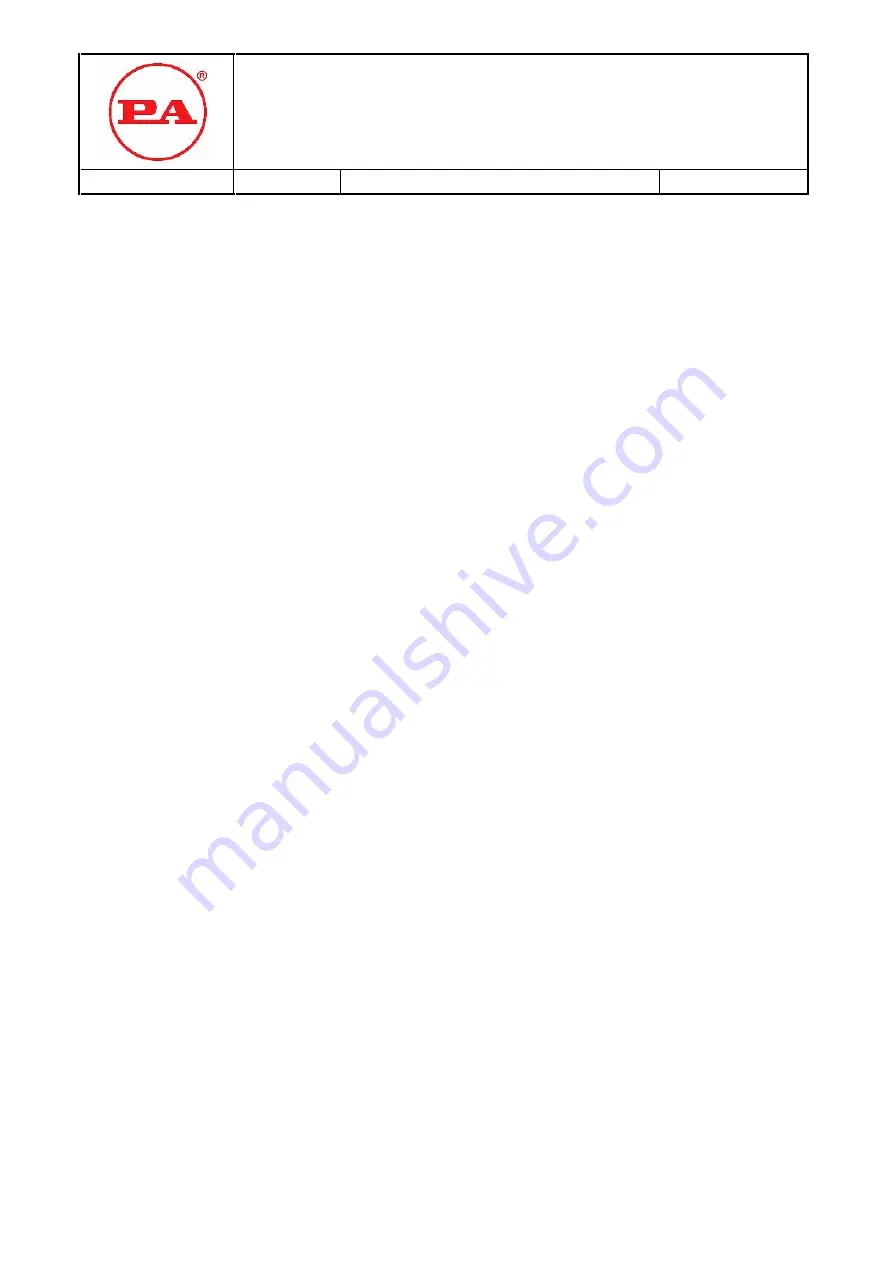
ATEX UNLOADER AND RELIEF VALVES
SAFETY NOTE
SN03
Rev. 00
Date 27/10/2020
Pag. 5 of 10
Qualified/Specialized Technician
: personnel who was trained for installation, adjustment, maintenance, repair. It is
required that the technician shall be trained and allowed to perform such tasks, and to have specific knowledge not
only of the tool and the risks stemming from its use, but also the possible risks of the appliance in question.
Temperature Class (T)
: it is the maximum superficial temperature of the appliance (taking into account also the safety
coefficient as reported in UNI CEI EN ISO 80079-36:2016. It also corresponds to the max. surface temperature of the
valve.
3. INSTRUCTIONS FOR USE
3.1 STORING, SHIPPING AND MOVING
The valves are supplied with adequate packaging. The unloading and moving of the tools shall be carried out by
trained personnel, who is also responsible for checking that the order and the freight match.
It is necessary to carefully move the valve to avoid shock impacts, and therefore, possible deformations and cracks
which could successively determine leaking of the product contained through the attachment points of the valve a/w
possible trigger source (sparks, adiabatic compression, etc.).
Localities of Warehouse storage, conservation, transport and movement of the valves must guarantee that they are
not subject to shock impacts, tumbles, deterioration and other damaging which could compromise the function of the
valve.
Any eventual damage must be immediately communicated to P.A. S.p.A. for assessment.
3.2 INSTALLATION
3.2.1 WARNING
Each installation or reinstallation must be performed by qualified personnel, duly trained and informed on the related
risks, even concerning the instructions of this document.
When using the utensils do not apply excessive force rotation on the connections in the presence of a potential
explosive atmosphere.
The use of utensils in zone 1/21 and 2/22 is allowed with particular instructions under the directive UNI CEI EN ISO
80079-36:2016 which has to be known by the operator.
Installation errors can provoke deformation or structural collapse of the pipe connection, also a loss of fluid in the
ambient.
Installation errors can compromise the regular movement with effective possibility of sparking.
During installation, keep to the direction of flow indicated by the arrows on the valve body and on the construction
drawings.
3.3 FILTERING OF LIQUID
The fluid sent from the system to the valve has to be filtered in order to prevent particles to slip through causing
malfunction and therefore frequent maintenance interventions. The recommended sealed filter has to be at least 300
microns. We recommend to clean it every 100/300 hours and, in case of filter breakage, replace it.