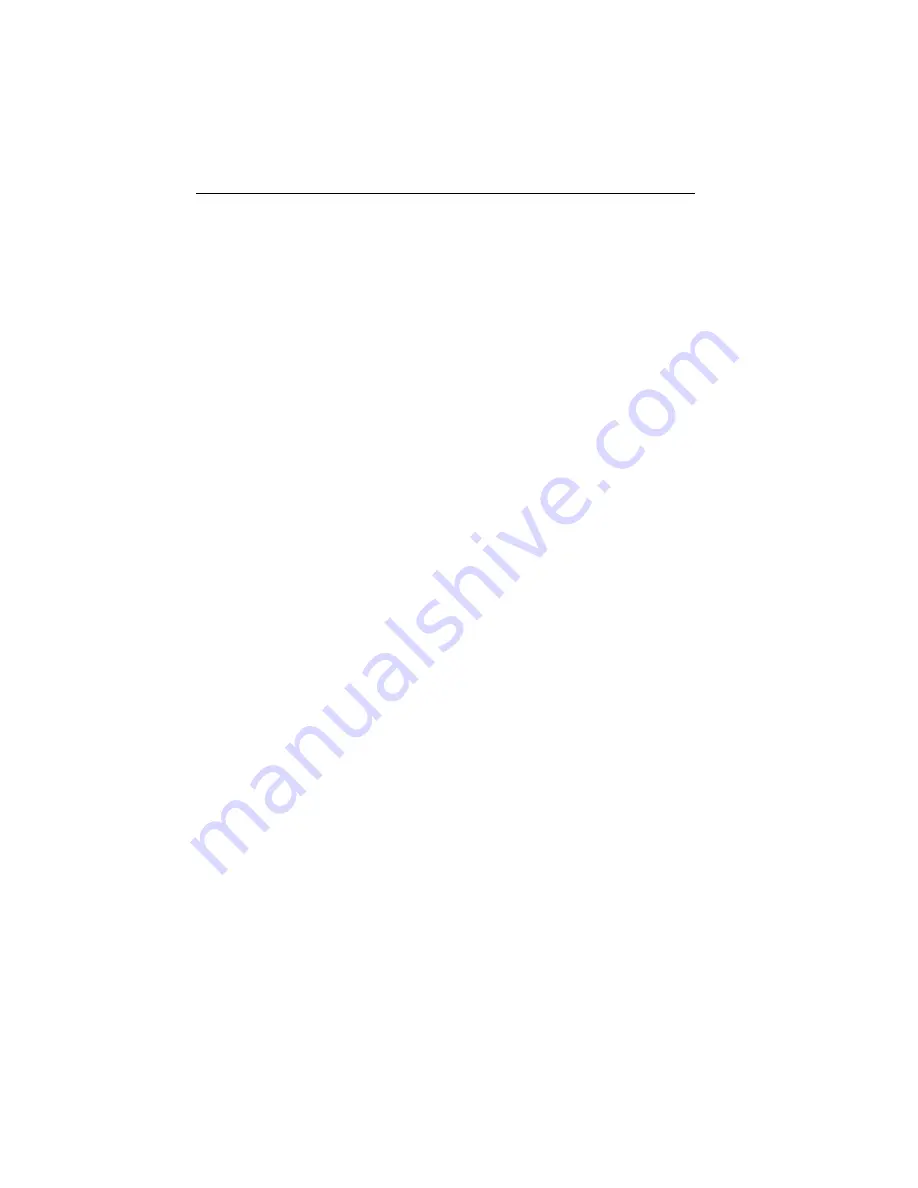
Table of Contents
vi
31200205
9.1 Product Specifications......................................................... 9-1
Fluid and Lubrication Capacities .................................... 9-1
Tires................................................................................ 9-2
Performance ................................................................... 9-3
Dimensions..................................................................... 9-6
Declaration of Vibration (CE).......................................... 9-8
Noise Emission Level (CE)............................................. 9-8
Summary of Contents for JLG 3508PS
Page 2: ......
Page 26: ...Section 1 General Safety Practices 1 14 31200205 This Page Intentionally Left Blank...
Page 45: ...Section 3 Controls and Indicators 3 9 31200205 This Page Intentionally Left Blank...
Page 68: ...Section 3 Controls and Indicators 3 32 31200205 This Page Intentionally Left Blank...
Page 85: ...Section 5 Attachments and Hitches 5 5 31200205 This Page Intentionally Left Blank...
Page 139: ...Section 7 Lubrication and Maintenance 7 7 31200205 17M OZ2430 EVERY 8...
Page 141: ...Section 7 Lubrication and Maintenance 7 9 31200205 17M OZ2440 2X 50 EVERY...
Page 160: ...Section 8 Additional Checks 8 6 31200205 This Page Intentionally Left Blank...
Page 174: ...Inspection Maintenance and Repair Log Date Comments...
Page 176: ......
Page 177: ......