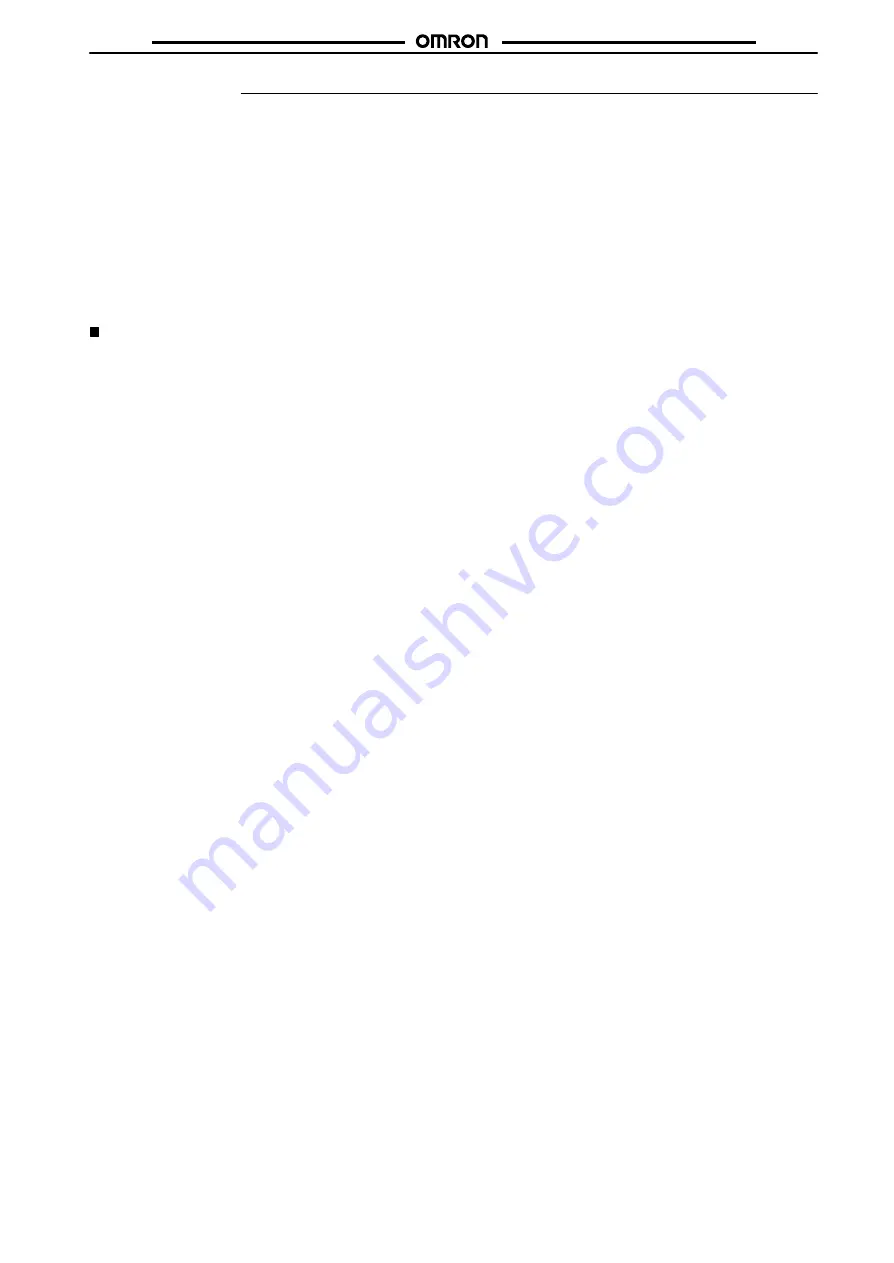
E3M-V
E3M-V
11
Precautions
Observe the following precautions to ensure safety.
•
Do not use the Sensor in locations subject to flammable or
explosive gases.
•
Do not use the Sensor in water or conductive solution.
•
Do not disassemble, repair, or modify the Sensor.
•
Use the Sensor under proper power supply specifications such
as the use of AC or DC power supply.
•
Do not apply any voltage or current exceeding the rated level.
•
Be careful with the power supply polarities and wire correctly.
•
Connect the loads correctly.
•
Do not short-circuit both ends of loads.
Correct Use
Installation
Power Reset Time
Since the E3M-V is ready to detect objects from 100 ms max. after
the E3M-V is turned ON, operate the remaining devices 100 ms af-
ter the Sensor is turned ON. If power is supplied to the E3M-V and
the load independently, be sure to turn on the E3M-V first.
Power OFF
The E3M-V may output a single pulse when the control power sup-
ply is turned OFF. If the E3M-V is connected to a timer or counter to
which power is supplied from an independent power supply, the
E3M-V will be more likely to output a single pulse when the control
power supply is turned OFF. Therefore, supply power to the timer or
counter from the same power supply for the E3M-V.
Power Supply Type
No full-wave or half-wave rectified power supplies can be con-
nected to the E3M-V.
Power Supply Connection
Be sure to ground the FG (frame ground) and G (ground) terminals if
a switching regulator is connected to the E3M-V, otherwise the
E3M-V may malfunction due to the switching noise of the switching
regulator.
Wiring
Cord
The cord can be extended up to 100 m provided that the thickness of
the cord is 0.3 mm
2
minimum.
Repeated Cable Bending
The cord must not be bent repeatedly.
High-tension Lines
The power supply lines of the Sensor must not be wired alongside
power lines or high-tension lines in the same conduit, otherwise the
Sensor may become damaged or malfunction due to induction
noise that may be generated from the power lines or high-tension
lines. Route the lines separately or in a single conduit.
Cord Pulling Force
Do not pull cords with pulling forces exceeding 50N.
Mounting
Screw Tightening
Make sure that the casing is tightened to a maximum torque of
1.2 N
S
m.
Mounting Direction
When Sensors are mounted to face each other, make sure to adjust
the optical axes so that the Sensors will not be mutually interfered.
Others
EEPROM Write Error
An EEPROM error may result if power supply to the Sensor fails or
the Sensor is influenced by static noise, in which case the threshold
level indicators will flash. Perform the teaching and threshold level
setting of the E3M-V again.
M12 Metal Connector
Make sure to connect or disconnect the metal connector after turn-
ing off the E3M-V.
Make sure to hold the connector cover when connecting or discon-
necting the metal connector.
Tighten the metal connector securely by hand. Do not use any tool,
such as pliers, otherwise the metal connector may be damaged.
If the metal connector is not tightened securely, the metal connector
may be disconnected by vibration and the proper degree of protec-
tion of the E3M-V may not be maintained.