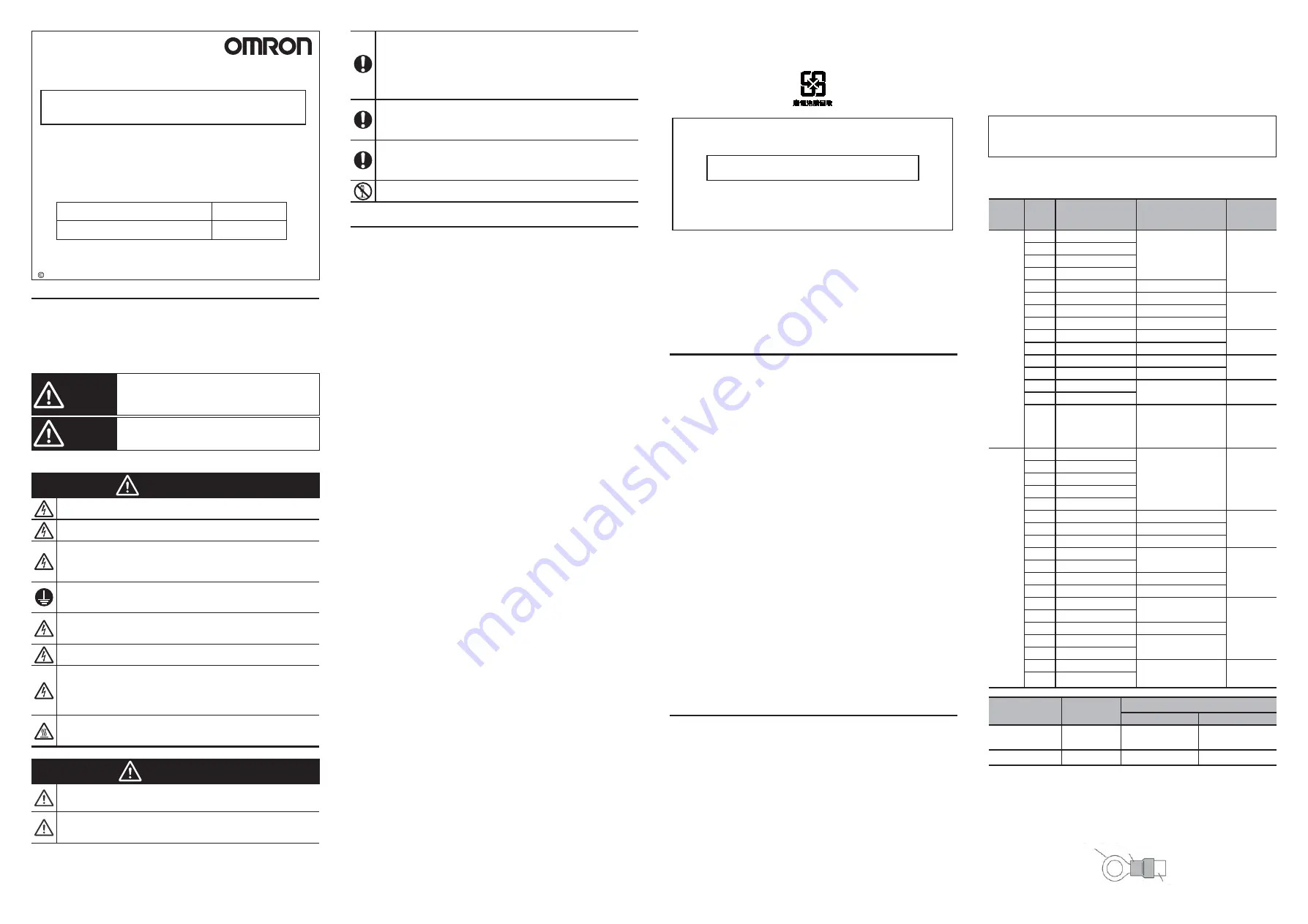
TYPE 3G3RX-
-V1
High-function General-purpose Inverter
NT205XG
Cat.No.
Manual Name
INSTRUCTION MANUAL
Thank you for purchasing 3G3RX, V1 type Inverter.
To ensure safe operation, please be sure to read the safety precautions
provided in this document along with all of the user manuals for the
inverter. Please be sure you are using the most recent versions of the
user manuals. Keep this instruction manual and all of the manuals in a
safe location and be sure that they are readily available to the final user
of the products.
OMRON Corporation
3G3RX User’s Manual
Safety Precautions
I578-E1
OMRON Corporation 2012 All Rights Reserved.
Indications and Meanings of Safety Information
Meanings of Signal Words
Alert Symbols in this Document
In this user’ s manual, the following precautions and signal words are
used to provide information to ensure the safe use of the 3G3RX, V1 type
Inverter.The information provided here is vital to safety. Strictly observe
the precautions provided.
WARNING
Indicates a potentially hazardous situation which,
if not avoided, may result in minor or moderate
injury or in property damage.
CAUTION
Indicates an imminently hazardous situation which,
if not avoided, is likely to result in serious injury or
may result in death. Additionally there may be severe
property damage.
Turn off the power supply and implement wiring correctly.
Not doing so may result in a serious injury due to an electric shock.
WARNING
Be sure to ground the unit. Not doing so may result in a serious injury
due to an electric shock or fire.
(200V class:type-D grounding, 400V class:type-C grounding)
Do not remove the terminal cover during the power supply and 10
minutes after the power shut off.
Doing so may result in a serious injury due to an electric shock.
Do not operate the Operator or switches with wet hands.
Doing so may result in a serious injury due to an electric shock.
Inspection of the Inverter must be conducted after the power supply has
been turned off. Not doing so may result in a serious injury due to an
electric shock.
The main power supply is not necessarily shut off even if the emergency
shut off function is activated.
Wiring work must be carried out only by qualified personnel.
Not doing so may result in a serious injury due to an electric shock.
Do not touch the Inverter fins, braking resistors and the motor, which
become too hot during the power supply and for some time after the
power shut off. Doing so may result in a burn.
Do not change wiring and slide switches (SW1), put on or take off
Operator and optional devices, replace cooling fans while the input
power is being supplied. Doing so may result in a serious injury due to
an electric shock.
CAUTION
The Inverter has high voltage parts inside which, if short-circuited, might
cause damage to itself or other property. Place covers on the openings
or take other precautions to make sure that no metal objects such as
cutting bits or lead wire scraps go inside when installing and wiring.
Be sure to use a specified type of braking resistor/regenerative braking
unit. In case of a braking resistor, install a thermal relay that monitors
the temperature of the resistor. Not doing so might result in a moderate
burn due to the heat generated in the braking resistor/regenerative
braking unit. Configure a sequence that enables the Inverter power to
turn off when unusual over heating is detected in the braking resistor/
regenerative braking unit.
Do not connect resistors to the terminals (+1, P/+2, N/-) directly. Doing
so might result in a small-scale fire, heat generation or damage to the
unit.
Do not dismantle, repair or modify the product.
Doing so may result in an injury.
Take safety precautions such as setting up a molded-case circuit breaker
(MCCB) that matches the Inverter capacity on the power supply side.
Not doing so might result in damage to property due to the short circuit
of the load.
Install a stop motion device to ensure safety. Not doing so might result in
a minor injury. (A holding brake is not a stop motion device designed to
ensure safety.)
Do not store or use the product in the following places.
Locations subject to direct sunlight.
Locations subject to ambient temperature exceeding the specifications.
Locations subject to relative humidity exceeding the specifications.
Locations subject to condensation due to severe temperature fluctuations.
Locations subject to corrosive or flammable gases.
Locations subject to exposure to combustibles.
Locations subject to dust (especially iron dust) or salts.
Locations subject to exposure to water, oil, or chemicals.
Locations subject to shock or vibration.
Installation and Storage
Precautions for Safe Use
Do not drop or apply strong impact on the product. Doing so may result
in damaged parts or malfunction.
Do not hold by the front cover and terminal cover, but hold by the fins
during transportation.
Confirm that the rated input voltage of the Inverter is the same as AC
power supply voltage.
Do not connect an AC power supply voltage to the control input/ output
terminals. Doing so may result in damage to the product.
Be sure to tighten the screws on the terminal block securely.
Wiring work must be done after installing the unit body.
Do not connect any load other than a three-phase inductive motor to
the U, V, and W output terminals.
Take sufficient shielding measures when using the product in the
following locations. Not doing so may result in damage to the product.
Locations subject to static electricity or other forms of noise.
Locations subject to strong magnetic fields.
Locations close to power lines.
If a parameter is set incorrectly when starting up, adjusting, maintaining,
or replacing, an unexpected operation may occur.
Perform the operation after enough confirmation.
When using DriveProgramming, confirm that the program data is
downloaded normally before starting the operation.
Operation and Adjustment
Maintenance and Inspection
Transporting, Installation, and Wiring
Be sure to confirm the permissible range of motors and machines before
operation because the inverter speed can be changed easily from low to
high.
Provide a separate holding brake if necessary.
If DriveProgramming stops during multi-function output, the output status
is held. Take safety precautions such as stopping peripheral devices.
If the clock command is used in DriveProgramming, an unexpected
operation may occur due to weak battery or removal of the LCD digital
operator.
Take measures such as detecting a weak battery or removal of the LCD
digital operator (the clock data detects the initial setting and all zero),
stopping the Inverter or programs.
Be sure to confirm safety before conducting maintenance, inspection or
parts replacement.
The capacitor service life is influenced by the ambient temperature.
Refer to "Product Life Curve" described in the manual. When a capacitor
reaches the end of its service life and does not work as the product, you
need to replace the capacitor.
When disposing of LCD digital operators and wasted batteries, follow
the applicable ordinances of your local government.
When disposing of the battery, insulate it using tape.
The following display must be indicated when products using lithium
primary batteries (with more than 6 ppb of perchlorate) are transport to
or through the State of California, USA.
Perchlorate Material - special handling may apply.
See www.dtsc.ca.gov/hazardouswaste/perchlorate
The 3G3AX-OP05 has the lithium primary battery (with more than 6 ppb
of perchlorate).Label or mark the above display on the exterior of all
outer shipping packages of your products when exporting your products
which the 3G3AX-OP05 are installed to the State of California, USA.
Do not short + and -, charge, disassemble, heat, put into the fire, or
apply strong impact on the battery. The battery may leak, explode,
produce heat or fire. Never use the battery which was applied strong
impact due to such as fall on the floor, it may leak.
UL standards establish that the battery shall be replaced by an expert
engineer.
The expert engineer must be in charge of the replacement and also
replace the battery according to the method described in this manual.
When the display of LCD digital operator can not be recognized due to
the service life, replace the LCD digital operator.
Precautions for Safe Use
Installation
Restart Selection Function
Deceleration Stop Function
Operation Stop Command
Maintenance and Parts Replacement
Product Disposal
Mount the product vertically on a wall the product’ s longer sides upright.
The material of the wall has to be noninflammable such as a metal plate.
Do not come close to the machine when using the Restart Selection
function (b001, b008) because the machine may abruptly start when
stopped by an alarm.
Be sure to confirm the RUN signal is turned off before resetting the
alarm because the machine may abruptly start.
Do not come close to the machine when selecting reset in the
Deceleration Stop Function (b050) because the machine may abruptly
start after the power is turned on.
Provide a separate emergency stop switch because the STOP Key on
the Operator is valid only when function settings are performed.
When checking a signal during the power supply and the voltage is
erroneously applied to the control input terminals, the motor may start
abruptly. Be sure to confirm safety before checking a signal.
Inverters contain components and will operate properly only when each
component operates normally. Some of the electrical components
require maintenance depending on application conditions.
Periodic inspection and replacement are necessary to ensure proper
long-term operation of Inverters. (Quoted from The Recommendation for
Periodic Maintenance of a General-purpose Inverter published by JEMA.)
When a cooling fan reaches the end of its service life, replace it.
Comply with the local ordinance and regulations when disposing of the
product.
UL Cautions
The warnings and instructions in this section summarize the procedures
necessary to ensure an inverter installation complies with Underwriters
Laboratories guidelines.
These devices are open type AC Inverters with three phase input and
three phase output. They are intended to be used in an enclosure. They
are used to provide both an adjustable voltage and adjustable frequency to
the AC motor. The inverter automatically maintains the required voltage-Hz
ration allowing the capability through the motor speed range.
Use 60/75°C Cu wire only. For models 3G3RX-V1 series except for
models 3G3RX-A4055-V1, 3G3RX-A4075, 3G3RX-A4110-V1.
Use 75°C Cu wire only. For models 3G3RX-V1 series for
3G3RX-A4055-V1, 3G3RX-A4075, 3G3RX-A4110-V1.
Suitable for use on a circuit capable of delivering not more than 100k rms
symmetrical amperes, 240 V maximum. (For models: 200 V class)
Suitable for use on a circuit capable of delivering not more than 100k rms
symmetrical amperes, 480 V maximum. (For models: 400 V class)
Install device in pollution degree 2 environment.
Maximum Surrounding Air Temperature 50°C (VT rating is 40°C).
Caution -Risk of Electric Shock- Capacitor discharge time is at least 10
minutes.
Solid state motor overload protection reacts with max. 120% of FLA.
Integral solid state short circuit protection dose not provide branch circuit
protection.
Branch circuit protection must be provided in accordance with the NEC
and any additional local codes.
Motor over temperature protection is not provided by the drive.
Terminal Tightening Torque and Wire Size
The wire size range and tightening torque for field wiring terminals are
presented in the tables below.
Input
Voltage
Motor
Output
(kW)
Inverter Model
3G3RX-
Power Terminal
Wiring Size Range
(AWG)
Torque
(N·m)
0.4
0.75
A2004-V1
A2007-V1
1.5
A2015-V1
2.2
A2022-V1
3.7
A2037-V1
350 kcmil (Prepared
wire only) or Parallel
of 2/0 (Prepared wire
only)
14(Stranded only)
10(Stranded only)
5.5
A2055-V1
8
7.5
A2075-V1
6
11
A2110-V1
6 or 4
15
A2150-V1
2
22
A2220-V1
1 or 1/0
30
A2300-V1
2/0 or Parallel of 1/0
37
A2370-V1
45
A2450-V1
55
A2550-V1
4/0 (Prepared wire
only) or Parallel of 1/0
18.5
A2185-V1
1
1.8
4.0
4.9
8.8
20.0
19.6
200V
Class
400V
Class
0.4
0.75
A4004-V1
A4007-V1
1.5
A4015-V1
2.2
A4022-V1
3.7
A4037-V1
14(Stranded only)
5.5
A4055-V1
12
7.5
A4075-V1
10
11
A4110-V1
8
15
A4150-V1
6
22
A4220-V1
6 or 4
30
A4300-V1
3
37
A4370-V1
45
A4450-V1
55
A4550-V1
1
2/0
75
B4750-V1
Parallel of 1/0
Parallel of 3/0
90
B4900-V1
110
B411K-V1
132
B413K-V1
18.5
A4185-V1
1.8
4.0
4.9
20.0
35.0
Terminal
Connector
Logic and Analog
connectors
Wiring Size
Range(AWG)
Torque
30~16
30~14
0.16~0.19
0.22~0.25
0.5~0.6
0.37~0.44
Ft·Ibs
(N·m)
Relay connector
Wire Connectors
Field wiring connections must be made by a UL Listed and CSA certified
closed-loop terminal connector sized for the wire gauge involved.
Connector must be fixed using the crimp tool specified by the connector
manufacturer.
Terminal
Cable support
Cable
0194437-6C
AVERTISSEMENT: ne retirez pas le capot avant pendant l’alimentation
et 10 minutes après l’arrêt de l’alimentation. Cela peut entraîner de
grave blessure due à un choc électrique.