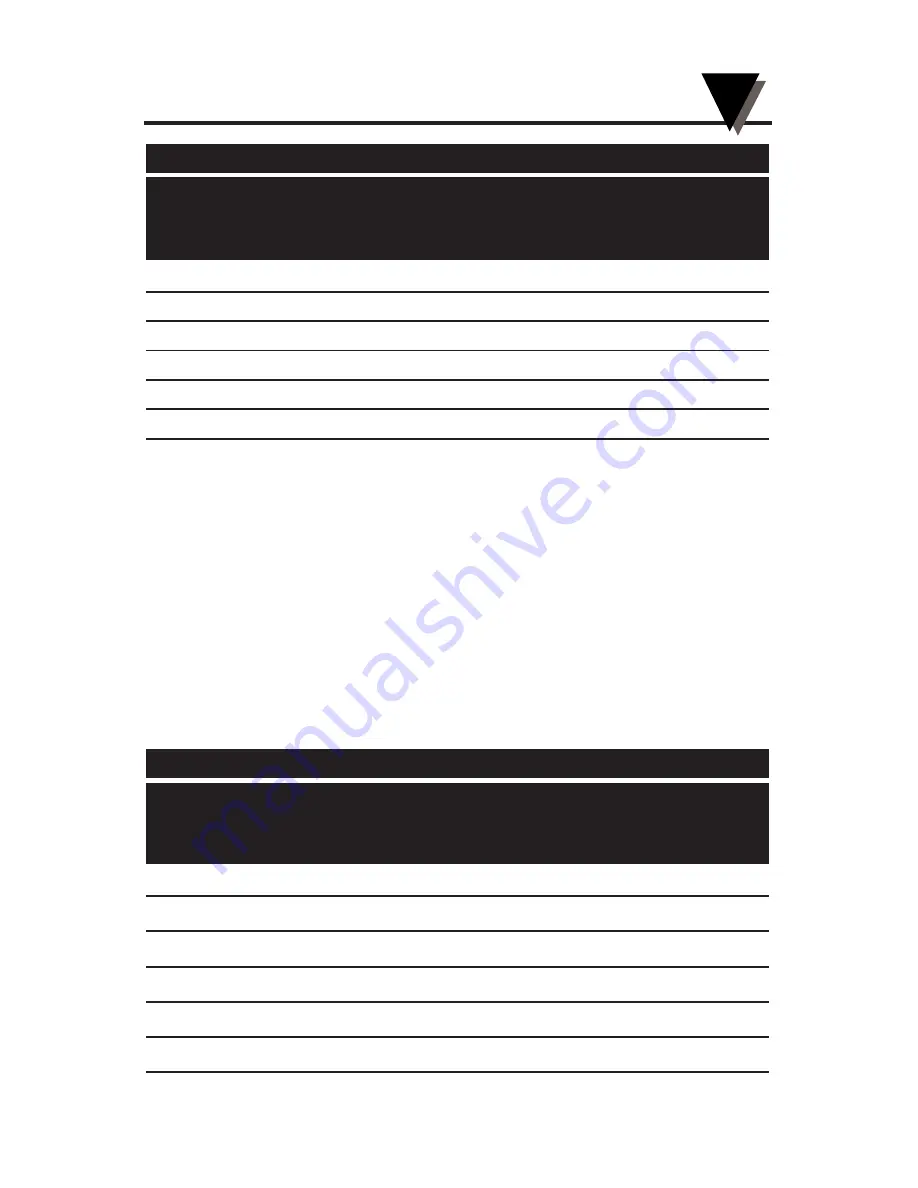
Specifications
9
9-3
Table 9-2. Average Flow Rates (Cont’d)
Tubing Wall
Tubing Size
mL per
Minimum Flow
Maximum Flow
Thickness
Inner Diameter
Revolution
Rate at 600 RPM
Rate at 600 RPM
(mL/Minute)
(mL/Minute)
1.5 mm
3.0 mm
0.8*
8
482
1.5 mm
4.0 mm
1.43*
15
857
1.5 mm
5.0 mm
2.1*
21
1257
1.5 mm
6.0 mm
2.7*
27
1607
1.5 mm
7.0 mm
3.6*
37
2187
1.5 mm
8.0 mm
3.9*
39
2316
* Metric mL per Revolution numbers are rounded off
Normalized flow rates (mL per revolution) vary significantly, based on
motor speed, tubing materials, and mechanical tolerances in pump
dimensions. In addition, the variances are different for the different
tubing dimensions. Variances from the normalized flow rates of Table
9-2 are shown below. The data is shown for new tubing only.
Tubing operating life tests are done at 600 RPM, with 20°C water, 0 PSI
back pressure until the tubing breaks
Table 9-3. Variances in Normalized Flow Rate (mL per Revolution)
Tubing Size
Due to
Between Pumps
Due to Different
Inner Diameter
Motor
(due to Mechanical
Tubing Materials
(in.)
Speed
Tolerances)
1
⁄
32
±10%
±25%
±20%
1
⁄
16
±10%
±15%
±15%
1
⁄
8
±10%
±10%
±5%
3
⁄
16
±5%
±10%
±5%
1
⁄
4
±5%
±15%
±5%
5
⁄
16
±15%
±20%
±10%
Summary of Contents for OMEGAFLEX FPU500
Page 6: ...Index II Notes I...
Page 8: ...Introduction 1 1 2 Notes...
Page 12: ...Parts of the Pump 2 2 4 Notes...
Page 21: ...Setting Up the Pump s 3 3 9 Notes...
Page 23: ...Tubing Information 4 4 2 Notes...
Page 30: ...Operating the Pump 5 5 7 Notes...
Page 34: ...Maintenance 6 6 4 Notes...
Page 38: ...Troubleshooting Guide 7 7 4 Notes...
Page 46: ...Specifications 9 9 6 Notes...