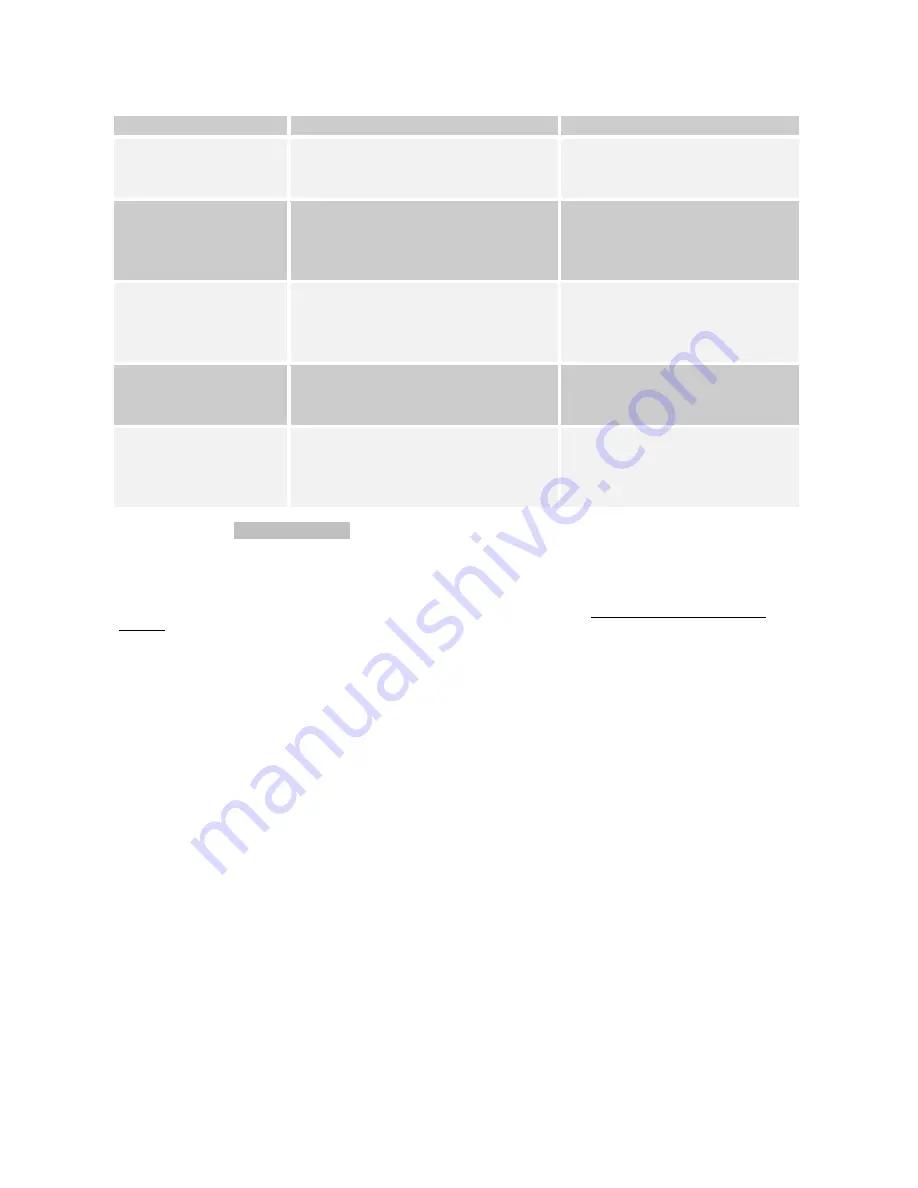
Last Update: 30/01/17
3
PROBLEMS AND SOLUTIONS
PROBLEMS
PROBABLE CAUSES
SOLUTIONS
Valve cycles
- Air inside the system
- Worn out seals
- Clogged circuit
- Flush out
- Replace
- Clean or widen passages
The valve does not reach
pressure
- Unproper nozzle size
- Seat/shutter/ball worn out
- Damaged nozzle
- Impurities
- Modify
- Replace
- Replace
- Clean
Pressure drop
- Worn out nozzle
- Pump gaskets worn out
- Valve seat worn out
- Air inside the system
- Replace
- Replace
- Replace
- Flush out
Pressure spikes
-
There is not a min.5% of total flow in bypass
- Clogged nozzle
- Re-adjust
- Clean
- Repeat adjustment and replace nozzle
Water leakage from bypass
Valve pounding
- O-ring seat damaged
- Damaged seat
- Impurities or worn out valve pumps
- Replace
- Replace
- Clean
REGULATIONS :
see norm manual
The accessory hereby described bears the CE marking in accordance with the Norms and Directives
applied on the Declaration of conformity.
For a correct utilization, follow the directions described in this manual and re-print them on the Use and maintenace manual of the
machine.
Make sure that you are given
the Original Conformity Declaration
for the accessory chosen. The present manual is valid for all
unloader valves named
VRP 200.
MAINTENANCE
Maintenance has to be carried out by
Specialized Technicians.
STANDARD: every 400 working hours (circa 10,000 cycles), check and lubricate the seals with water
resistant grease.
SPECIAL: every 800 working hours( circa 20,000 cycles), control the wear of the seals and internal parts and
if necessary, replace with original PA parts taking care during installation and to lubricate with water resistant
grease.
ATTENTION: reassemble the valve in the correct manner paying special attention how to set the valve as
described in the paragraph PRESSURE ADJUSTMENT/SETTING.
The manufacturer is not to be considered responsible for damage as a result from incorrect fitting and
maintenance
Technical data, descriptions and illustrations are indicative and liable to modification without notic