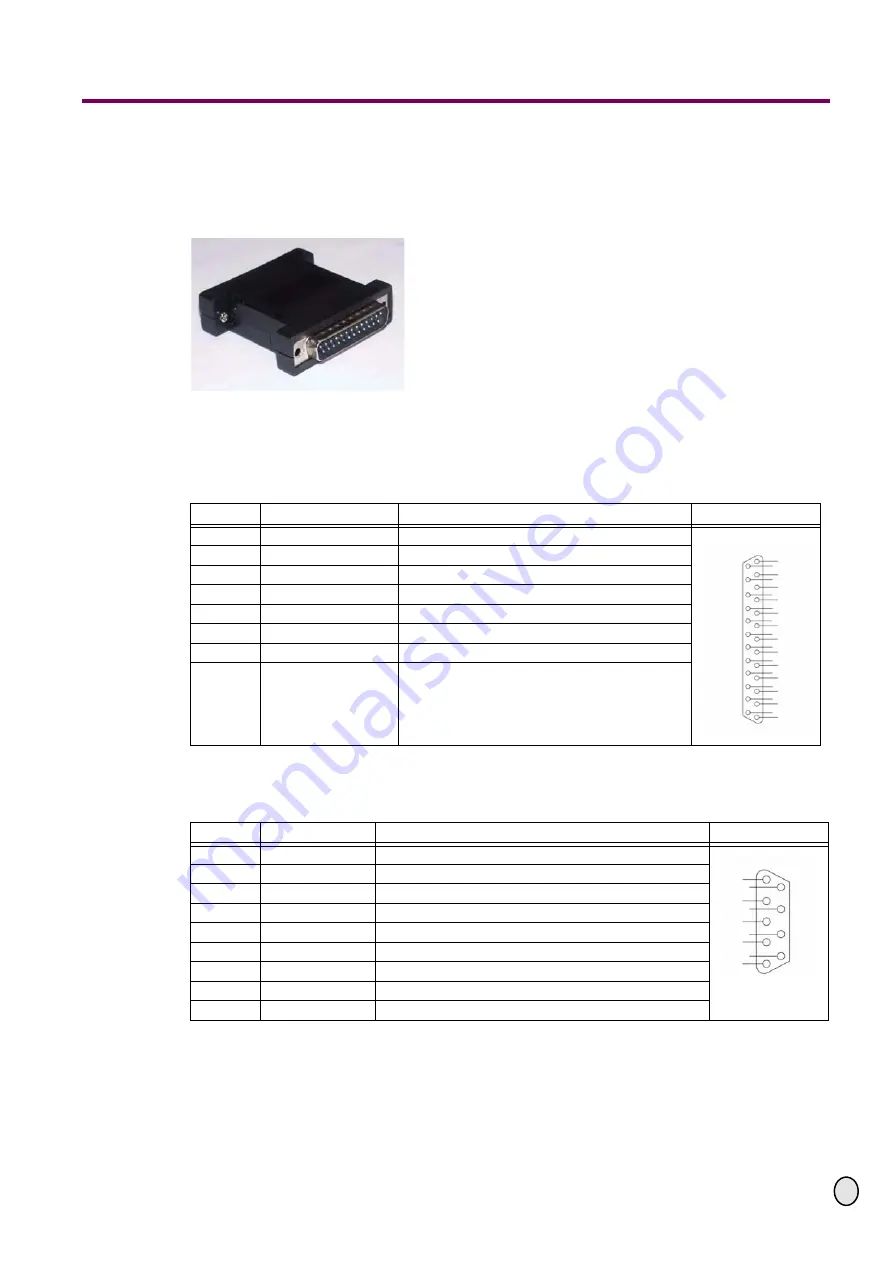
Description of the connection
OPTIMUM
M A S C H I N E N - G E R M A N Y
29 / 11 / 2006
Page
6
Description of the connection CNC Controller III and VI ; Version 2.0.1
©
20
06
GB
6.1
Signal configuration on the parallel port
The CNC controller III and VI need to be supplied with separate direction and cycle signals.
When using the HSE software such as PCturn DOS PCturn for Windows you have to connect
the adapter plug wihich is included in the delivery volume on the PC port.
Fig.6-1: LPT port adapter plug
6.1.1
Assignment of the signals at the parallel port, CNC controller III (port / PC)
The following assignment of signals is required on the parallel port.
6.1.2
Assignment of signals at the port reference switch (Ref.switch)
The following signal configuration is used on the parallel port.
Pin No
Application
Description
DB 25 male
2
Direction X-axis
Direction signal to control the axis
3
Cycle X
Cycle signal to control the step motor
4
Direction Y
Direction signal to control the axis
5
Cycle Y
Cycle signal to control the step motor
6
Direction Z
Direction signal to control the axis
7
Cycle Z
Cycle signal to control the step motor
8 - 24
Free
Not assigned
25
OV DC, earthing
2
3
4
5
6
7
8
9
10
11
12
13
14
15
16
17
18
19
20
21
22
23
24
25
1
Pin No
Application
Description
DB9 female
1
X1
Machine point of origin port 1 X-axis
2
Y1
Machine point of origin port 1 Y-axis
3
Z1
Machine point of origin port 1 Z-axis
4
Round table
Point of origin round table port 1
5
+12V DC
6
X2
Machine point of origin port 2 X-axis
7
Y2
Machine point of origin port 2 Y-axis
8
Z2
Machine point of origin port 2 Z-axis
9
0V DC
5
4
3
2
9
8
7
6
1