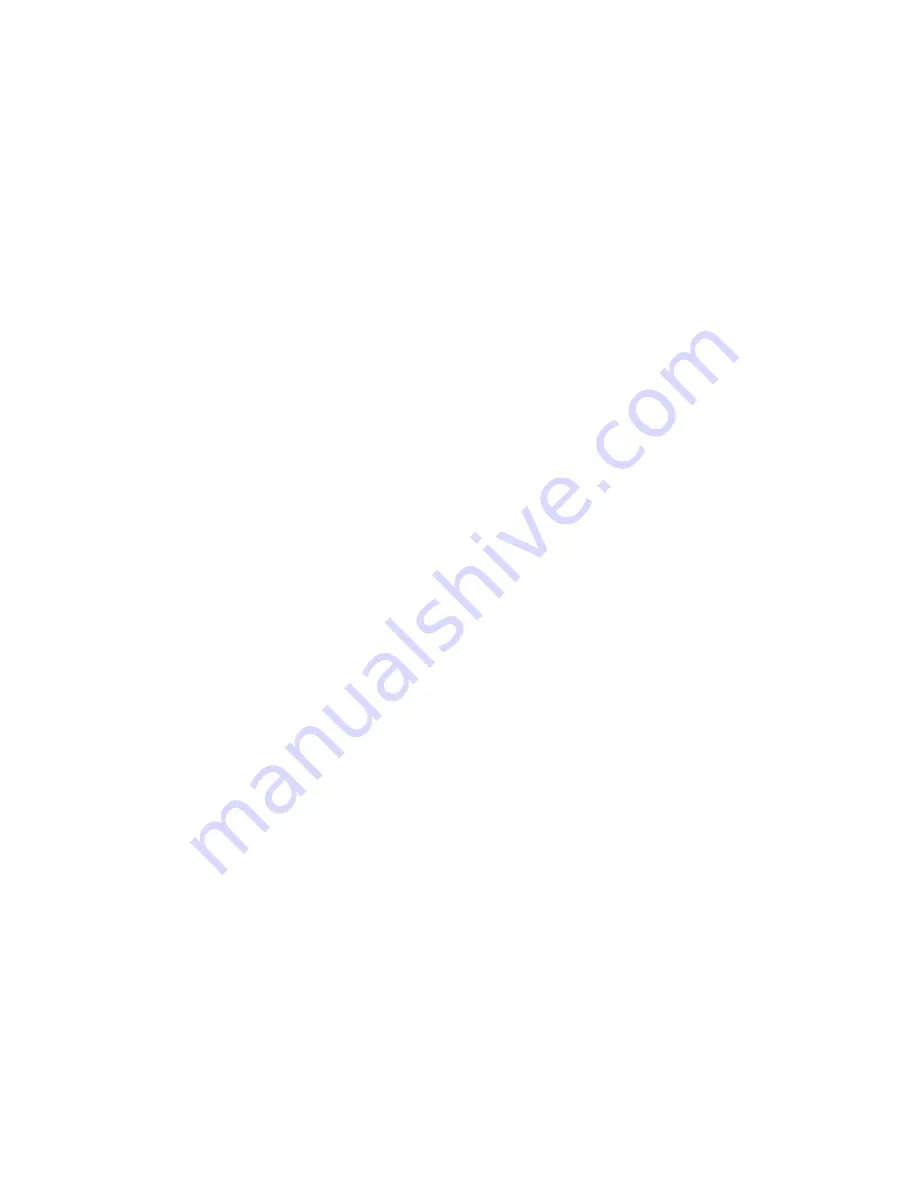
5
maximum force. If this does not eliminate leakage, try a
new valve assembly. If then the valve does not shut off
completely, send the torch to a repair station for reseating
of the body.
Cutting Oxygen Valve
If leakage develops around the oxygen valve stem, re-
place the valve packing bushing. If leakage develops
through the oxygen valve, replace the valve seat. Re-
placement procedure as follows:
1. Unscrew the lever attaching screw and lift the lever
off.
2. Unscrew the valve stem guide and remove the valve
assembly from the guide.
3. Use Leak Test Solution to moisten the stem head,
then remove the packing bushing and ferrule. Re-
move the sealing ring from the bushing. Lift off the
spring and spring support.
4. Replace the valve seat (stem) if necessary and any
other parts which are worn or damaged.
5. Reassemble the valve following the above instruc-
tions in reverse order.
Cleaning Cutting Nozzle:
If the cutting nozzle does not
produce straight, uniform flames, or if any of the pre-
heat nozzle holes become clogged, clean them by us-
ing the serrated tip cleaners in the cleaning kit supplied
with the torch, part number 751F00. Maintaining clean
preheat holes is essential for quality performance of this
equipment.
If the cutting orifice becomes clogged or fouled, gently
insert and twist the appropriate tapered cleaning tool
found in the cleaning kit. Nozzle P/N 2118703 should
only be cleaned with Oxweld nozzle cleaning compound
P/N 761F00. The use of twist drills for cleaning holes is
not recommended. Nozzles should be cleaned periodi-
cally in a solution of OXWELD Nozzle Cleaning Com-
pound (P/N 761F00), made up and used as directed on
the container in which it is packed.
MAINTENANCE
For all repairs other than those covered below, send the
torch to ESAB Welding & Cutting Products
Remanfacturing Center, 411 South Ebenezer Road, Flo-
rence, SC 29501.
Testing Seats:
Under normal use the internal seating
surfaces in the nozzle socket should last the life of the
torch. Should reseating be necessary, reseating should
be done only by the factory or a qualified repair person.
To test the seat, thinly coat the seating surfaces of a
new nozzle with nondrying Prussian blueing. Insert the
nozzle into the nozzle socket without the nozzle nut and
rotate the nozzle by hand one half turn. Remove the
nozzle and observe the seating surfaces in the socket.
Blueing should be evenly distributed on both seating
surfaces. Depressions or the absence of uniform blue-
ing indicates the nozzle socket requires reseating.
Reseating:
By hand, screw in reseating tool P/N
5230207 into nozzle head. Do not overtighten or dam-
age to head could result. While gently tightening and
holding threaded nut of reseating tool, slowly rotate
reamer allowing tapered seat to be reseated. Make sure
reamer is rotated at least two revolutions so that reseated
surfaces are true. Retest seats and repeat if necessary
until seating surfaces have been restored. Clean out
metal shavings before putting torch back into service.
PM nozzles cannot and should not be reseated.
Preheat Valves:
Leakage around either throttle valve
can usually be corrected by tightening the packing nut
slightly. If this does not stop the leakage, replace the
throttle valve.
If either preheat valve fails to shut off completely, re-
move the throttle valve assembly from the torch. With a
clean cloth, wipe the ball in the end of the stem. Then
reinsert valve assembly and tighten it several times with
Summary of Contents for PM-GST
Page 7: ...7 ...