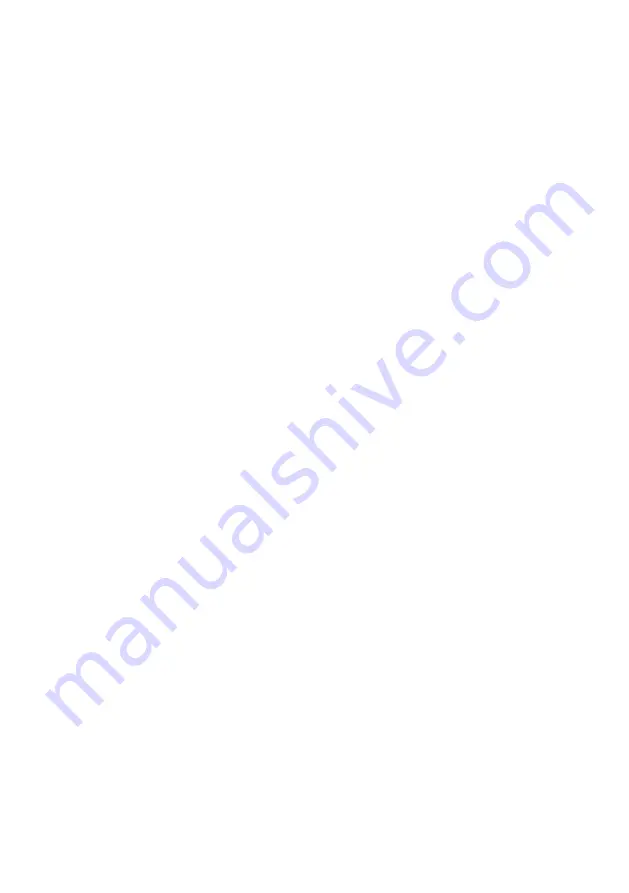
14
5. MAINTENANCE, SAFETY AND SERVICING
Maintenance must be carried out by a compe-
tent person.
5.1 Draining/flushing
1. Turn off mains supply.
2. Connect hose pipe to drain cock at base of
cylinder.
3. Open hot tap. Open drain valve and open
temperature & pressure relief valve.
4. Allow vessel to drain. Follow commissioning
instructions (above) to refill.
5.2 Recommissioning
Cold or tepid water discharge from tundish
The tundish should be installed away from electri-
cal devices.
1. Close cold water supply valve
2. Open a hot tap.
3. Repressurize the expansion vessel air charge
to its set level.
4. Close hot tap
5. Open the cold water supply valve
Hot water discharge from tundish: This indicates a
malfunction of a thermal cut-out, operating ther-
mostat or the combined temperature and pressure
relief valve. Turn off the electrical supply to the
immersion heater and also isolate an indirect unit
from the boiler. Contact the installer or competent
engineer.
5.3 Safety and maintenance
Safety cut-out
1.
The safety cut-out operates if:
a). Wiring is incorrect.
b). The immersion heater thermostat or
cylinder thermostat fails.
c). Thermostat is set too high.
2. Remember before resetting the safety cut-
out or altering the thermostat setting, isolate
electrical supply to the unit prior to removal
of the electrical box lid.
3. Reduce thermostat setting and press the re-
set button. After adjustments are completed,
ensure the lid to the electrical box is replaced
correctly and the retaining screw is fitted.
4. If still out of operation, contact installer.
Pressure reducing valve
1.
Isolate the cold water supply and open a
ground floor cold tap.
2. Unscrew the pressure reducing cartridge
3. Clean the filter mesh and the cartridge under
running water.
4. Replace cartridge ensuring that strainer is
correctly located and reassemble the unit.
Pressure Reducing Valve cartridge and
strainer Part No. REDC355030 - 3 Bar.
Expansion relief cartridge
1.
Isolate the cold water supply and open a
ground floor cold tap.
2. Unscrew blue expansion relief headwork
from valve body.
3. Clean valve seat face and seating - do not
scratch or damage either seat face or seating.
4. Refit in reverse order. Do not overtighten
Expansion valve cartridge and seat Part No.
RELC 214005 6.0 Bar.
Complete Expansion Valve Part No. PREL
355030.
Expansion vessel
Repressurizing vessel:
1. Close cold water supply valve
2. Remove cap covering air valve
3. Adjust the vessel air pressure in relation to
the set incoming water pressure using an air
compressor or hand pump.
4. Replace the air valve cap.
Note: If water emits from the air valve the vessel is
punctured and must be replaced.
It is a condition of the guarantee that annually
a competent person:
1.
Inspects and cleans the line strainer.
2. Checks the operation of the expansion relief
valve and temperature & pressure relief valve.
3. Recommissions the cylinder in accordance
with the instructions above.
5.4 Corrosion resistance
Stainless steel is naturally corrosion resistant to
mains water supply. No specific maintenance is
required to maintain this resistance. Please see
guarantee terms for permissable water con-
tent. Please note: OSO cylinders are not guar-
anteed for use with a private water supply.
The immersion heater can be removed to provide
visual inspection access to the cylinder.
For further information contact your Building
Control Office.