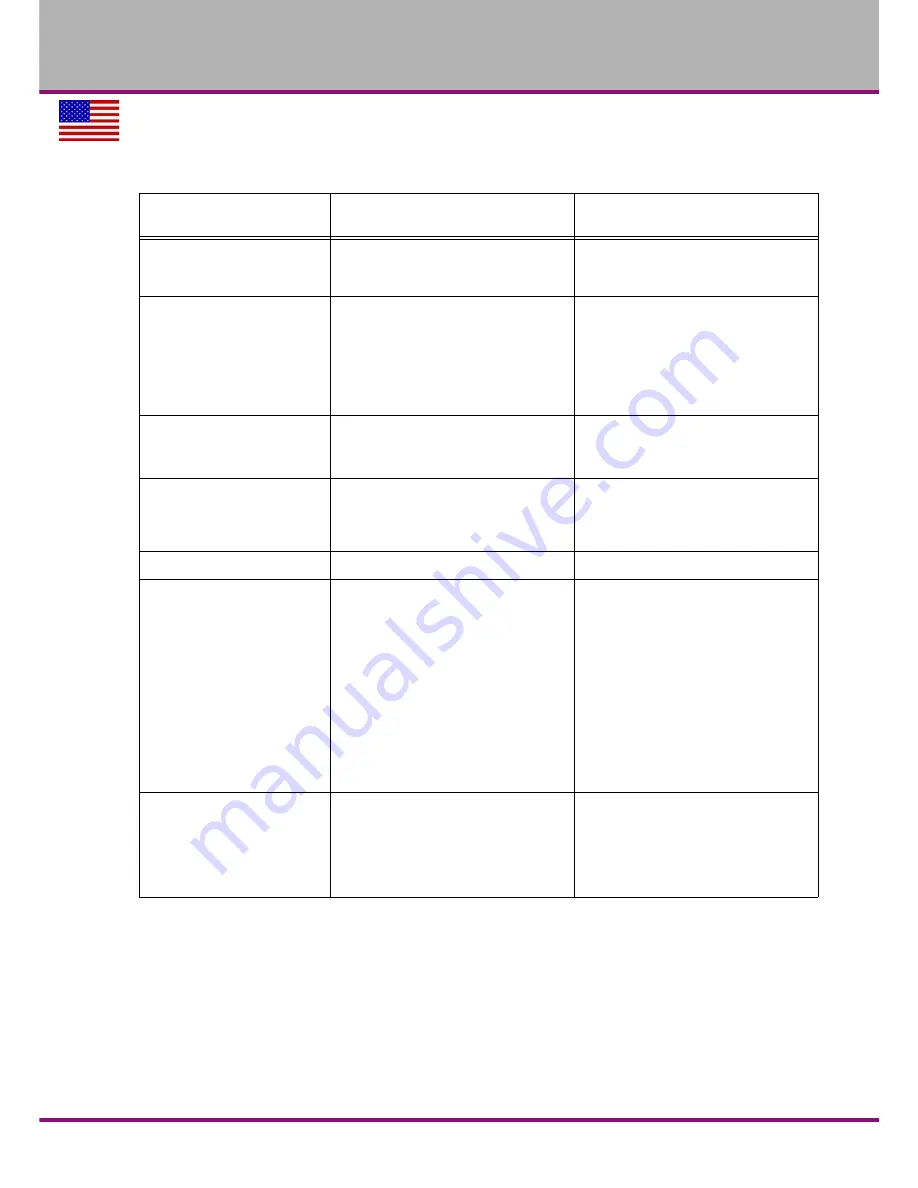
OPTIMUM
M A S C H I N E N - G E R M A N Y
Version 3.1.8 dated 2015-1-27
Page 49
Original operating instructions
BF20V
US
7
Troubleshooting
7.1
Troubleshooting the mill drill
Malfunction
Cause/
possible consequences
Solution
The mill drill does not start
•
Start sequence not followed.
•
"Switching on the mill drill“ on
page 25
•
Have it checked by authorised staff.
Tool "burnt“.
•
Incorrect speed.
•
The chips have not been removed
from the bore hole.
•
Tool blunt.
•
Operating without cooling agent.
•
Select another speed, feed too high.
•
Retract tool more often
•
Sharpen and replace tool.
•
Use coolant.
Impossible to insert holding
taper into the spindle
sleeve.
•
Remove any dirt, grease or oil from
the internal conical surface of the
spindle sleeve or the holding taper.
•
Clean surfaces well.
Keep surfaces free of grease.
Taper cannot be removed
•
Optional MT3 taper seat shrunk on
morse cone.
•
Have the machine heat-up at highest
speed for about two minutes and
then try again to disassemble the
taper.
Motor does not start
•
Defective fuse
•
Have it checked by authorised staff.
Working spindle rattling on
rough workpiece surface
•
Climb milling machining not possible
under the current operating condi-
tions.
•
Clamping lever of the movement
axes not tightened.
•
Loose collet chuck, loose drill chuck,
loose draw-in rod.
•
Tool blunt.
•
Workpiece is not fixed.
•
Excessive slack in bearing.
•
Working spindle goes up and down.
•
Perform conventional milling.
•
Tighten clamping lever
•
Check, retighten.
•
Sharpen or replace tool
•
Secure the workpiece properly.
•
Readjust bearing slack or replace
bearing.
•
Readjust bearing slack or replace
bearing.
Fine feed of spindle sleeve
does not work
•
Fine feed is not correctly activated
•
Clutch of the fine feed does not
engage, is dirty, smeared, worn or
defective
•
"Manual spindle feed with the
fine feed“ on page 30
•
Clean, replace