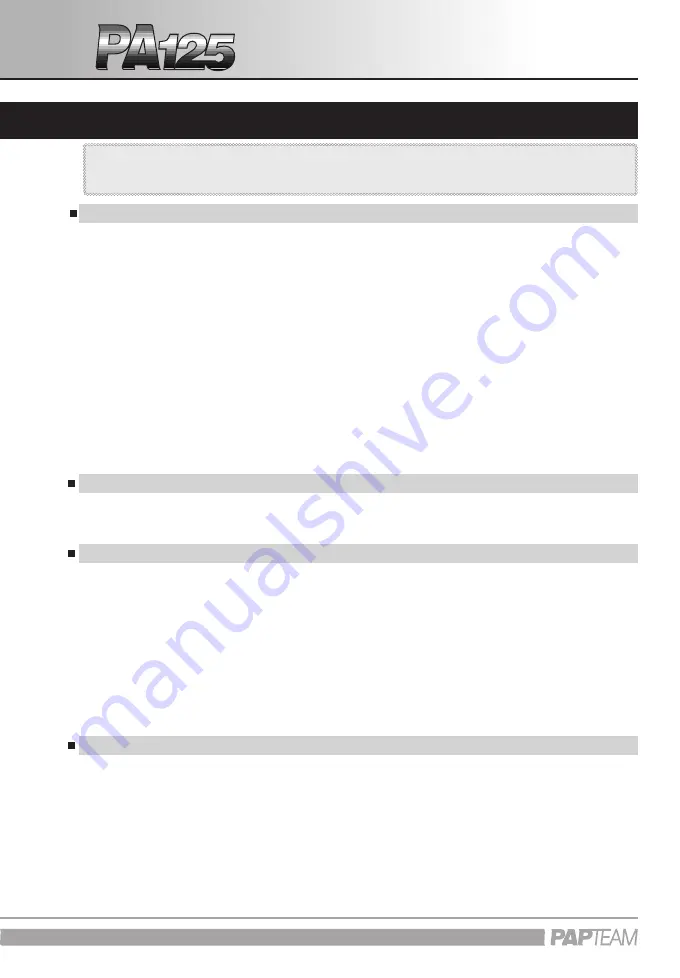
MAINTENANCE
FIRST 5 HOURS (RUNNING-IN)
1.- Check torque of all screws and nuts of the engine and of all other elements related,
especially the exhaust pipe.
2.- Check torque of all screws and nuts of the chassis and all its elements.
3.- Check torque of all cylinder head nuts with a torque wrench (16 Nm or 1.6 Kgm), with a
cold engine in order to avoid distortions.
4.- Check inside Walbro carburettor petrol filter by opening the inner part cover.
5.- Check torque of all screws of the wood propeller (max. 11 Nm or 1,1 Kgm), carbon
propeller (max. 8 Nm or 8 Kgm)
6.- Check spark plug. The inner part colour should be clear brown and have a 0.5 mm gap
between electrodes.
7.- Remove the reduction gear from the engine casing body and clean the dust of the friction
material from clutch. Check state of clutch springs.
8.- Adjust Paramotor ACTIVE SYSTEM anchor arms to paraglider in order to get the best
balance in flight (during the 1st hour of flight).
Maintenance.
EVERY 5 HOURS
1.- Thorough cleaning of engine and all other elements related for a proper operation.
2.- Fix any issue, especially if it is not under the normal checking periods.
EVERY 20 HOURS. Same as every 5 hours, and:
1.- Check main engine elements: main screws and nuts, cylinder head torque (12 Nm or 1.2
Kgm), outside petrol filter and inside carburettor filter, wood propeller torque (max. 11 Nm or
1,1 Kgm), carbon propeller torque (max. 8 Nm or 8 Kgm), spark plug check, clutch check
and its springs.
2.- Check spark plug. The inner part colour should be clear brown and have a 0.5 mm gap
between electrodes. Replace spark plug after first 25 hours (model NGK B10ES).
3.- Check amount of reduction gear oil via the sight screw located under its left front side
(PICTURE 24), adding, if necessary, (by means of its top screw), max from empty is 40
ml. of SAE 140.
4.- Check movement of exhaust pipe elements and their supports.
EVERY 50 HOURS. Same as every 5 + 20 hours, and:
1.- Check state and elasticity of inlet plates. If they are worn or not elastic anymore, please
replace them.
2.- Check state and elasticity of carburettor membranes. If they are worn or not elastic
anymore, please replace them.
3.- Check state of the clutch shoes and the clutch bell , Clean inside the clutch bell.
4.- Clean carbon residue out of cylinder head, exhaust manifold, piston, and cylinder. Check
con rod needle bearing set by vertically moving the piston. Change cylinder gasket if you
consider it is worn and cylinder head gasket (O-ring).
5.- Check spark plug and change if necessary. Check contact between spark plug cable and cap.
IMPORTANT: after your engine having running one hour check torque of all cylinder head
nuts with a torque wrench (16 Nm or 1.6 Kgm)
USER MANUAL
31
Summary of Contents for RM80
Page 1: ...page 2 page 10 page 28 page 36 USER MANUAL...
Page 39: ...Electronic box USER MANUAL 39...
Page 40: ...40 USER MANUAL...