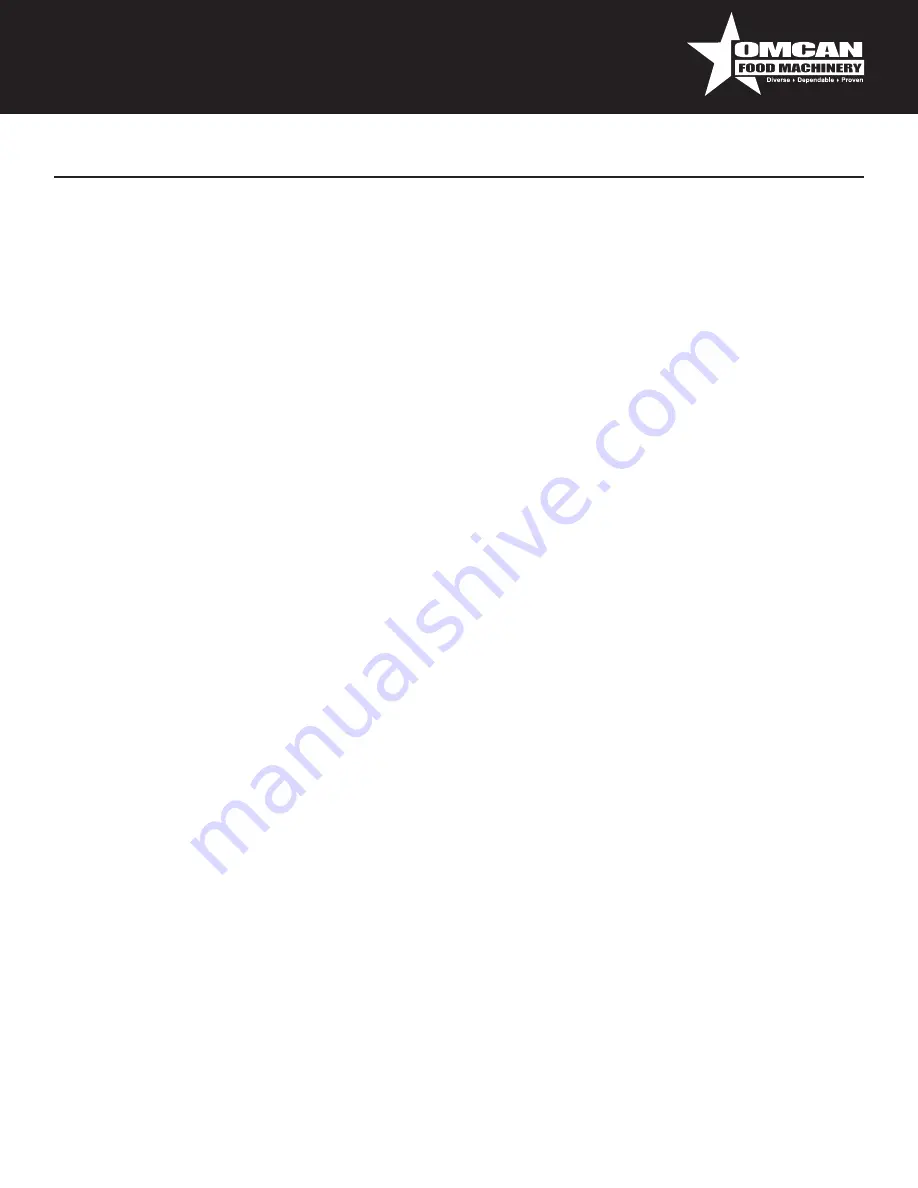
10
Instructions for Field Conversion between LP & NG
CAUTION: ENSURE THE GAS SUPPLY IS SHUT OFF AT THE MANUAL SHUT OFF
VALVE BEFORE PROCEEDING WITH THE CONVERSION.
1. Switch off the gas at the main supply valve and allow the unit to cool down before commencing with the
conversion.
2. Lift off the complete grill plate assembly to expose the burners and valves.
3. Remove the burners by loosening the fastening nuts located under the rear of the burner, lift the rear of the
burner and slide backwards.
4. The brass orifice located on the end of the control valve may now be loosened and removed using a 1/2”
wrench. Replace with the new orifice from the conversion kit, first applying a small amount of jointing paste
to the threat on the end of the valve, this will ensure a good gas tight seal.
5. Replace the burner by sliding the open end over the orifice and then locating the M5 stud through the slot
in the support bracket. Secure by replacing the M5 nut.
6. Replace the burner by sliding the open end over the orifice and then locating the M5 stud through the slot
in the support bracket. Secure by replacing the M5 nut.
7. To operate with LP gas the regulator must be changed to operate at 10” WC. To do this remove the
converter cap and pin from the regulator, remove the pin and invert then reinstall in the cap. Replace the
cap on the regulator taking care that the gasket is in place on the cap.
8. Prior to connecting the regulator, check the incoming line pressure, as the regulators can only withstand a
maximum pressure of 1/2 PSI (13” WC). If the line pressure is beyond this limit, a step down regulator will
be required. The arrow forged into the bottom of the regulator body shows gas flow direction, and should
point downstream to the appliance.
9. Check for gas leaks regularly. A soapy water solution is recommended for locating gas leakage. Matches,
candle flame or other sources of ignition shall not be used for this purpose.
10. Replace the loose fitting grill plate assembly into position.
11. Fix the conversion rating plate supplied in the kit adjacent to the original rating plate on the rear of the unit.
Fill in the details required on the installation plate and fix to the rear of the unit.
Summary of Contents for 37525
Page 12: ...12 Parts Breakdown Model TH RB 1 37525...
Page 14: ...14 Parts Breakdown Model TH RB 2A 37529...
Page 16: ...16...
Page 18: ......
Page 19: ......