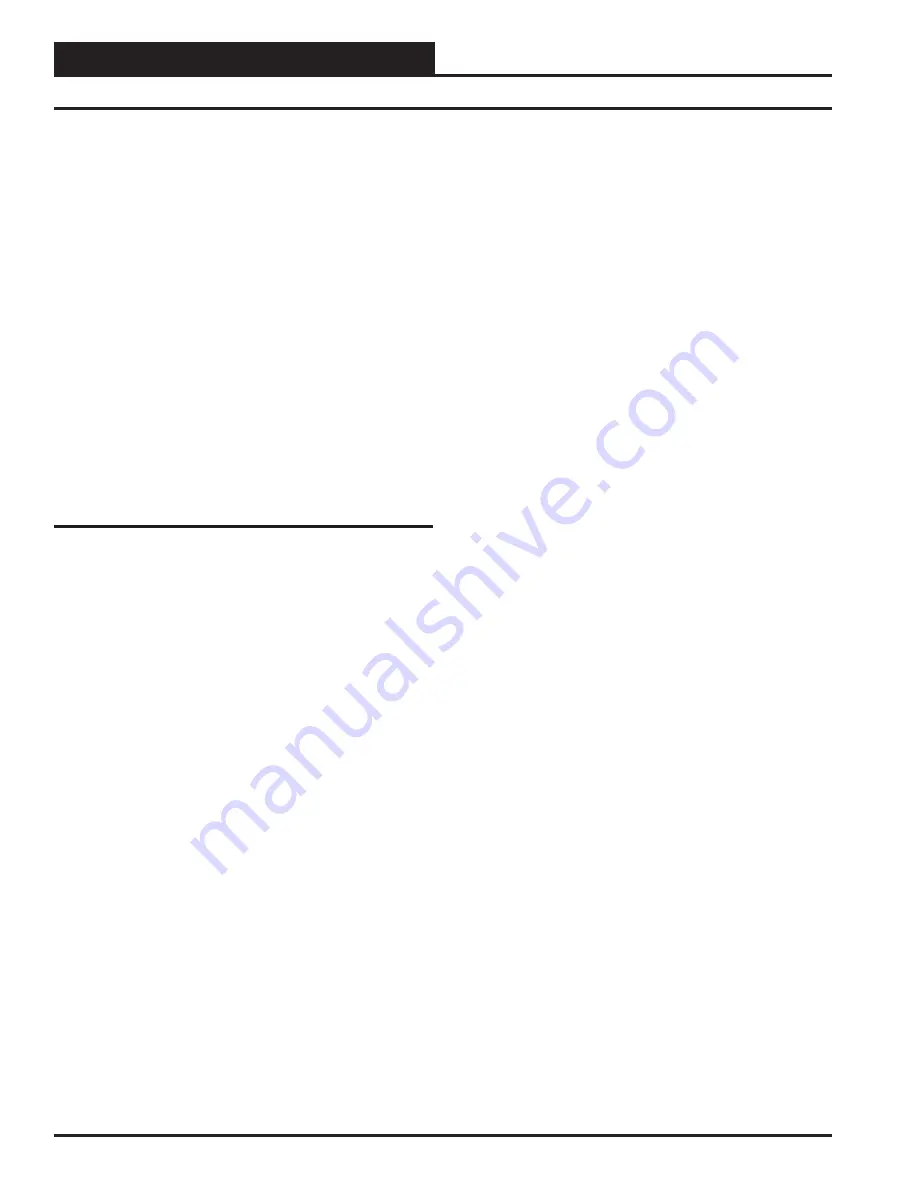
34
VAV/Zone Controller Package
SEQUENCE OF OPERATIONS
VAV/Zone Damper Control
Parallel Flow Fan Terminals
If the VAV/Zone Controller has been confi gured as a Parallel
Fan Powered terminal unit, the Parallel fan will run continuously
when the VAV/Zone Controller is in the Space Heating Mode no
matter whether “Check for Main Status” has been selected or not.
At all other times, the fan will be off .
If “Check for Main Status” is selected, the damper will remain in
the closed position until the HVAC unit controller is broadcast-
ing that the HVAC unit fan is operating, regardless of whether it
is calling for heat or not. The damper will be held at the closed
position until the main fan status broadcast is received. Once the
broadcast is received, the damper will then move to its Night
Minimum position. If “Check for Main Status” has not been
selected, the damper will stay in the closed position until Space
Heating Mode is initiated. When in Space Heating Mode the
damper will move to its Reheat Minimum position. When in
Supply Air Heating Mode the damper will modulate to maintain
the Unoccupied Heating Setpoint.
Damper Control
The damper position is calculated by the demand from the
space. This calculation can also include an optional Integral
function. This prevents the damper/airfl ow from stagnating at
a position somewhere above the setpoint because the Supply
Air Temperature or Duct Pressure isn’t quite enough to satisfy
the space at the currently calculated proportional position. The
Integral causes the calculation to keep adding a small amount of
the proportional error back into the damper/airfl ow position each
time a new position is calculated. The amount the Integral adds
back in is user-adjustable. This value is presented as a number
between 0.0 and 10.0. That means that if the integral is less than
1.0, you are adding a percentage from 0 to 100% of the error
back into the calculation. If you increase the Integral above 1.0,
you are adding more than 100% back in.
With just proportional control, a 1ºF error would cause a 50%
increase in damper/airfl ow if the Integral is not included. (1°F
is half of the 2ºF Proportional Window).
If you had set the Integral to 1.0, the calculation would add 2%
to the current damper/airfl ow calculation each time. The calcula-
tion occurs once every 10 seconds, so it would take a little over
4 minutes to reach the programmed 100% maximum.
Example:
1. 50% Remaining / 2% Integral = 25 moves to get to a
100% Maximum
2. 25 Moves times 10 seconds = 250 seconds or a little
over 4 minutes to reach the 100% maximum damper/
airfl ow position.
Of course, diff erent Space Temperature errors and diff erent In-
tegral values cause this calculation to operate slower or faster. It
is up to the user to determine the optimum setting that provides
the tightest temperature control without causing the damper to
continue to hunt or modulate which causes premature wear of the
actuator gears and motor.
On pressure dependent terminal units, the damper position is
maintained to within ± 3% of the calculated position. No attempt
is made to position the damper exactly on the calculated posi-
tion. This reduces wear and tear on the actuator gears and motors
and the amount of airfl ow involved is not aff ected by that small
amount of damper error.
On pressure independent terminal units, the airfl ow is maintained
to within roughly 3% of the terminal unit size constant but no
tighter than 16 CFM on the smallest terminal units. The actual
control window is based on the formula:
Window = Terminal unit size X Square Root (1 / 750)
where Terminal unit size refers to the total rated CFM of
the terminal unit
This sliding window allows the control to be much tighter on the
smaller terminal units than can be achieved on the larger terminal
units as far as CFM readings. On a large terminal unit, 25 CFM
may not be noticeable, but on a small terminal unit, 25 CFM may
be more than the minimum airfl ow setting for the space.
If the pressure sensor is disconnected or fails on a pressure in-
dependent terminal unit, the controller automatically reverts to
pressure dependent operation and generates an alarm to alert the
user that a failure has occurred.
On either type of terminal unit, a space sensor failure will force
the damper to position itself to the 50% of the maximum damper
position setpoint, and it will not change until the sensor is repaired
or replaced.