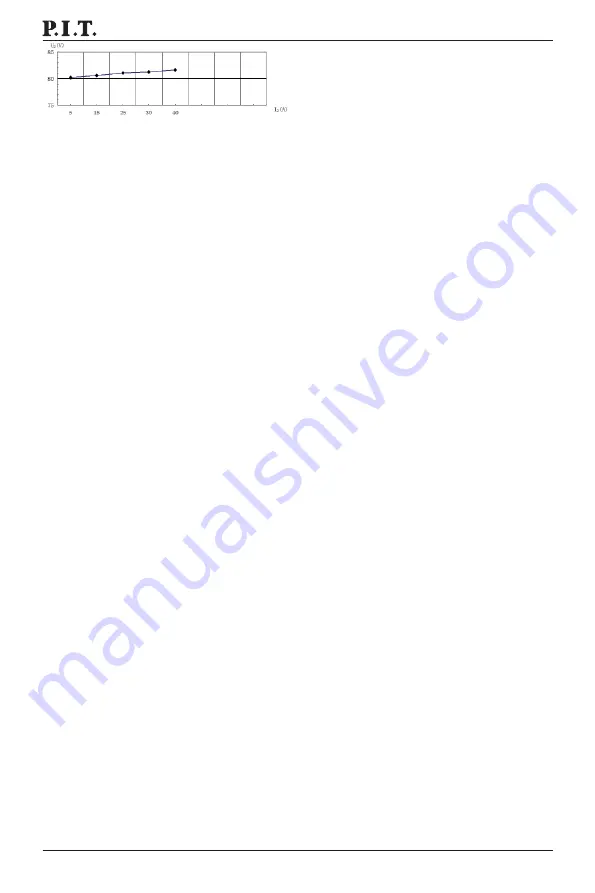
Plasma Cutting Machine
5
central system, the regulator must be set to
the maximum outlet pressure, which, howev-
er, must not exceed 8 atmospheres (bar) (0.8
MPa).
If the air is supplied from a compressed air
cylinder, the compressed air cylinder must be
equipped with a pressure regulator.
A common problem with many budget com-
pressors is that small-bore
fi
ttings and adapt-
ers are installed at the compressor outlet,
which, at high air
fl
ow rates, leads to a pres-
sure drop.
This can be avoided by connecting the
hose
,
not to the outlet of the compressor,
but directly to the receiver (for many models,
this requires removing the plug on the side
and inserting a fitting instead; however, it is
not recommended to use the plug at the bot-
tom to remove condensate for this).
The compressed air cylinder must never be
directly connected to the inlet of the plasma
system, only through a reducer-dryer!
Cutting tips
►
While cutting, move the torch perpendicu-
lar to the surface to be cut.
►
If it is necessary to burn through a hole
(“breakdown”), tilt the torch slightly to re-
duce the risk of backspatter and their ad-
hesion to the torch nozzle. In case of fre-
quent breakdowns of holes, promptly clean
the nozzle from adhering metal. It should
be remembered that ignition of the arc “for
breakdown” reduces the service life of the
nozzle, cathode and protective cap.
►
If you place a bath with water under the
product, you can almost completely re-
move the harmful effects of smoke and
metal splashes.
►
If the arc does not strike well, check that
the grounding clamp has a good contact
(check for paint, oil, dirt, rust at the con-
nection point).
►
If the arc “breaks” during cutting, the arc
burns unstably - check the air pressure
on the reducer-dryer, as a rule, the most
stable result is given by an operating pres-
sure of 0.5 MPa. However, depending on
the productivity, cutting thickness, you can
increase the pressure, while monitoring
the stability of the work. The best cutting
result and minimum wear on the nozzle
and cathode will be at maximum pressure,
but if the arc begins to break, reduce the
pressure on the reducer until the breaks
stop.
PRECAUTIONARY MEASURES!
Any con-
current, because the “V-A” slope is
fi
xed.
Equipment connection
►
Connect the nut of the plasma torch main
cable to the connection socket on the front
panel of the device. Check and, if nec-
essary, replace the working consumable
parts of the plasmatron: cathode, nozzle,
diffuser, protective cap. When installing
the cathode and guard, do not use tools -
a little finger force is sufficient. Attention!
Disassemble the plasma torch only with
the device turned off. Make sure that the
parts of the torch are cool!
►
Connect the control cable from the plasma
torch button to the front panel connector.
►
Connect the hose from the compressor/
compressed air system to the inlet of the
supplied gas reducer-dryer (air preparation
unit). Set the pressure on the pressure
gauge of the reducer-dryer to 0.5 MPa.
►
Connect the grounding cable insert to the
connector on the front panel of the device,
and fasten the earth clamp to the part.
Make sure there is good electrical contact
between the clamp and the part.
►
Ground the part and the body of the de-
vice. If possible, check with a voltmeter
whether the supply voltage is correct.
Make sure there are no cuts or breaks in
all cables and sleeves. Connect the mains
plug to the mains socket.
Beginning of work
►
Turn on the power with the power switch
on the back of the machine to the “On” po-
sition.
►
Set the cutting current according to the
thickness of the part to be cut.
►
To check, briefly press the button on the
plasma torch - the valve should open.
►
Touch the part with the nozzle, press the
button on the plasma torch, after the arc
has ignited, start cutting.
Special features when working
with compressed air
The used compressed air from the compres-
sor must have a pressure of at least 6 atmo-
spheres (bar) (0.6 MPa) with a minimum
fl
ow
rate of 200 l / min.
If the air is supplied from a compressor or
Summary of Contents for PCUT40-C
Page 1: ......
Page 2: ...Plasma Cutting Machine 1...
Page 10: ...9...
Page 11: ...10 18...
Page 12: ...11...
Page 13: ...12 15 10 PCUT40 C 50 60 100 1 2 3 4 5 6 PCUT40 C 190 250 50 6200 10 3 8...
Page 14: ...13 PCUT40 C 8 8 1 1 1 2 1 1 P I T V A 100 V A 0 5 6 0 6 M a 200 8 0 8 M a...
Page 15: ...14 0 5 80 10 40 C 0 3...
Page 16: ...15 P I T https pittools ru servises 0 55 85 0 50 80 2 2 2 1 2 OnePower 12 I 3 4...
Page 17: ...16 3 2 2 5...
Page 18: ...17...
Page 23: ......