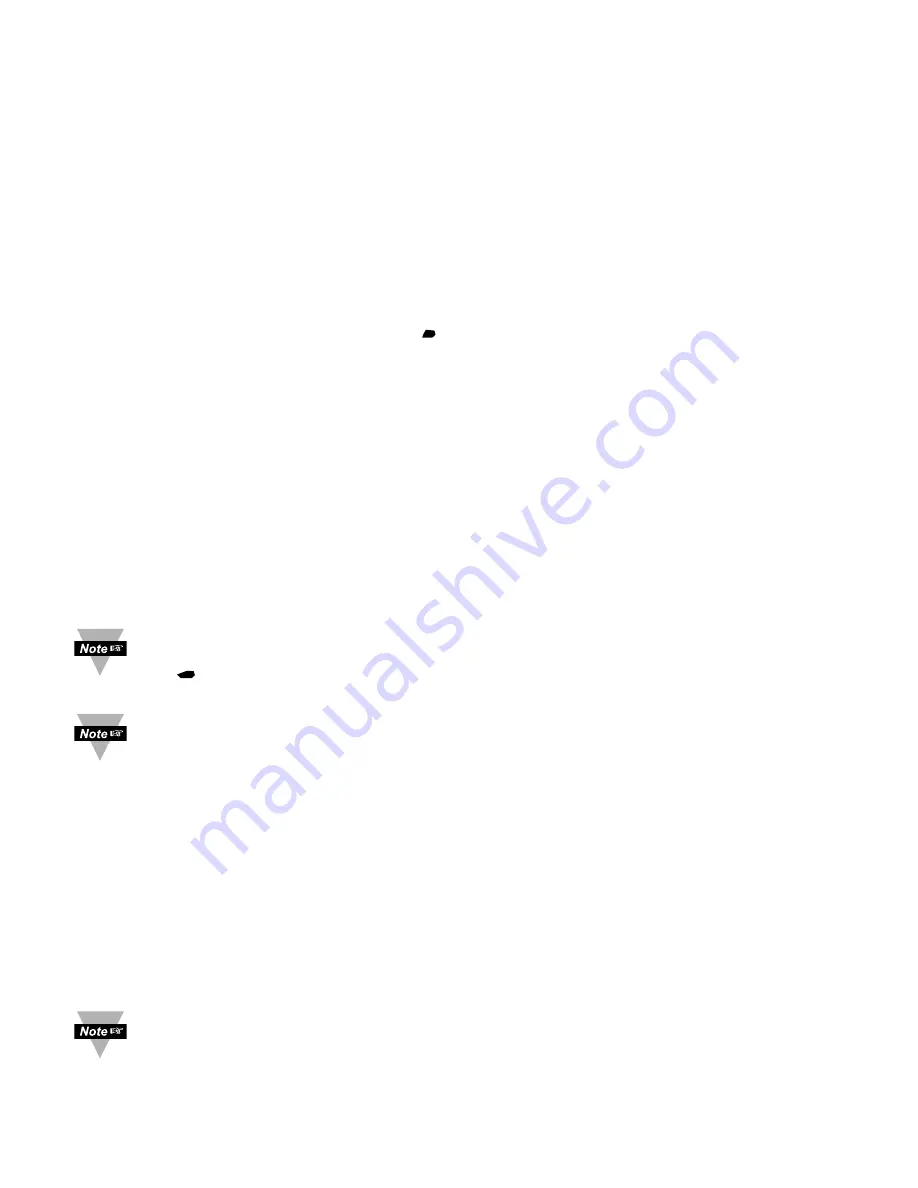
ENTER INPUT TYPE MENU:
Press
a
1)
Press
a
, if necessary, until
CNFG
prompt appears.
Press
d
2)
Display advances to
INPT
Input Menu.
Press
d
3)
Display flashes
0-0.1
,
0-1.0
,
0-10
or
0-20
(0 to 100 mV,
0 to 1 V, 0 to 10 V or 0 to 20 mA).
INPUT TYPE MENU:
Press
b
4)
Scroll through the available selection of input ranges
0-0.1
,
0-1.0
,
0-10
or
0-20
to the selection of your choice.
Press
d
5)
Display shows
STRD
stored message momentarily and then
advances to the
RT1B
Ratiometric Operation Submenu.
Input Types:
100 mV 1 V
10 V
0 – 20 mA
Display:
0-0.1
0-1.0
0-10
0-20
RATIOMETRIC OPERATION SUBMENU:
Press
d
6)
Display flashes previous selection of
ENBL
Enable or
DSBL
Disable.
Press
b
7)
Scroll through the available selection
ENBL
or
DSBL
(flashing).
Press
d
8)
Display shows
STRD
stored message momentarily and then
advances to
RESO
Input/Reading Resolution Submenu.
The Ratiometric operations are typically used for Strain gauge controller.
If your controller is configured as Process (Voltage and Current), set
RTIB
to
DSBL
disable Ratiometric operations.
If
ENBL
Ratiometric operations
Enabled
was selected, the changes to
the excitation voltage will be compensated through Ratio measurement.
If
DSBL
Ratiometric operation
Disabled
was selected, any changes to
the excitation voltage will effect the output of strain gauge bridge and, as
a result, a reading of the controller.
INPUT/READING RESOLUTION SUBMENU:
Press
a
9)
Display flashes previous selection of
LO
Low or
HI
High
resolution.
Press
d
10)
Scroll through the available selection
LO
or
HI
(flashing).
Press
d
11)
Display shows
STRD
stored message momentarily and then
advances to
BUTN
Button Selection Submenu.
If
LO
Low Resolution was selected the resolution of the display is 10 µV.
If
HI
High Resolution was selected the resolution of the display is 1 µV.
In case of High Resolution, the maximum input signal is 10 mV.
18
Summary of Contents for CNiS16
Page 69: ...NOTES 65...
Page 70: ...NOTES 66...