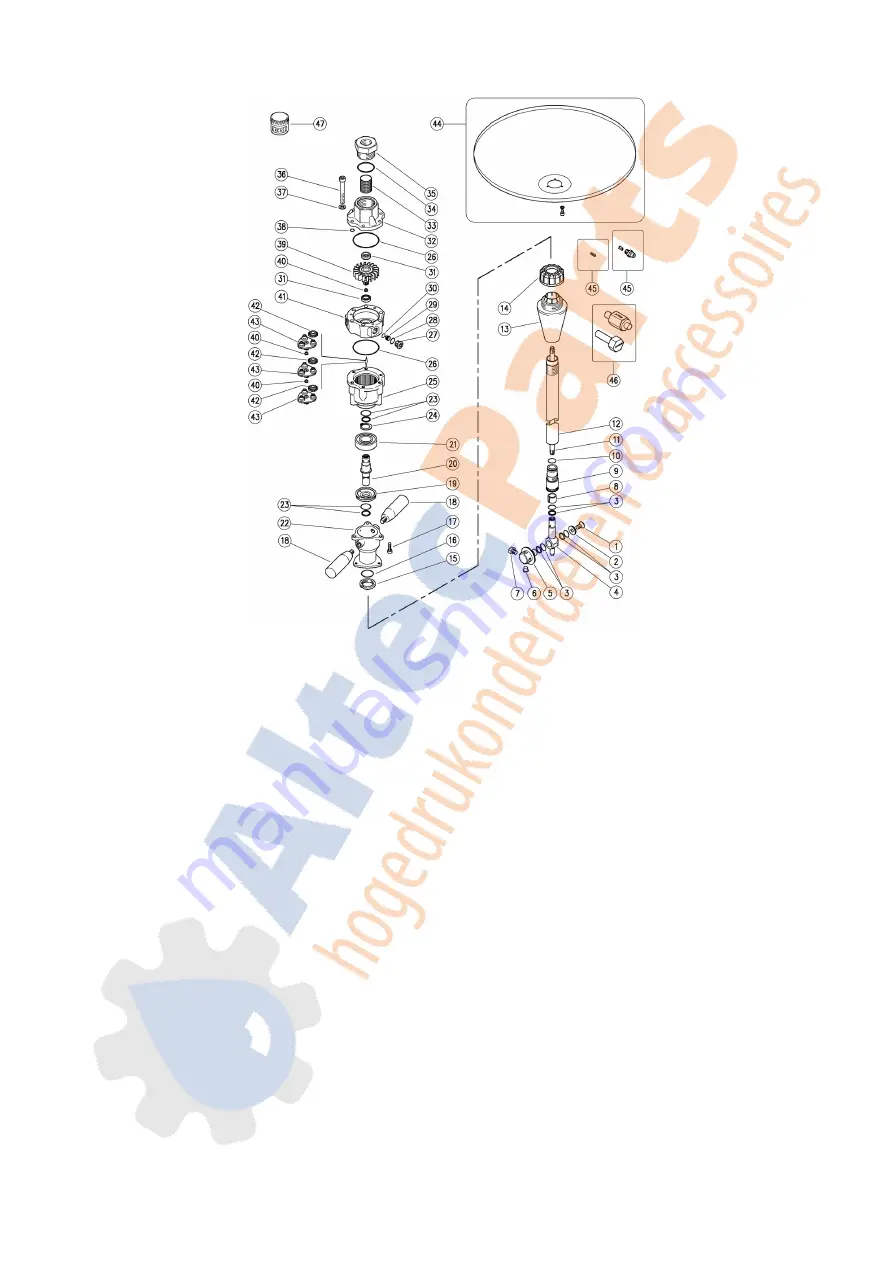
Last updated 06/07/2020
25.4600.20 MI63-50 Tank cl.,hydr.-driv.,2mm-inject.
25.4600.24 MI63-45 Tank cl.,hydr.-driv.,2mm-inject.
25.4600.30 MI63-50 Tank cl.,hydr.-driv.,3mm-inject.
25.4600.40 MI63-50-1/8 inject.4,00mm
25.4600.50 MI63-50 Tank cl.,hydr.-driv.,5mm-inject.
25.4902.25 MI63A-50 Tank cl.,hy.-driv.,2,5mm-Atex 2460