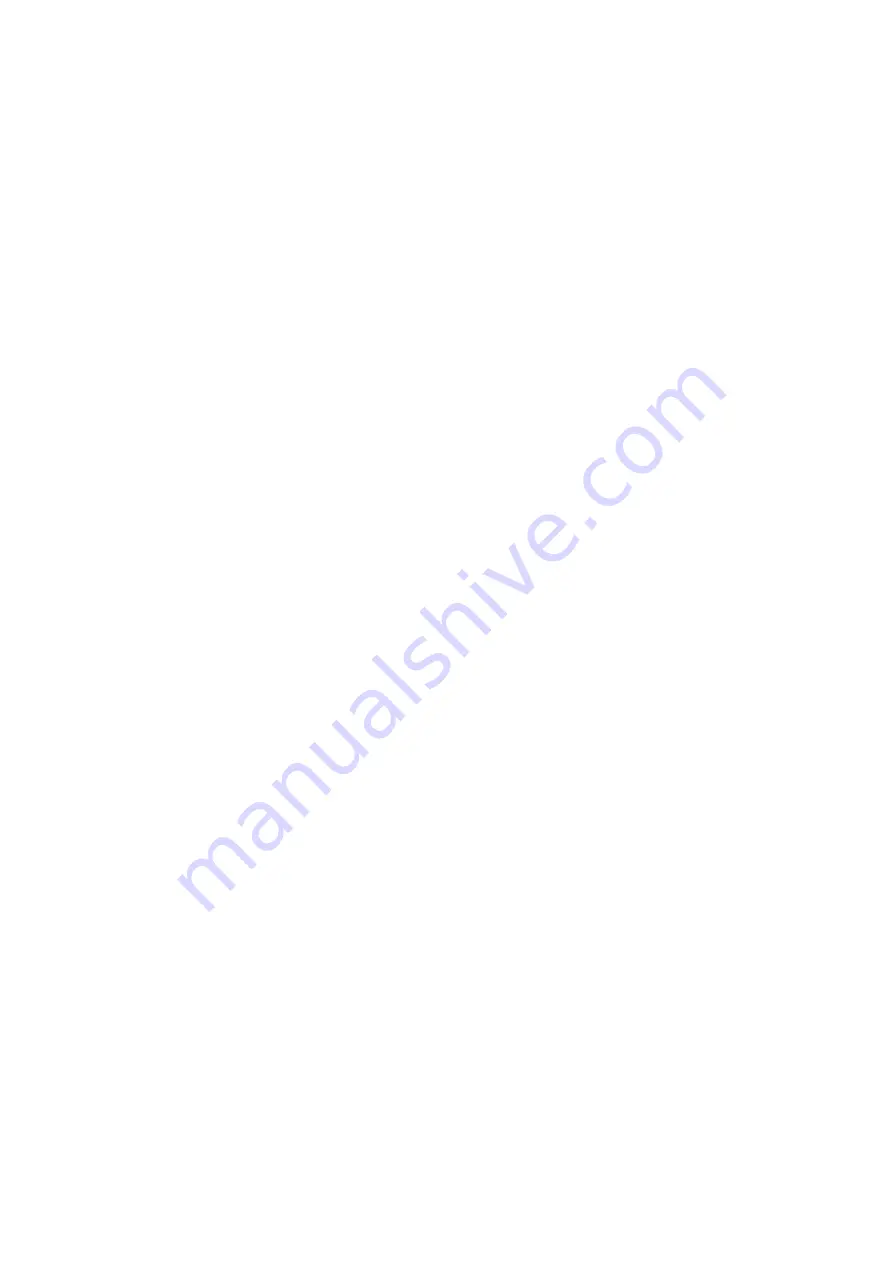
9
Excessive Motor Noise
The motor needs a run in time of around
2 - 4 days continuous running. They are
sometimes a little noisy to start with. Most
importantly you can “tune in” the motor to give
minimum noise by slackening off all 3 mounting
plate screws next to the pulley then tightening
one screw in turn. Find out which screw reduces
motor noise when lightly tightened and then
adjust the other two to give minimum noise.
Please note that by adjusting these screws
you effect the angle of the motor. If the belt
touches the flanges at the top or bottom of the
pulley then the motor is at too extreme an
angle and you will need to re-adjust the
bolts. The ideal is for a vertical pulley with
the lowest noise level. If you get a knocking
sound from the motor then slightly slacken
off the three screws holding the motor to the
top plate.
It may be necessary to use thread lock or similar
to stop the screws vibrating loose. If it continues
to be very noisy please get back to us and we
may check it out. However bear in mind that the
DC motor is never silent as a/c motors are - this
is because they rely on a higher grade of brush.
The other major potential source of noise
is the motor vibrating against it’s top plate
and causing it to resonate. The solution is
usually to slightly tighten the 3 small screws
holding on the motor. This adjustment is fairly
critical - if the 3 small screws are too tight
then the motor whispers, too slack and the
motor can vibrate against it’s top plate.
If you have checked the above and are still
having trouble please contact us making a
note of the serial number on the back of
the control box.
Example Fitting the Kit to an LP12
To fit the DC motor kit to the Linn is
straightforward by carrying out the following
steps. No drilling of the top-plate is required and
the modifications are easily reversible should you
ever wish to sell your Linn but retain the DC motor.
Unplug the deck from the mains supply for safety
reasons and before doing any work allow the
Valhulla capacitors to discharge for 45 minutes.
Do not remove the baseboard cover before this
period is over as there is danger of lethal electric
shock. You MUST also remove the mains plug
at this stage to avoid any possibility of someone
plugging it in at a later stage. You will not need the
Linn electronic power supply any more, so it can
either be detached entirely or simply left in place
for quick reversal of this modification. The LP12
will sound better if the Valhulla board is removed
entirely due to the additional resonance it inputs to
the plinth.
Unscrew the baseboard from the Linn - the
screws, which hold on the 4 rubber feet and 2
others, usually hold it on.
Disconnect the 4 wires leading to the Linn motor
(2 grey, 1 blue, 1 red) by slackening the screws
holding them at the terminal block.
Unscrew the 2 slotted pan head screws that
control the tilt of the Linn motor.
Unscrew the 2 black round headed Allen screws
that hold on the Linn Motor - you may need to