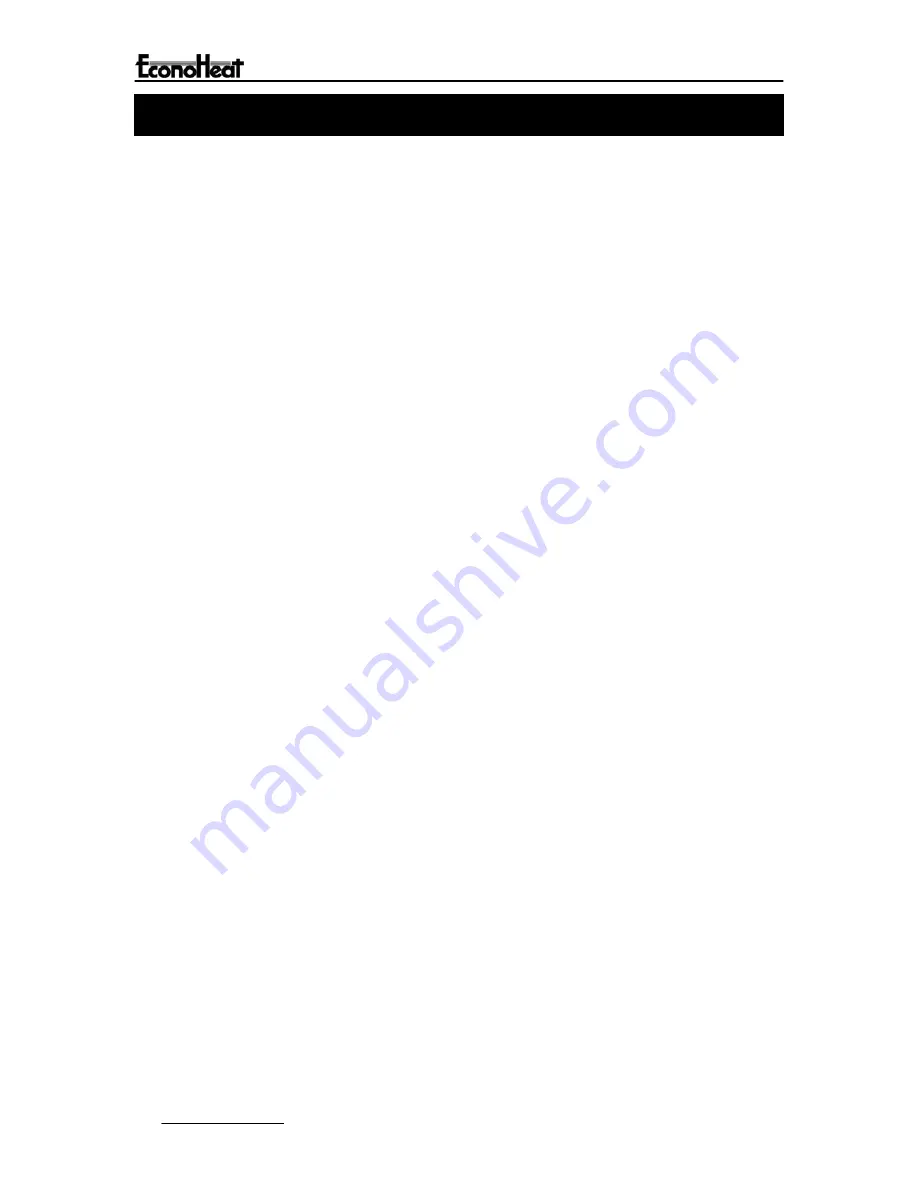
TROUBLE-SHOOTING GUIDE
NO HEAT:
1. Check burner power switch and make sure power is available to the whole control
system.
2. If included in system, check low-water cutoff and/or manual reset high limit.
3. Check room thermostat(s) and zone valves or pump relays (if used).
4. Make sure there is oil in tank.
5. Inquire if reset button on burner oil primary control has been tripped. If reset button
continues to trip then DO NOT ATTEMPT TO START BURNER.
Open burner door by disconnecting the plug-in lead and remove the four hex head
bolts. Examine the combustion chamber for unburned oil and oil vapor. If present,
clean up oil.
With burner door open check cad cell for soot or dirt deposits, check nozzle and if
clogged, replace with nozzle of identical make and style. Check electrodes for proper
gap and for soot or oil deposits. Also check porcelains for cracks.
Close burner door and re-connect electric cord. Press reset button while watching
through the observation port. If burner fires immediately and flame looks good, cycle
several times.
If burner does not fire immediately, or if it fires but flame looks ragged and/or smoky,
shut burner down and check the fuel delivery system. The problem may be air in the
intake line so tighten all fittings and tighten the unused intake port plug. Also check
the filter cover and gasket.
Also check the pump filter and clean it with a brush and fuel oil or kerosene if it looks
dirty.
INADEQUATE HEAT:
1. Check thermostat and heat anticipator setting. A wrong setting can cause short
cycling and inadequate heating.
2. Check to see if the distribution system is airbound. If pump and boiler are running
and the pipe connection to the boiler supply port is hot, check the pipe temperature at
the inlet to the first radiator. If it is cool or only lukewarm, then the problem is lack of
circulation. Look for air in the system, a valve partially closed, a zone valve failed in
the closed position, a pump failure. The most common fault is air in the system.
RELIEF VALVE LEAKS CONSTANTLY:
1. Check
system pressure. With system hot, pressure should be in the 20 psi to 25 psi
range, not to exceed 25 psi. With system cold, pressure should be in the 12-14 psi
range. If pressure is over these ranges, then suspect the pressure reducing fill valve or
the expansion tank. A diaphragm tank may be too small, may have a ruptured
diaphragm (this would cause a very sharp rise in pressure as system water heats up
and a sudden opening of the relief valve) or may be over-pressurized. A closed type
expansion tank may be undersized, may be improperly piped to the boiler, may be
water logged.
2. Relief valve may be defective, or it may have foreign material lodged on the seat.
46
Installation, Operation, And Service Instructions