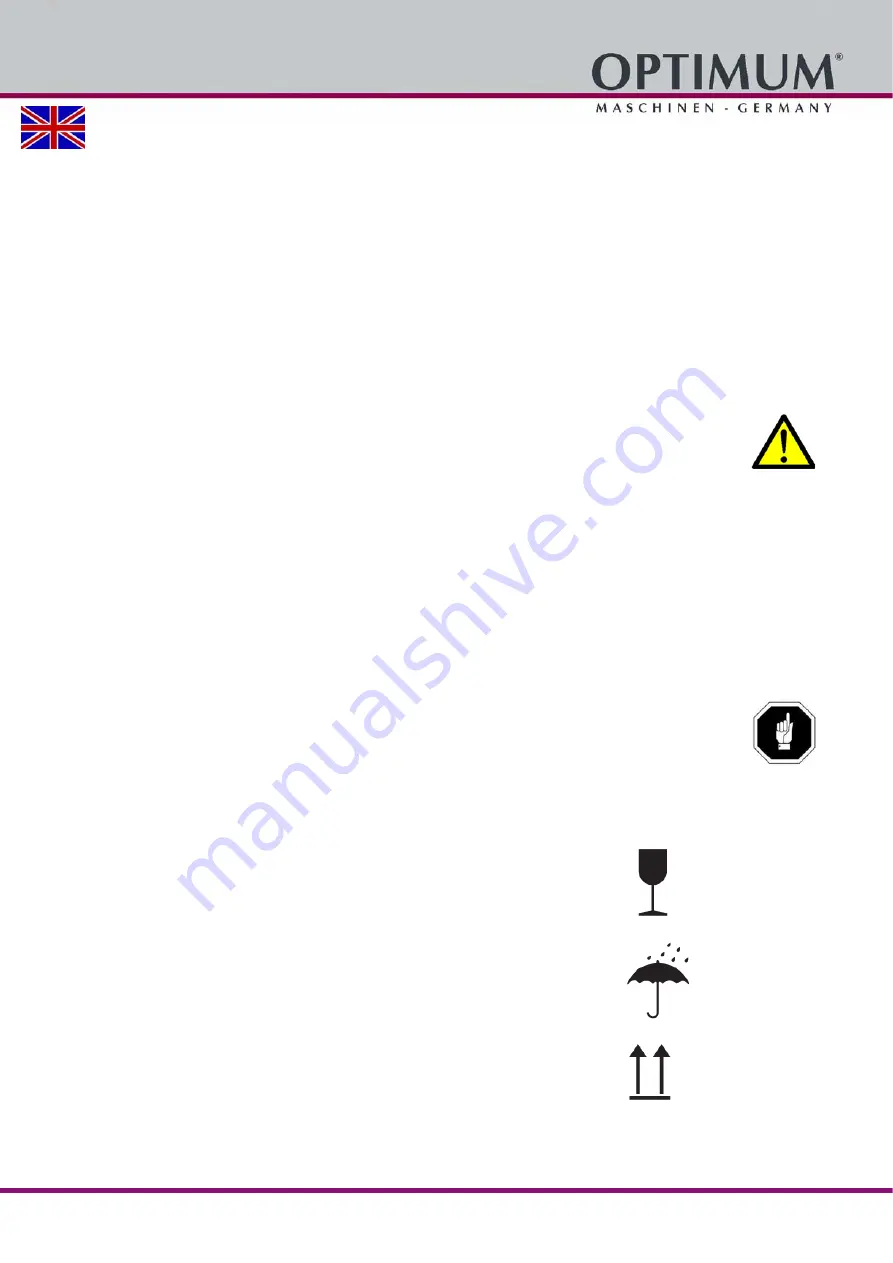
Appendix
Version 1.0 - 2020-09-04
33
Translation of original instructions
DX17E
EN
D
X
17E
_GB_
6.
fm
Neither are the following items covered by liability or warranty claims:
- Wearing parts and components which are subject to normal and intended wear, such as
V-belts, ball bearings, lighting, filters, seals, etc.
- Non reproducible software errors
Any services, which OPTIMUM GmbH or one of its agents performs in order to fulfil any
additional warranty are neither an acceptance of the defects nor an acceptance of its obli-
gation to compensate. These services neither delay nor interrupt the warranty period.
The court of jurisdiction for legal disputes between businessmen is Bamberg.
If any of the aforementioned agreements is totally or partially inoperative and/or invalid, a
provision which nearest approaches the intent of the guarantor and remains within the
framework of the limits of liability and warranty which are specified by this contract is
deemed agreed.
6.3.1
Decommissioning
CAUTION!
Used devices need to be decommissioned in a professional way in order to avoid later
misuses and endangerment of the environment or persons.
Unplug the power cord.
Cut the connection cable.
Remove all operating materials from the used device which are harmful to the envi-
ronment.
If applicable remove batteries and accumulators.
Disassemble the machine if required into easy-to-handle and reusable assemblies
and component parts.
Dispose of machine components and operating fluids using the intended disposal
methods.
6.4
Storage
ATTENTION!
Incorrect and improper storage might result in damage or destruction of electrical and
mechanical machine components.
Store packed and unpacked parts only under the intended environmental conditions.
Follow the instructions and information on the transport box.
Fragile goods (Goods require careful handling)
Protect against moisture and humid environment
Prescribed position of the packing case (Marking of the top surface -
arrows pointing to the top)