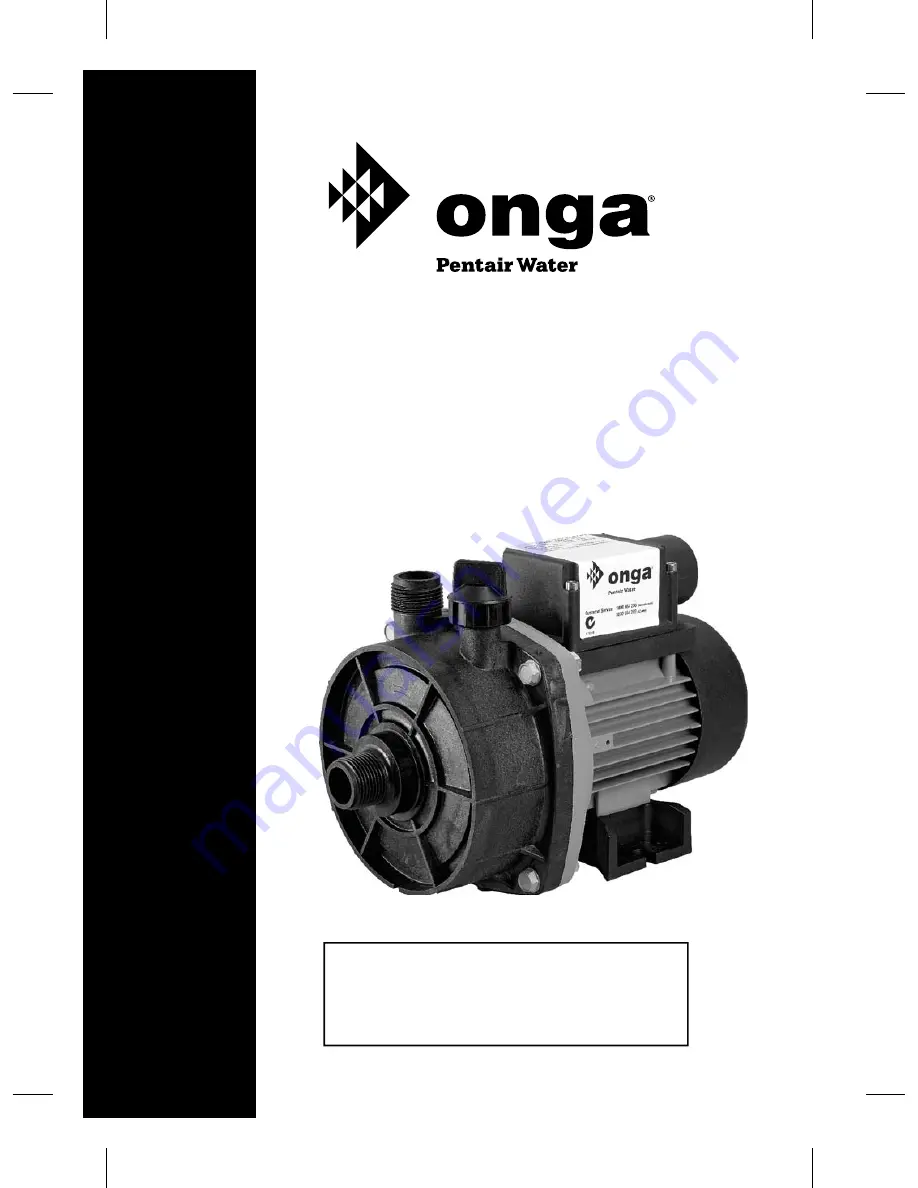
1
400 SERIES
HI-FLO CENTRIFUGAL PUMPS
High head water transfer, circulation duty
for hydroponic greenhouses, tank filling
OWNER`S MANU
AL
Should
the
installer
or
owner
be
unfamiliar
with
the
correct
installation
or
operation
of
this
type
of
equipment,
contact
the
distributor
or
manufacturer
for correct
advice
before
proceeding
with
installation
or operation
of
the
product
L100100_400Series_OM
Wednesday, 13 March 2013 9:13:38 AM