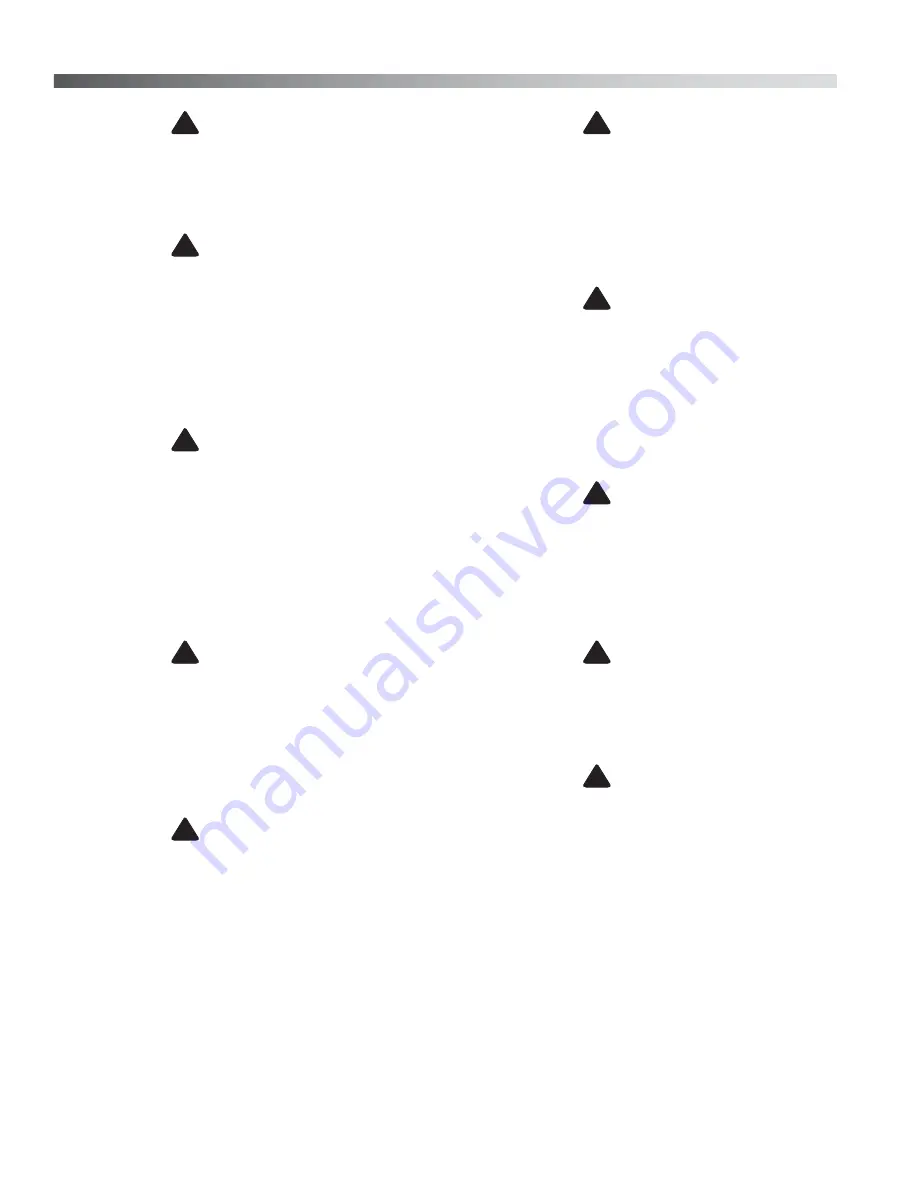
4
THE OILGEAR COMPANY
Bulletin 947023
Hydraulic components can be heavy. Use
caution while lifting these components.
Serious personal injury can be avoided
with proper handling of the components.
Please contact Oilgear if you require
assistance, when performing hydraulic
test procedures, use the proper hydraulic
gauges. Installing an incorrect test gauge
could result in serious injury if the gauge
fails. Use properly rated hydraulic hoses
to allow the test gauge to be read away
from moving parts and functions.
Increasing hydraulic pressure beyond the
recommendations may result in serious
damage to the pump and system or
serious personal injury and may void the
Oilgear Warranty. If you have questions
concerning hydraulic pressures or testing
procedures, please contact Oilgear before
attempting the test procedures or making
adjustments.
An Oilgear pump must not be modified in
any way without authorization from
Oilgear. Modifications may not comply
with safety standards, including ANSI
safety standards, and may result in
serious personal injury. Please contact
Oilgear if you require assistance.
DO NOT enter under hydraulic supported
equipment unless they are fully supported
or blocked. Failure to follow this procedure
can result in serious injury or death.
Any Oilgear pump safety decals must be
replaced anytime they are damaged,
missing, or cannot be read clearly. Failure
to have proper decals in place can result
in serious injury or death. (If you require
safety decals, please contact Oilgear for
replacement safety decals, at no charge.)
Be sure everyone is clear of the area
around the hydraulic system before
operating after servicing. Remain attentive
at all times when operating to check your
work until you are completely sure it is
safe to return to service. Failure to heed
this warning may result in serious
personal injury or death.
Wear the proper protective clothing when
operating, servicing or maintaining the
hydraulic system or the Oilgear pump. Wear
the correct protective gear, safety glasses,
gloves, and safety shoes. Serious injury
can result without proper protective gear.
Make sure to keep hands and feet and
other parts of your body clear of revolving
or moving parts. Failure to comply can
cause serious injury.
DO NOT wear watches, rings, or jewelry
while working with electrical and
mechanical equipment. These items can
be hazardous and can cause serious and
painful injuries if they come into contact
with electrical wires, moving parts, or
hydraulic equipment.
!
WARNING
!
WARNING
!
WARNING
!
WARNING
!
WARNING
!
WARNING
!
WARNING
!
WARNING
!
WARNING
!
WARNING
Safety First