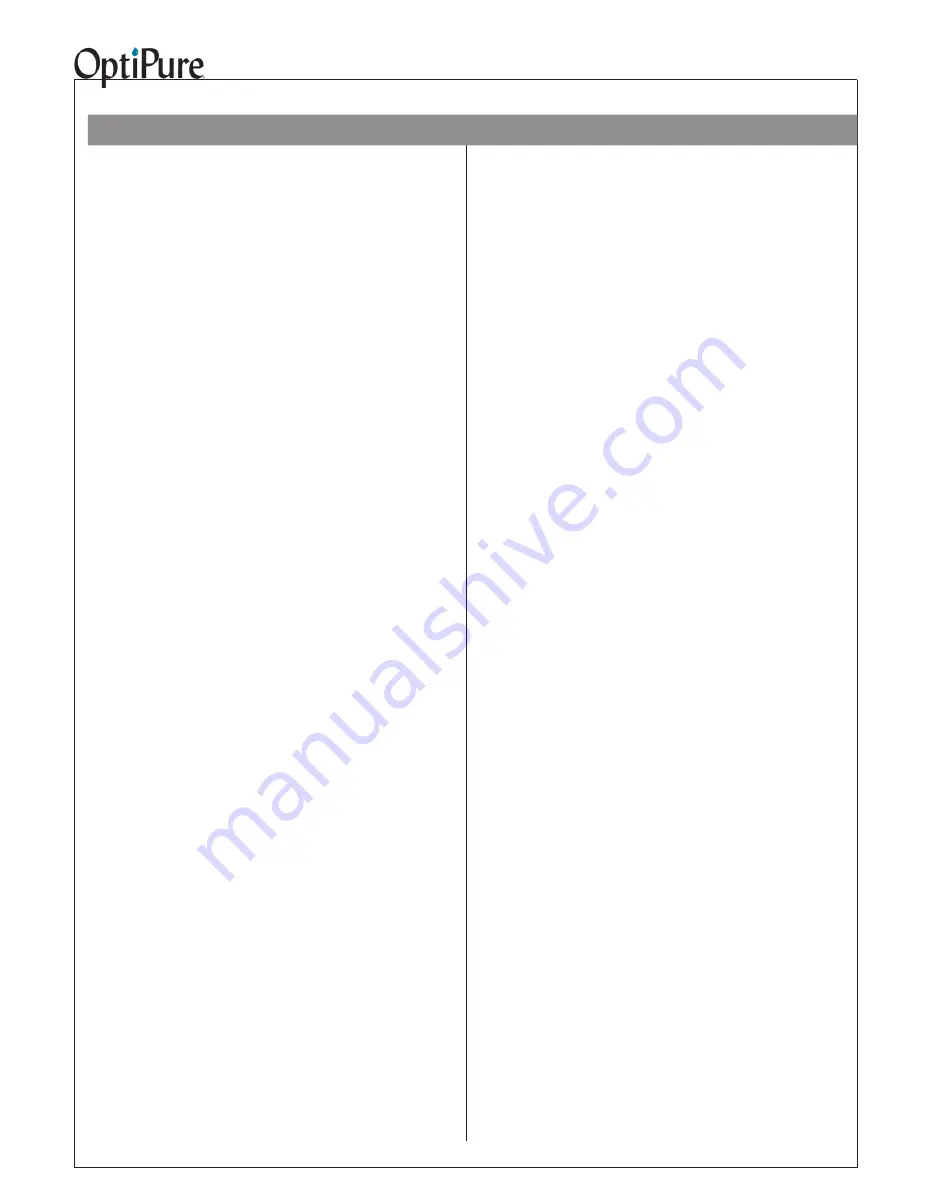
OP350 System Installation, Operation & Maintenance
4
Installation Requirements
This section and the next provide the water, electrical
and space requirements for the OP350.
Pay
special attention to the feed-water chemistry
requirements.
Operating a system on water supplies
outside of these parameters may lead to premature
membrane failure. This product is for commercial
use only and must be installed and maintained in
accordance with manufacturer’s guidelines and local
regulatory plumbing and electrical codes.
Operating parameters
Typical Membrane TDS* rejection:
97+%
Feed Temperature:
40 - 100° F (4 - 38° C)
Feed pressure:
50 - 80 psi
(3.4 - 5.9 bar) at 1 gpm
Production**
(
at 77°F, 60 psi
)
350 gals/day,
14.6 gals/hr, 0.24 gpm
Recovery:
up to 33%.
IMPORTANT NOTE:
The nominal production rate
is strictly dependent on feed water temperature and
pressure. Reduced temperature or pressure will
reduce production. For example: Operating pressure
of 30 psi will cut production by 50%. 48˚F feedwater
will cut production by 50%.
Location
The system should be installed indoors, in the
proximity of the equipment (within 25 feet) and
protected from the elements. Do not let the processor
or storage tank freeze or be exposed to rain or direct
sunlight.
Additional Optional Post-treatment
Treated water stored in a tank may absorb organic
compounds from the tank, which can affect water
taste and odor. If product water is for consumption, an
optional post-treatment filter, such as an OptiPure
FX or QT carbon filter, should be installed after the
tank. If used, it is best installed as close to the point of
use as possible. Other specialized post-treatment is
also available.
Feed water connection
An adequate flow and pressure of water to the unit is
essential for successful operation. Provide a dedicated
1/2” water line to the vicinity of the installation. Install
a full-flow ball valve and pressure gauge with 1/2”
female pipe thread (user supplied) for connection to
installation hardware provided with the system. A 1/2”
male pipe thread x 3/8” push-to-connect adapter is
included in the installation kit.
Drain
A drain should be located within 5 feet of the location
of the unit. Drain must allow a minimum flow of 2
gallons per minute. Compliance with most local
plumbing codes requires installation of an approved air
gap in the drain line. The drain connection should be
accessible for system set-up and service.
Electrical requirements
A power source with two outlets should be located
within 5 feet of the location of the unit.
Processor
120V, 60Hz 6 Watts
RP Pump
120V 60Hz 2 Amps
Feed-water chemistry
Feed TDS
Up to 1200 ppm
Feed pH
6 - 10
Hardness
28 grains or less
Free chlorine
<2 mg/l
Iron (Fe)
0.1 mg/l max.
Turbidity
<0.05 NTU
Manganese
0.05 mg/l max.
Hydrogen sulfide
0.0 mg/l
A water analysis must be conducted before installing
the system, or the information requested above can
be obtained from your local water utility. If your water
analysis shows that any of these parameters are not
within range, additional pretreatment and/or higher
frequency of maintenance may be required. Contact
your OptiPure distributor for assistance. The presence
of silica or flocculants such as alum or cationic
polymers in the feedwater may cause membrane
fouling and may require special chemical pretreatment
or periodic membrane cleaning. Please note that
membrane failure due to fouling is not covered by the
warranty.
Storage Tank
The tank must be located within 10 feet of the water
processor unit. The floor beneath the storage tank
should be smooth, clean and free of sharp objects that
could puncture the bottom of the tank.
Note: The tank
is atmospheric, with a sub-micron, hydrophobic air
breather filter.
Optimized Water Lines to Equipment
Tubing, piping and associated fittings connecting
Optimized water lines to equipment shoud be food
grade material that meets NSF Std 51 or 61 with a
minimum pressure rating of 75 PSI. Optimized water
may react with most metal piping imparting a bad
taste. Plastic pipe or reinforced opaque beverage
tubing are acceptable choices for Optimized water
distribution. The larger inside diameter tubing or hose,
the better to minimize pressure drop.
*TDS (total dissolved solids) create conductivity in water and are
expressed in ppm or mg/l (parts per million or milligram per liter).
**Nominal production @ 77°F (25°C) @ 500 ppm based on a 24
hr day. Actual production will vary based on variations in water
temperature, pressure, and TDS.