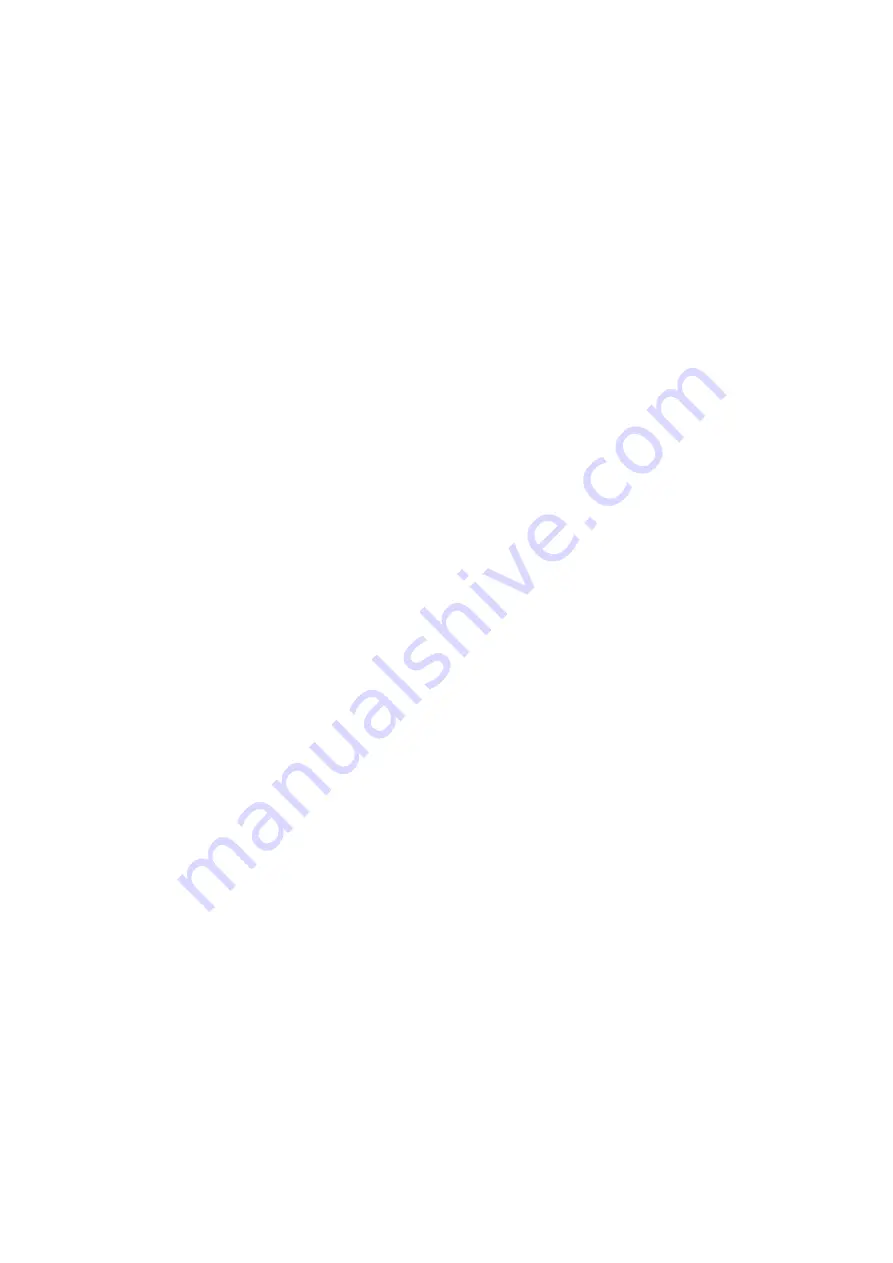
11.
USE PROPER EXTENSION CORD
. Make sure your extension cord is in
good condition. When using an extension cord, be sure to use one heavy
enough to carry the current your product will draw. An undersized cord will
cause a drop in line voltage resulting in loss of power and overheating. Table
1 shows the correct size to use depending on cord length and nameplate
ampere rating. If in doubt, use the next heavier gage. The smaller the gage
number, the heavier the cord.
12.
WEAR PROPER APPAREL
Do not wear loose clothing, gloves, neckties,
rings, bracelets, or other jewelry which may get caught in moving parts.
Nonslip footwear is recommended. Wear protective hair covering to contain
long hair.
13.
ALWAYS USE SAFETY GLASSES.
Also use face or dust mask if cutting
operation is dusty. Everyday eyeglasses only have impact resistant lenses,
they are NOT safety glasses.
14.
SECURE WORK.
Use clamps or a vise to hold work when practical. It’s safer
than using your hand and it frees both hands to operate tool.
15.
DON’T OVERREACH.
Keep proper footing and balance at all times.
16.
MAINTAIN TOOLS WITH CARE.
Keep tools sharp and clean for best and
safest performance. Follow instructions for lubricating and changing
accessories.
17.
DISCONNECT TOOLS
before servicing; when changing accessories, such
as blades, bits, cutters, and the like.
18.
REDUCE THE RISK OF UNINTENTIONAL STARTING.
Make sure switch is
in off position before plugging in.
19.
USE REC
OMM
ENDED ACCESSORIES.
Consult the owner’s manual for
recommended accessories. The use of improper accessories may cause risk
of injury or persons.
20.
NEVER STAND ON TOOL
Serious injury could occur if the tool is tipped or if
the cutting tool is unintentionally contacted.
Summary of Contents for 4620
Page 18: ...FENCE ASSEMBLY 1 5 2 6 3 7 4 8...
Page 19: ...9 13 10 14 11 15 12...
Page 20: ...FENCE ADJUSTMENT TABLE 90 Shaft for 90 ADJUSTING SCREW...
Page 23: ......
Page 24: ......
Page 27: ......
Page 29: ...62 Page Oliver Machinery 4430 Planer Maintenance Record Date Task Operator...
Page 30: ...4430 Planer OLIVERMACHINERY NET 63 Page Notes...