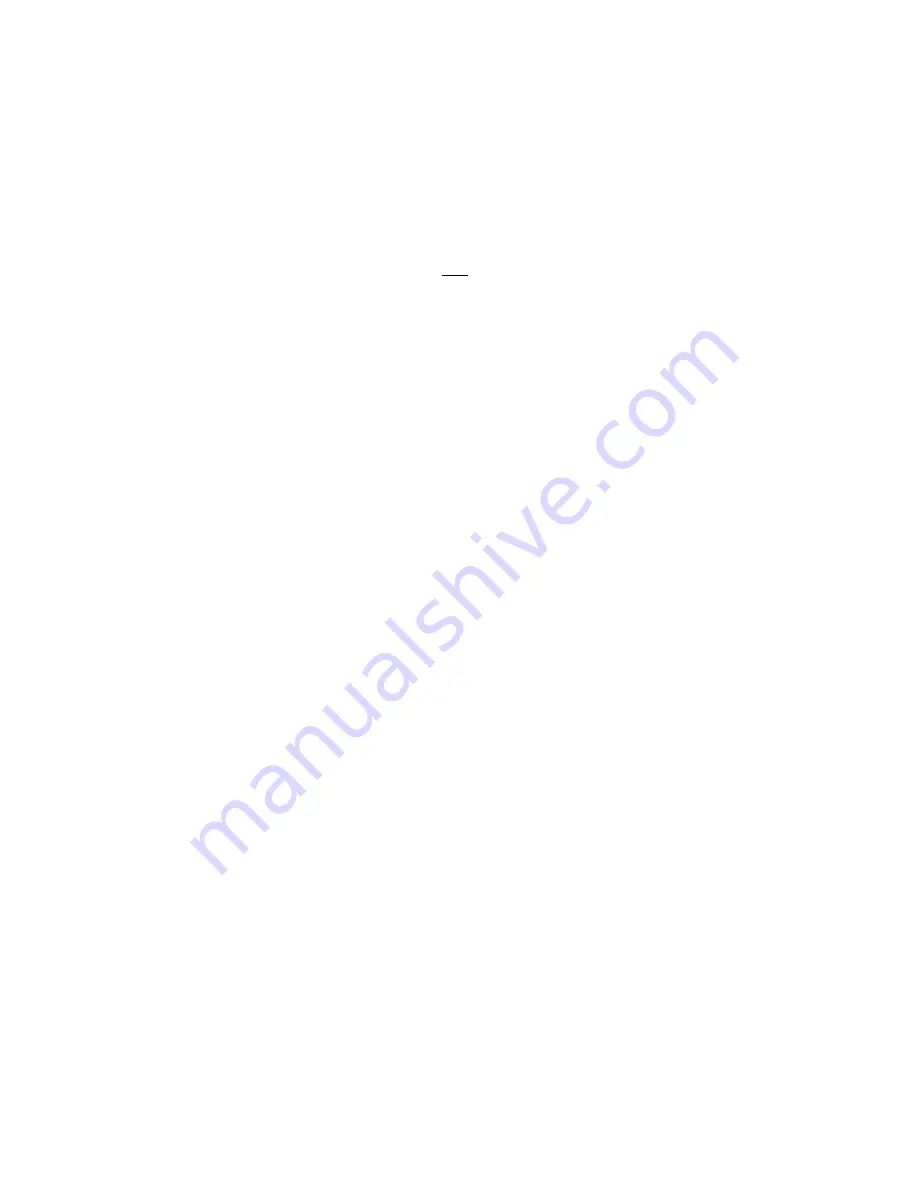
Document number 900-32003 Rev. A
2
IMPORTANT SAFETY NOTICE
Fire Safety Conditional Approvals
A fire safety conditional approval must be issued by an appropriate licensed
electrical engineer for use of this sewer camera in areas of a sewer that have been
demonstrated by testing and monitoring not to fall under the “Fire Safety Approval”
requirement in Section 2540.2 of Title 8 of the California Code of Regulations.
Testing and monitoring will be considered by the California Division of
Occupational Safety and Health, to be sufficient for this purpose if all
measurements indicate that the sewer atmosphere is below 10% of the lower
explosive limit (LEL) and if the user meets all of the following additional
conditions:
(1)
Before each use, inspects cable and electrical equipment for damage or wear
that could compromise safety;
(2)
Test operates the sewer camera and associated electrical equipment in a dry
location away from any potential exposure to hazardous conditions to determine
whether the equipment functions normally and without any problems, such as
sparking, loose connections, or other similar safety problems;
(3)
Tests for the existence of a hazardous atmosphere prior to opening any
sewer access point using a multi-gas tester, and before energizing the equipment,
conducts a test of the sewer atmosphere at the access point estimated to be closest
to the end point of the camera work;
(4)
Provides continuous monitoring in the alarm mode at the access point from
which the work is performed at all times while the sewer inspection camera is
energized in the sewer;
(5)
De-energizes all electrical equipment and uses mechanical ventilation of a
measurement exceeding 10% of the LEL is obtained;
and Discontinues use of all electrical equipment if the sewer environment cannot be
maintained below 10%.
Copyright © 2002 RS Technical Services