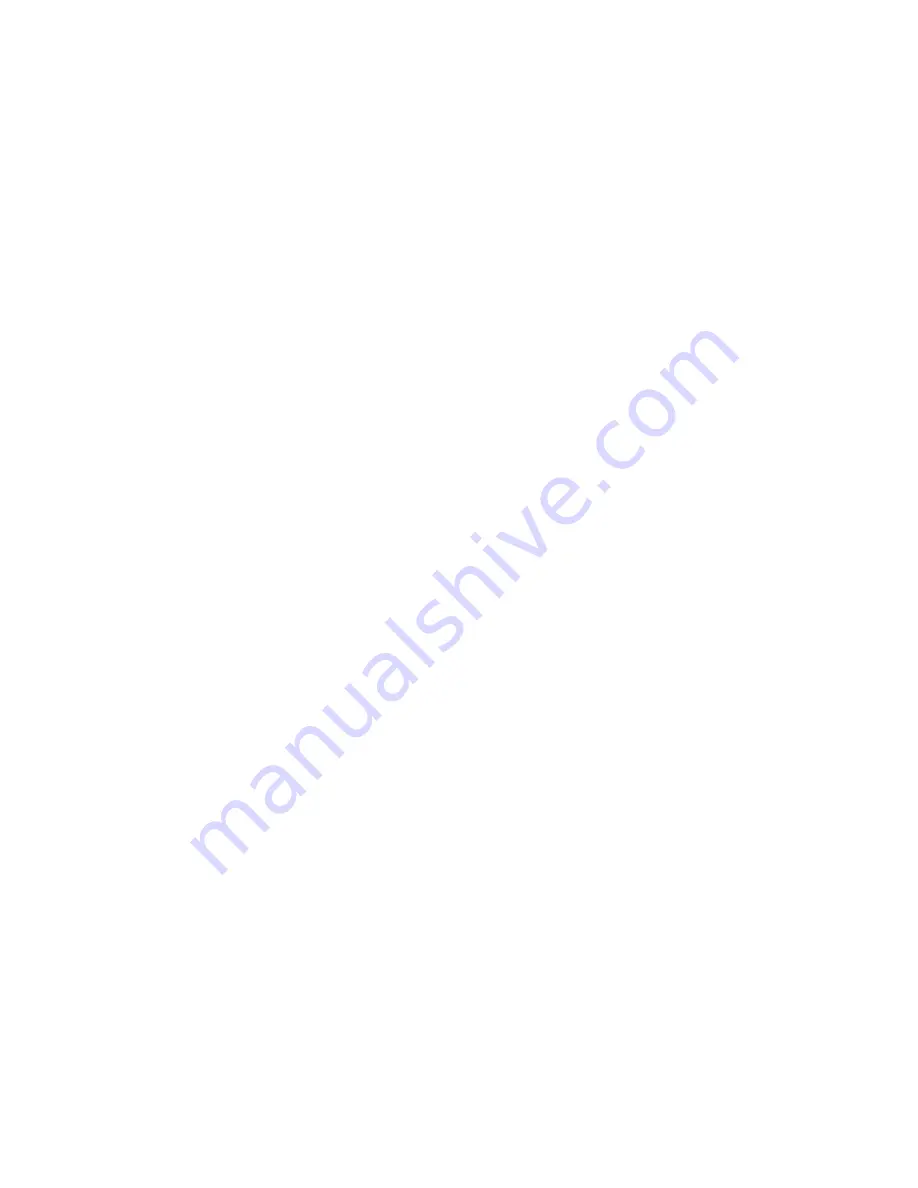
33
AIR MOTOR SERVICE
DISASSEMBLY PROCEDURE
A. Preparing for Motor disassembly
1. Remove the motor from the winch and move to a clean
working surface ready for stripping, externally clean
the motor before opening.
2. Drain the oil from the motor casing by removing the
drain plug (26).
3. Stripping and re-assembly will be simplifi ed if the crank-
shaft (20/A/B) is held vertically in a soft-jawed vice or
supported on a suitable support to raise the shaft clear
of the working surface.
B. Removal of Rotary Valve Housing assembly
1. Remove inlet control valve.
2. Remove valve cover (51)
3. Release bolts (38) and valve bush housing (3) can be
eased upward.
4. Carefully remove rotary valve (2) from the housing (3).
This can generally be done from the inside outwards.
Inspect both the rotary valve and the housing for wear.
The normal clearance at manufacture between these
two components is 0.002 - 0.003 in. (0.05 - 0.075 mm).
Excessive wear will cause air leakages and loss of ef-
fi ciency of the unit.
C. Disassembly of the motor
1. Remove the outer spacer washer 31/34 and remove
the pivot pins (29). This is usually done with a bent rod
withdrawing the pins from the inside outwards.
2. Remove all cylinder cap bolts (37). Remove the pis-
ton and rod assembly from the motor by pushing the
queen rods (30) outwards.
3. Turn the motor over to remove the crank bearing (48).
The main king rod (12) can be lifted upwards and tilted
over the top of the crankshaft.
4. Remove the main king rod (12), piston (9), and cylinder
(8) from the motor
5. Remove the output shaft retainer (14), spacer (15),
and shims (16).
6. Remove the bolts (52) holding the output fl ange on the
case. The case can be removed.
7. Use a punch to drive the crankshaft inwards from the
fl ange plate (24A).
8. Remove the outer shaft bearings (55 and 56) by using
a punch. They are retained (18) on the inner side.
All parts should be thoroughly cleaned and inspected for
wear.
The motor number and its code should be incorporated
in any spares order. This is always stamped on the main
fl ange plate (24) located near the breather plug hole 46,
i.e. 230 Hx.
The seals and gaskets should be replaced using the motor
seal kit .
ASSEMBLY PROCEDURE
All parts should be clean and liberally coated with oil.
1. Output Shaft Assembly: Ensure the retaining rings and
bearings are fully seated. Lubricate oil seal (19) and
install with lip facing inward.
2. Push crankshaft to seat it and install spacer (15) and
retaining ring (14). Check gap and use shim (16) for
minimum end clearance.
3. Install new seal (25) and the output fl ange to the motor
case.
4. Set motor vertical with shaft down. Fit the 3 queen
rods (30) on to the piston assembly (9) and install into
cylinder (8) with gasket (7).
5. Fit piston assembly (9) onto the king rod (10) insuring
retaining clips are seated. Assemble a ring clamp onto
the king rod piston to compress the piston rings.
6. Put the crank spacer (13) on the crankshaft (20A/B).
Rotate the crankshaft until the crank pin is in the verti-
cal position (near breather plug 46).
7. Put king rod(12) with it’s piston assembly through the
opening “Z” marked on the drawing.
8. Twist and lift the rod over the end of the crank pin.
9. Fit crank pin bearings. Push the cylinder pot (8) with
gasket (7) onto the piston. The ring clamp is ejected
inward from the piston. Work the clamp off of the king
rod.
Summary of Contents for Braden BA2A
Page 2: ...2...
Page 25: ...25 THIS PAGE INTENTIONALLY LEFT BLANK...
Page 26: ...26 WINCH CROSS SECTION...