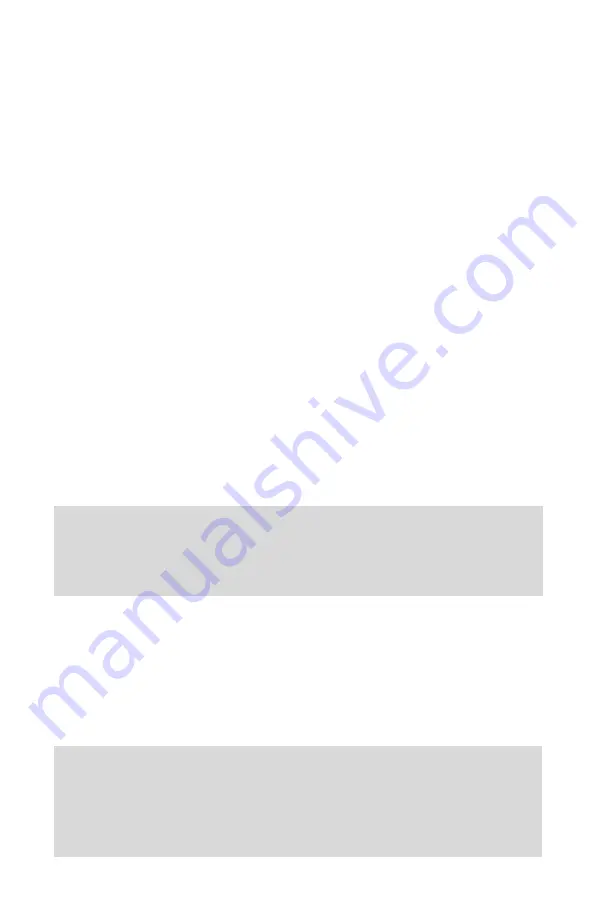
7.2
Calibration of FMA1700A/1800A Mass Flow Meters
All adjustments in this section are made from the outside of the meter, there is no
need to disassemble any part of the instrument.
FMA1700A/1800A Mass Flow Meters may be field recalibrated/checked for the
same range they were originally factory calibrated for. When linearity adjustment
is needed, or flow range changes are being made proceed to step
7.3.
Flow
range changes may require a different Restrictor Flow Element (RFE). Consult
OMEGA
7
for more information.
7.2.1
Connections and Initial Warm Up
At the 9-pin “D” connector of the FMA1700A/1800A transducer, connect the mul-
timeter to output pins [2] and [3] for 0-5 VDC (or pins [8] and [9] for 4-20 mA)-(see
Figure 2.a).
Power up the Mass Flow Meter for at least 30 minutes prior to commencing the
calibration procedure.
7.2.2 ZERO Adjustment
Shut off the flow of gas into the Mass Flow Meter. To ensure that no seepage or leak
occurs into the meter, it is good practice to temporarily disconnect the gas source.
Using the multimeter and the insulated screwdriver, adjust the ZERO potentiometer
[R34] through the access window for 0 VDC (or 4 mA respectively) at zero flow.
14
CAUTION: The minimum voltage on 0-5 Vdc output can be in the range of 7
to 25 mV. Trying to reduce voltage below this level may increase negative
zero shift. This shift may be invisible on devices without LCD display. Stop
R34 zero potentiometer adjustment if voltage on 0-5 Vdc output is in the
range from 7 to 25 mV and does not decrease any lower.
7.2.3 SPAN Adjustment
Reconnect the gas source. Using the flow regulator, adjust the flow rate to 100% of
full scale flow. Check the flow rate indicated against the flow calibrator. If the devia-
tion is less than ±10% of full scale reading, correct the SPAN potentiometer [R33]
setting by using the insulated screwdriver through the access window, to eliminate
any deviation. If the deviation is larger than ±10% of full scale reading, a defective
condition may be present.
LIKELY REASONS FOR A MALFUNCTIONING SIGNAL MAY BE:
✓
Occluded or contaminated sensor tube.
✓
Leaking condition in the FMA1700A/1800A transducer or the gas line and fittings.
✓
For gases other than nitrogen, recheck appropriate “K” factor from the Gas Factor Table.
✓
Temperature and/or pressure correction errors.
Summary of Contents for FMA1700A
Page 28: ...24 APPENDIX 1 COMPONENTS DIAGRAM FMA1700A 1800A METERING PC BOARD...
Page 35: ...31 PARTS OF THE FLOW METER LEFT AND RIGHT VIEWS FRONT VIEW...
Page 36: ...32...
Page 37: ...33...
Page 38: ...34...