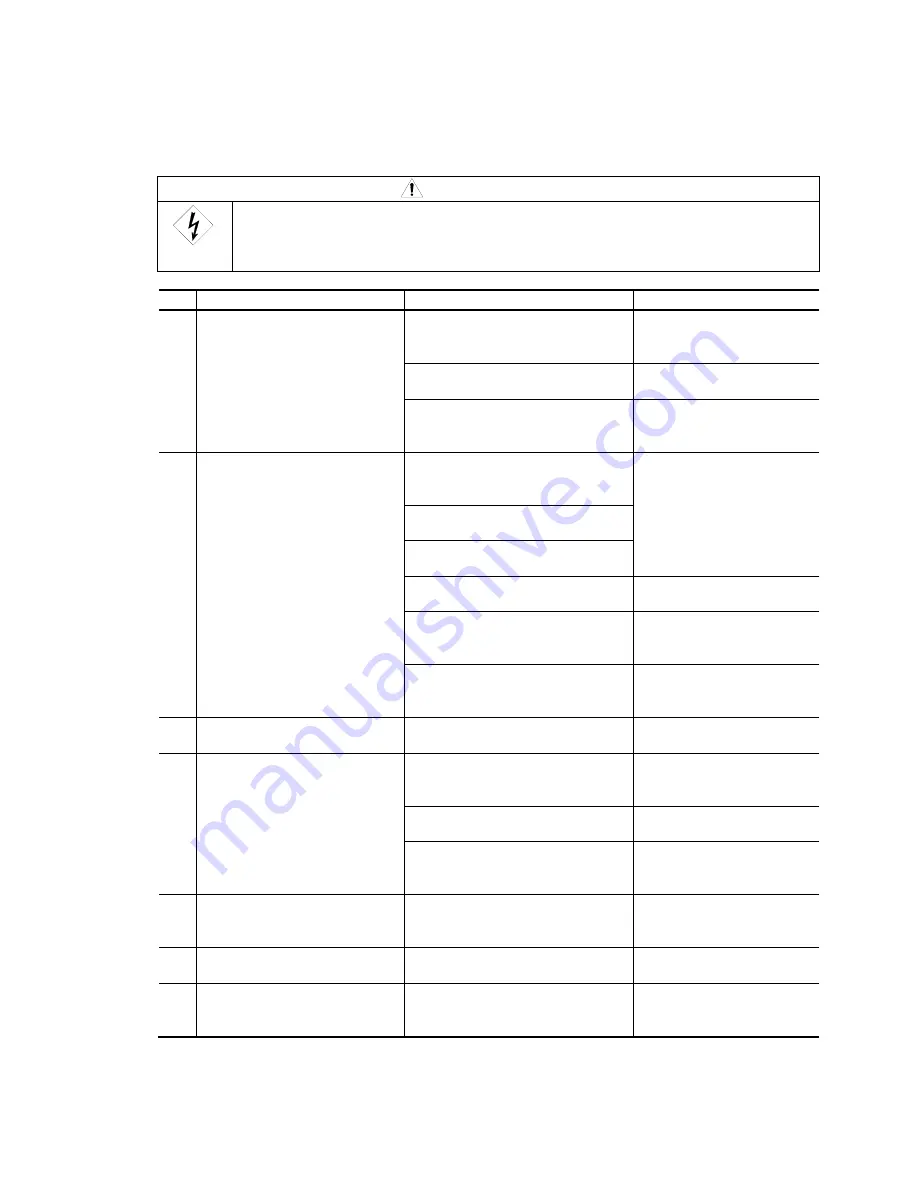
No. U5260
P. 17 / 27
8. MAINTENANCE AND TROUBLESHOOTING
8.1 Carrying Out Maintenance
WARNING
●
Do not touch the charging parts inside or outside the wire feeder.
●
Disconnect the wire feeder from the welding power source by turning off the line
disconnect switch in the power box to avoid an electric shock before carrying the
equipment.
No. Problem
Cause
Solution
1
Wire gets deformed.
Wire pressure is too strong.
Refer to “Recommended
wire adjustment” in Section
7.2.
Feed roll of wrong wire size is
used.
Replace it with the feed roll
of proper wire size.
Feed roll and pressure roll are
worn.
Replace the feed roll
and the pressure roll
with a new ones.
2
Wire is not fed.
Poor contact and breakdown in
the control cable.
Check the socket.
Check the cables and
replace with new ones.
Poor contact and breakdown in
the encoder cable
Poor contact and breakdown in
the voltage detection cable
Trouble with the motor
Replace the motor with a
new.
Wire pressure is too weak.
Refer to “Recommended
wire adjustment” in Section
7.2.
Dust and chip are accumulated
on the outlet guide and on the
feed roll.
Remove the dust and chip.
3
Pressure roll does not rotate
smoothly.
Failure of the pressure roll holder.
Replace it with a new.
4 Shield gas is not supplied
when pressing the torch
switch.
The discharge valve is closed of
the gas cylinder.
Open the valve.
Lack of gas pressure in the gas
cylinder
Check gas pressure.
Failure of gas solenoid valve
After checking the gas
solenoid valve, replace it
with new ones.
5 Shield gas supply does not
stop.
Failure of gas solenoid valve
Check the socket. Check
the cables and replace
with new ones.
6
Defective gas hoses
Crack in the gas hose
Replace them with new
ones.
7 Wire does not fed smoothly
through the wire reel.
Adjustment of the brake is either
too strong or too weak.
Refer to “Adjustment of the
wire reel hub” in Section
7.3.