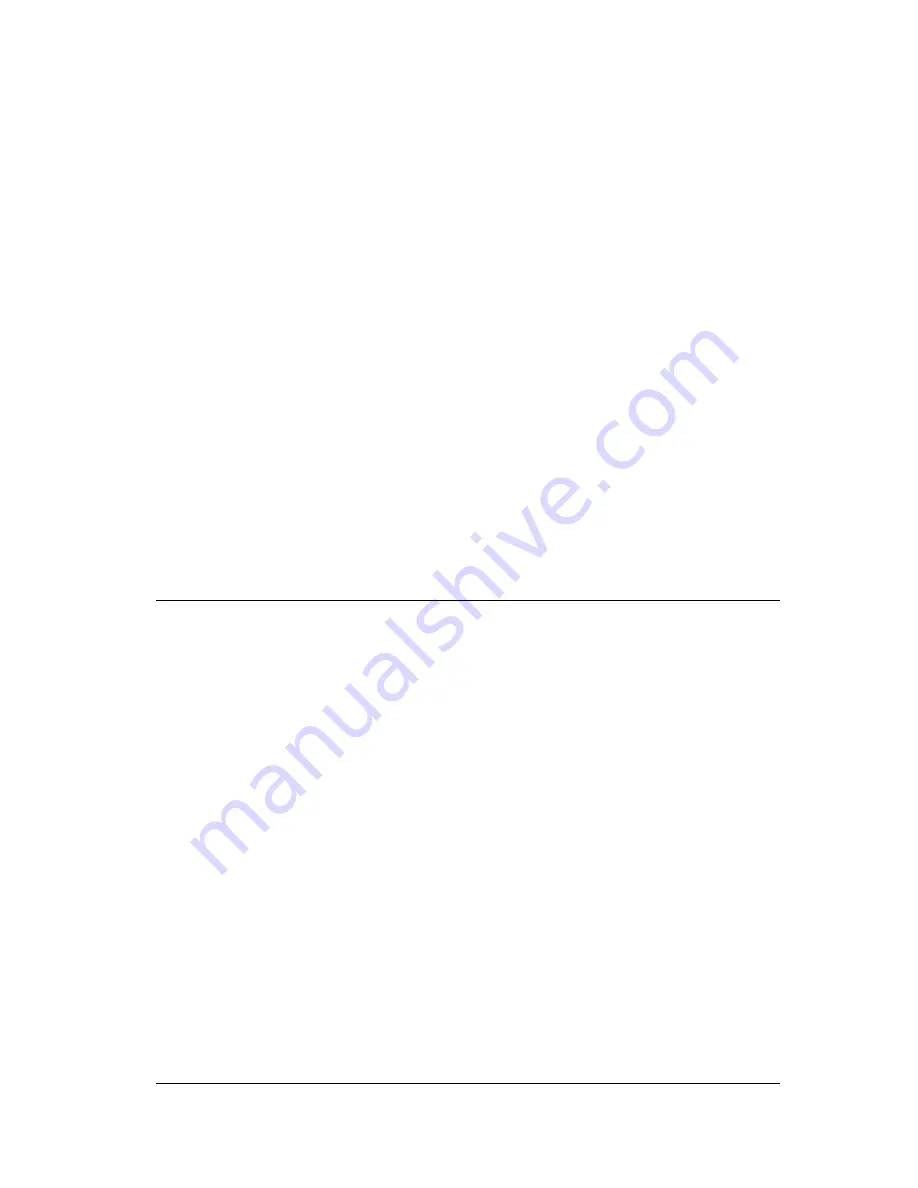
17
H I - F I C A R T R I D G E A L I G N I N G T O O L S
Tools required are an alignment gauge, a tracking force gauge, a FLAT record, a screwdriver or Allen keys of the right
size (usually 2mm), a good light may also be helpful. Small needle-nose pliers and a magnifying glass all help. It also helps
to have the hi-fi news test record. Treat the arm with care as some parts are fragile. To this end ensure that tightening of
any bolts is carried out gently and without causing undue strain.
C H E C K H I - F I C A R T R I D G E C L I P C O N N E C T I O N S A N D M O U N T I N G
Tonearm wiring uses a standard color code for left channel (L) and right channel (R) and polarity. Coding is as follows:
White = L Hot, Blue = L Ground, Red = R Hot, and Green = R Ground. If the cartridge pins aren't color-coded the
same way, they will have letter identifications next to them. Make sure that the arm’s wires, wire clips, and solder joints
are in very good condition. At minimum, clean the contact between cartridge pins and wire clips by removing and
replacing each clip. Holding the clips with needle-nose pliers can make this easier, but be careful that you don’t strain the
wires where they join the clip. Check the clips for a proper fit on the cartridge pins, and adjust them if necessary.
"Proper" means snug but not tight. To check clip size, hold the cartridge tail-up close to the head wires, grasp a clip
firmly right behind its tubular part with the tweezers, line it up with the cartridge pin, and press. If it does not slide on
with moderate force, the clip needs opening-up. If it slides on easily but flops around when attached, it needs tightening.
Sizing is the operation most likely to detach a clip. The trick is to avoid bending the wire at its attachment point or
putting too much tension on it. To avoid either, always hold the clip with its wire slightly slack-looped behind it while
adjusting. For opening a clip, hold it firmly with the tweezers or needle-noses, right behind its tubular section, and press
the tip of the jeweler's screwdriver into the open end of its longitudinal slot until you see this widen very slightly. (Here's
where you'll probably need the headband magnifier or reading glasses.) You're dealing with thousandths of an inch here,
so a barely visible spreading may be all that's needed. Try it for fit, and repeat until it does. For tightening a clip, press a
toothpick inside it as far as it will go, then use the needle-nose pliers to gently squeeze together the sides of the clip near
its free end, while watching the slot for any change. (Attempting to squeeze a clip without the toothpick inside it will
flatten its sides.) Try it for size, and resqueeze if necessary until the fit is correct. When it is, close up the middle section of
the tube to match the end
Cartridge mounting screws (usually 2.5mm allen bolts) should be tight. Steel allen bolts are the best for mounting hi-fi
cartridges - aluminum or brass are OK but difficult to tighten up hard (as they should be).
S E T T I N G U P H I - F I C A R T R I D G E S
M O U N T I N G
Mount the hi-fi cartridge in the headshell if this is not done already. This is best done with the hi-fi cartridge stylus guard
in place but it may be necessary to remove it during at least one phase of the installation. If you do, replace it as soon as
possible. Be especially careful when the stylus guard is off, as many MC cartridges have a strong magnetic field at the
base of the cantilever. If this attracts the tip of a steel-bladed screwdriver, it can destroy the stylus - there is no hope of
resisting it. The best precaution is to keep the screwdriver well away from the cantilever, use a nonferrous screwdriver, or
keep the stylus guard on when you're using the screwdriver near it. The other main hazard is children so don’t forget to
warn prying fingers.
The headshell screws should be finger-tightened just enough that the cartridge cannot fall off but still loose enough that
the cartridge is easily moved around. Work whenever possible with the stylus’s safety cap in place. Set tracking force at
nominal, then do the tangency alignment procedures, then the azimuth. Do not deviate from this sequence as each step
affects the subsequent one — change the order and the setup will be wrong.
T R A C K I N G F O R C E
This adjustment is carried out on the counterbalance weight of the tonearm or spring dial if one is in place. At this point,
use your tracking force gauge and setting tracking force according to your cartridge instructions — final adjustment will
be done later by ear.
If you do not have a tracking force gauge, but the arm does have a calibrated counterweight, defeat the arm’s anti-skate
mechanism or set it to zero. Set the counterweight so the arm is level and balanced. Be very careful of the unprotected
stylus — you cannot do this with its safety cap in place. Once the arm is balanced, lock it in its cradle and, using the
calibrated counterweight, set the tracking force according to your cartridge’s recommended weight.