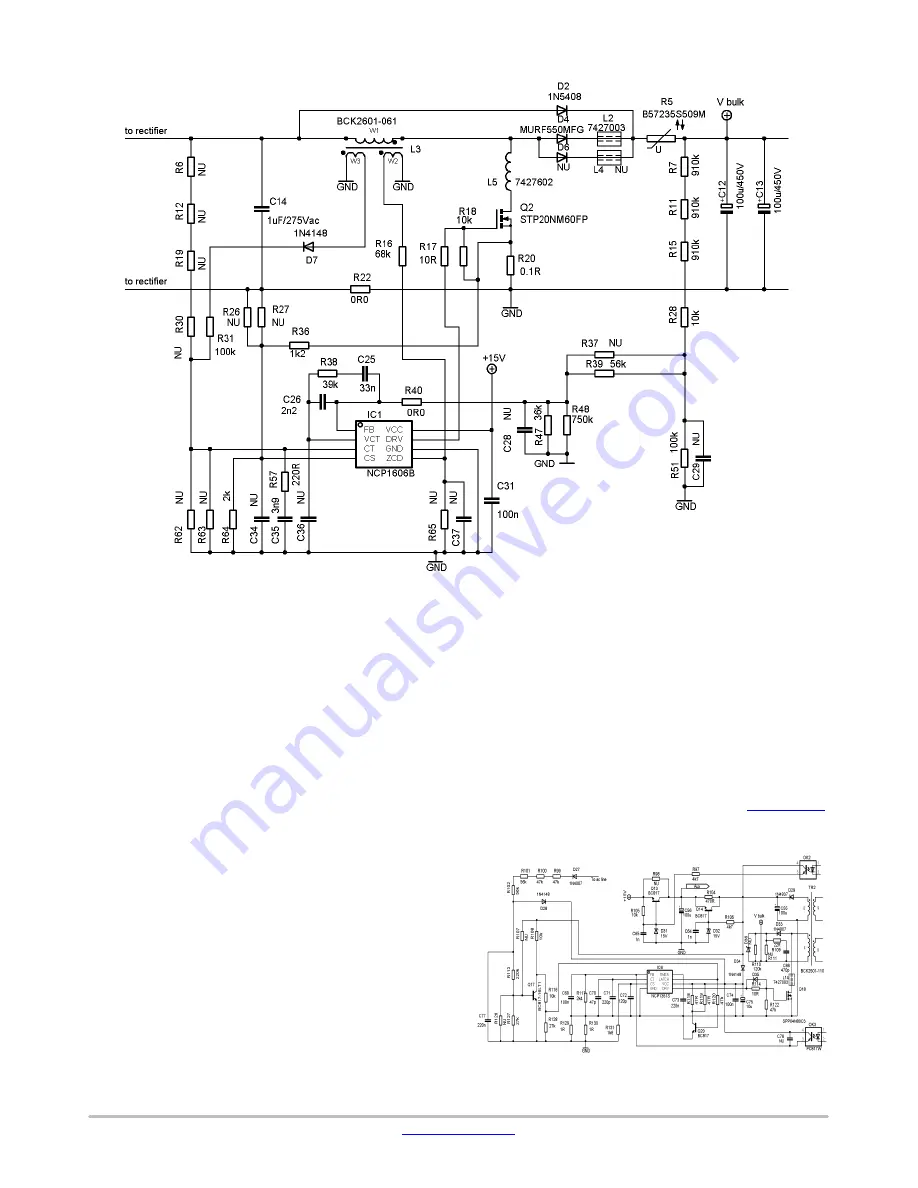
AND8344/D
4
Figure 3. Schematic of the PFC Stage
The NCP1606B boost PFC controller is used in this
application. This controller operates in critical conduction
mode. The printed circuit board (PCB) is compatible with
some other ON Semiconductor PFC controllers (e.g.
MC33262, NCP1601 or NCP1653). The input voltage
passes through an EMI filter (Figure 2), which protects the
distribution network against noise generated by the SMPS.
The EMI filter is created by capacitors CY1, CY2, C44, C63
and current compensated chokes L9 and L12 (L10 and L11
are options for using chokes in a different package). Varistor
R48 protects the SMPS against surges passed from the
mains. Filtered ac voltage is rectified by a four-diode
rectifier and connected to capacitor C14, which filters high
frequency peaks created in the PFC stage (Figure 3). If
MOSFET Q2 is turned on, energy is stored in coil L2. Once
MOSFET Q2 is turned off, the energy stored in coil L2 is
added to the rectified voltage on C14 and the bulk capacitors
are charged through diode D4. This voltage is divided by
resistors R7, R11, R18, R28, R51, R38, R46, and R47 and
is connected to the FB pin of the PFC in order to set the
regulation level. The current flowing through PFC coil L2
is sensed by R20 and ultimately the CS pin of the PFC
controller using resistor divider R35 and R64. The IC
monitors coil current during every switching cycle and if it
exceeds the safety level, it immediately turns off the
MOSFET. Resistor R37 and capacitors C26 and C27 create
a compensation network. The transient response depends on
the compensation network. Auxiliary winding W2 of the L2
coil provides information through resistor R15 to the PFC
controller about demagnetization of the coil. Thanks to this
monitoring, it is possible to turn on the switcher after full
demagnetization of the coil. This enables the use of a diode
with higher t
rr
, and it is good from an EMI point of view.
Diode D7 and resistor R30 together with W3 of the L2 help
to lower on time if the input voltage reaches the peak value.
For detailed information on how the PFC stage works and
how to design it, please read Application Note
Standby Power Supply
Figure 4. The SMPS Primary Side Schematic
Summary of Contents for NCP1351B
Page 19: ...AND8344 D www onsemi com 19 Figure 47 Schematic of the SMPS...
Page 20: ...AND8344 D www onsemi com 20 Figure 48 Bottom Side of the PCB...
Page 21: ...AND8344 D www onsemi com 21 Figure 49 Bottom Labels...
Page 22: ...AND8344 D www onsemi com 22 Figure 50 Top Labels...
Page 24: ...AND8344 D www onsemi com 24 Figure 52 Photo of the Demoboard with Heatsinks Removed...
Page 25: ...AND8344 D www onsemi com 25 Figure 53 Photo of the Demoboard Bottom Side...
Page 26: ...AND8344 D www onsemi com 26...
Page 27: ...AND8344 D www onsemi com 27...