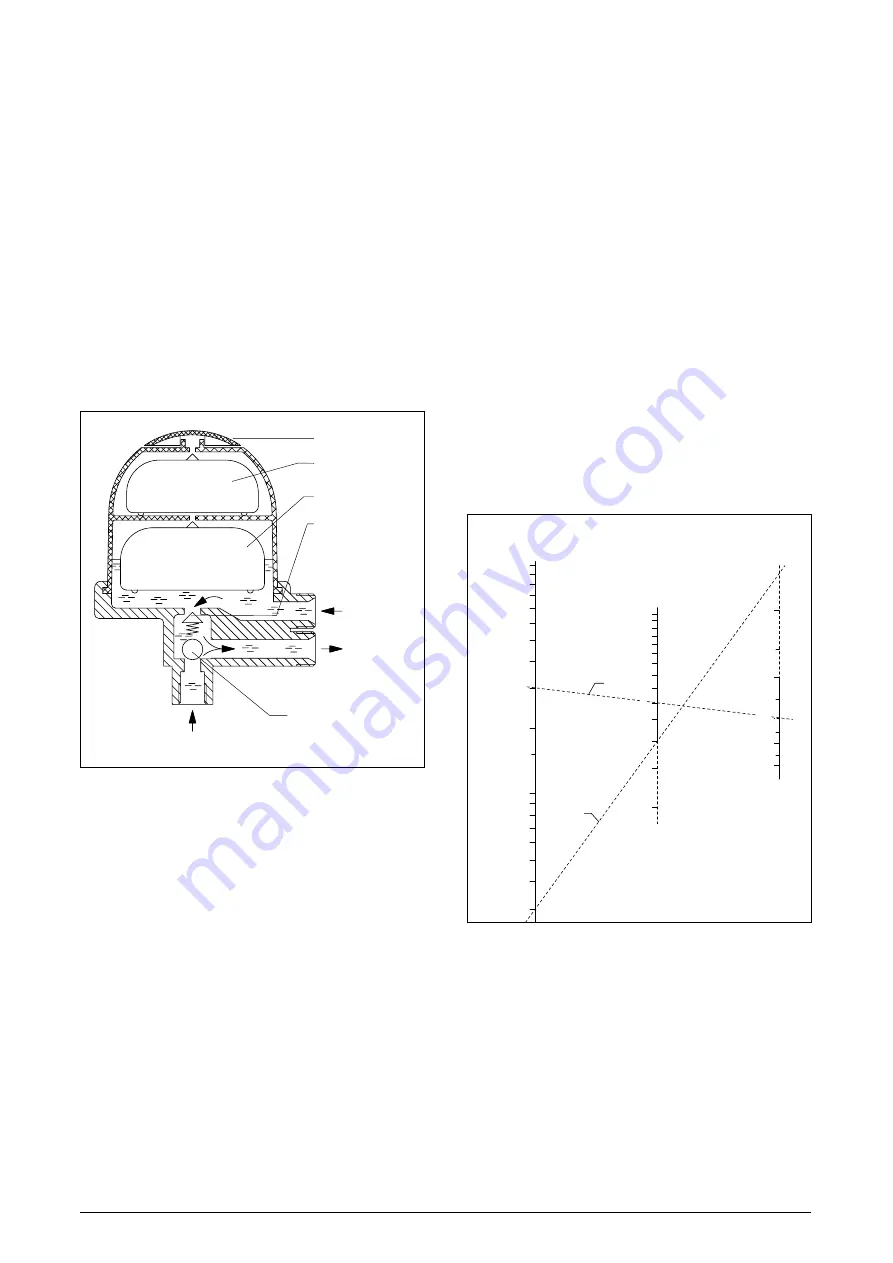
2
2004 Oventrop
Function:
Oventrop heating oil deaerator “Toc-Uno-N” for automatic
deaeration of heating oil.
The burner pump draws oil through the suction pipe via the
filter mounted in front of the deaerator, the connection pipe
and the check valve. Normally, a small portion of oil is
pumped to the nozzle by the burner pump and is burnt
(per 10 kW of heat output about 1 litre of oil per hour). The
excess is fed into the deaerator via the return pipe. Air and
gas emissions rise and are expelled into the atmosphere via
the float valve. The deaerated oil is fed into the supply via a
diaphragm controlled valve. As a result, only the used
quantity is drawn from the tank via the suction pipe and the
filter. At the same time, the working temperature of the oil
pump is used for pre-warming the oil.
Under working conditions, a relatively constant filling height
will be present in the lower part of the float case. Depending
on the working conditions, this part may even fill up
completely.
If heating oil enters the upper part with the security float, the
deaerator has to be replaced.
The supply and return connection must not be mixed up as
this may cause damage to the deaerator and the burner
pump.
Pressure test:
When carrying out the pressure test of the suction pipe, the
pressure test device must not be connected to the “Toc-Uno-
N” as the integrated check valve will prevent the pressure
transmission on the tank side.
Moreover, the float valves of a new unfilled “Toc-Uno-N” are
opened so that it should not be included in the pressure test.
Notes:
Do not use detergents containing alcohol or solvents as
these may damage the plastic parts.
Sizing of the suction pipe:
The suction pipe towards the tank should be sized in such a
way that the velocity of the heating oil during burner operation
is between 0.2 and 0.5 m/s (DIN 4755). If the suction pipes are
oversized, velocity is reduced in such a way that the gas
emissions are not transported constantly and gather as big air
bubbles in upper pipe sections. If a big air bubble reaches the
burner, it may cause a malfunction.
For small burner units in one or two family houses, the inner
pipe dimension of 4 mm (e.g. pipe 6 x 1) is often sufficient.
Apart from the velocity, the flow resistance and the suction
height have to be taken into consideration.
b
a
min.
min.
3
2
2
3
4
0.1
0.5
0.4
0.3
0.2
15
10
9
8
7
6
5
4
80
70
60
50
40
30
20
10
9
8
7
6
5
*
90
100
110
12
Examples:
a. For a pump capacity of 30 l/h (about 300 kW), with a
medium suction speed of 0.3 m/s, a pipe of 8 x 1 mm with
an inner diameter of 6 mm is required.
b. A small installation with a heat output of 30 kW,
corresponding to a flow rate of 3 l/h, is equipped with a
pipe of 6 x 1 with an inner diameter of 4 mm. The velocity
is very low then (about 0.07 m/s), but possible airlocks are
very small and do not cause malfunctions.
Installation:
The heating oil deaerator is to be installed at a suitable
location with the help of the enclosed fixing plate. To mount
the latter on the burner wall by use of the enclosed sheet
metal screws, provide 3 mm tapping points. Care should be
taken that the max. ambient temperature does not exceed
60 °C, i.e. not mount the “Toc-Uno-N” near an un-insulated
part of the boiler or the exhaust pipe or above flaps of the
heating which can be opened.
The heating oil deaerator is to be installed vertically.
It can be installed above and below the oil level.
For function control, the “Toc-Uno-N” should be installed at a
location which is well visible and easily accessible.
When converting from two pipe systems to one pipe
operation, the pipe dimension has to be reduced if required,
see “Sizing of the suction pipe”.
If constructional conditions allow, the pipe should be installed
in such a way that it acts as a “self-monitoring suction pipe”
according to TRbF 50. It should then be installed with an even
decline towards the tank and all check valves in front of the
“Toc-Uno-N” have to be removed. If a leakage occurs, the
column of liquid in the declining pipe breaks off.
Functional scheme:
Oil capacity
in l/h
Inner pipe
diameter
in mm
Oil velocity
in m/s
Velocity of the heating oil in suction pipes
during operation according to DIN 4755:
0,2 bis 0,5 m/s
* Avoid dimensions of less than 4 mm
Nomogram:
Return
Security float
Float
Differential
pressure
relief valve
Cap
Supply
from
tank
Non-return ball
check valve