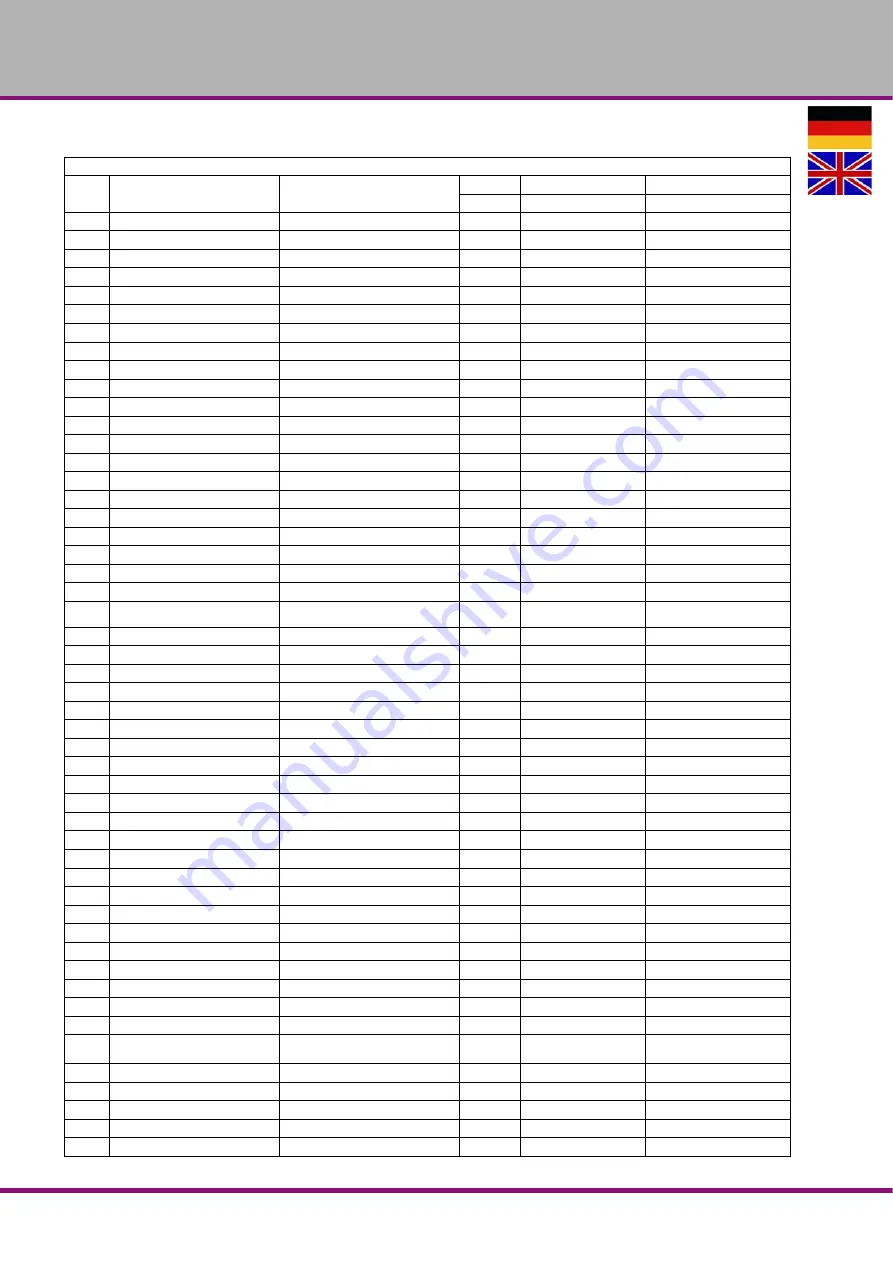
OPTIMUM
M A S C H I N E N - G E R M A N Y
Ersatzteile - Spare parts
Version 1.0.2 2017-04-11
36
Originalbetriebsanleitung
RD3
DE
Ersatzteilliste - Spare part list
Pos.
Bezeichnung
Designation
Menge
Grösse
Artikelnummer
Qty.
Size
Item no.
1
Schwenkfuß
Swivel Base
1
033350351
2
Säulenfuß
Column Base
1
033350352
3
Zahnstange
Rack
1
033350353
6
Federscheibe
Spring Washer
6
M12
7
Sechskant schraube
Hex. Head Screw
6
M12x50
8
Radial Arm
Radial Arm
1
033350358
9
Zahnstange Ausleger
Movable Rack
1
033350359
10
Sechskant schraube
Hex. Socket Head Screw
4
M6x15
11
Skala
Scale
1
0333503511
12
Niet
Rivet
2
Ø2
13
Unterlegscheibe
Washer
2
Ø10.5xØ27x3t
0333503513
14
Buchse Klemmgriff
Lock Handle Bushing
2
0333503514
15
Klemmgriff
Lock Handle
2
0333503515
16
Stahlband
Band Steel
1
0333503516
17
Senkkopfschraube
Flat Round Head Screw
2
M5x8
18
Griff für den Ausleger
Knob Set
1
0333503518
19
Flanschring Säule
Column Flange Ring
1
0333503519
20
Kopfplatte Säule
Column Head Set
1
032352020
22
Schlauchtülle
Hose Bushing
1
0333503522
23
Schneckenwelle
Worm Shaft
1
0333503523
24
Buchse
Bushing
1
0333503524
25
Halterungsbaugruppe Höhenver-
stellung
Head Raise Bracket Assembly
1
0333503525
26
Sechskant schraube
Hex. Socket Head Screw
4
M6x25
27
Kurbel Auf / Ab
Up-Down crank
1
0333503527
29
Knopf
Knob
1
0333503529
30
Bohrkopfgehäuse
Head Body
1
0333503530
31
Pinolenkegel
Spindle Taper Sleeve
1
0333503531
32
Sicherungsring
C-Retaining ring
1
Ø3xØ80
0333503532
33
Äußere Lagerplatte
Outer Bearing Plate
1
Ø105xØ66x2.5t
0333503533
34
Senkkopfschraube
Cross Round Head Screw
3
M6x10L
35
Kappe
Cap
1
032353535
36
Sechskant schraube
Hex. Socket Head Screw
4
M6x20L
37
Keilriemenscheibe Spindel
Spindle Pulley
1
0333503537
38
Sicherungsmutter Spindel
Spindle Locknut
1
0333503538
39
Abdeckung Hauptwelle
Main Shaft Cover
1
0333503539
40
Senkkopfschraube
Cross Round Head Screw
4
M5x10L
41
Anzugsstange
Draw bar
1
MT12xP1.75
0333503541
42
Abdeckung Hauptwelle
Main Shaft Cover
1
0333503542
43
Keilriemenabdeckung
Belt Cover
1
0333503543
44
Seitenplatte (links)
Side Plate (left)
1
0333503544
45
Seitenplatte (rechts)
Side Plate (Right)
1
0333503545
46
Senkkopfschraube
Cross Round Head Screw
6
M5x8L
47
Bezeichnungsschild
Name Plate
1
48
Baugruppe Riemenscheibe Motor
Motor Pulley Set
1
0333503548
50
Keilriemen
Belt
1
13A0840C
AX-32
032350350
51
Motorbefestigungsplatte
Motor Mount Plate
1
0333503551
52
Sechskant schraube
Hex. Socket Head Screw
1
M10x20L
53
Knopf
Knob
1
0333503553
54
Unterlegscheibe
Washer
1
Ø10.5xØ27x3t
0333503554
55
Sechskant schraube
Hex. Socket Head Screw
1
M10x40L