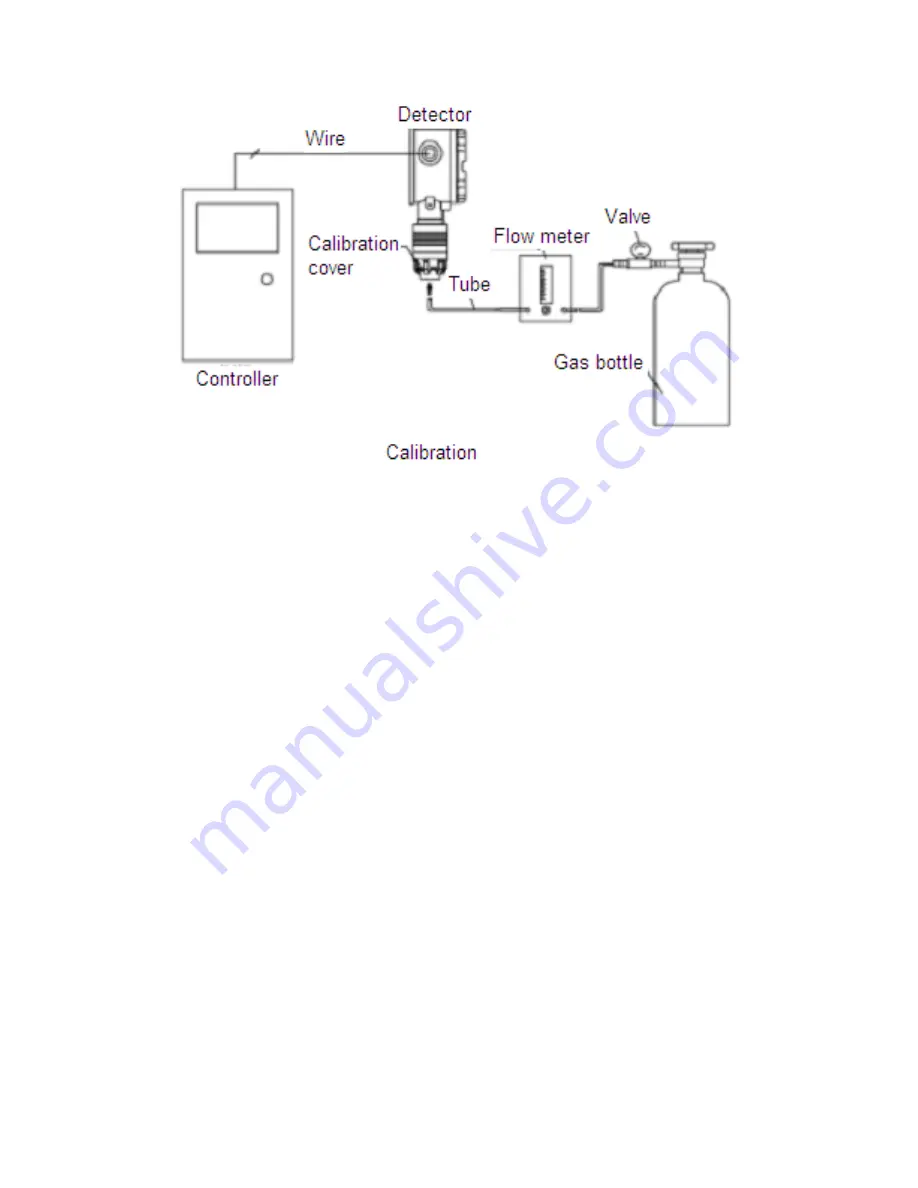
7.4 Calibration of Oxygen Detector
7.4.1 Zero calibration
Disconnect the sensor module from the detector. At the same time, hold
both S2 and S3 buttons continuously for 1-2 seconds, the green power
LED starts to flicker, which indicates the device enters into calibration
status. Adjust the first digit of DIP switch to "ON". Red LED starts to
flicker and green LED is continuously on. After several minutes, resume
the first digit of DIP switch to the original position, and the detector
remembers this value as zero. Red LED flickers several times and then
is off. Zero calibration is completed.
7.4.2 Single Point Calibration (20.9%VOL)
After zero calibration, connect the sensor module to the detector correctly
and electrify the detector. After working for 10 minutes, follow the above
instruction to enter into calibration status. Adjust the second digit of DIP
switch to "ON" (which is 20.9%VOL. Red LED starts to flicker. After
several seconds, resume the DIP switch to the original position and the
detector will remember this value. Red LED flickers several times and
then is off. The calibration is completed.
8. Sensor replacement
In normal working environment, the catalytic sensor life is 3 years and